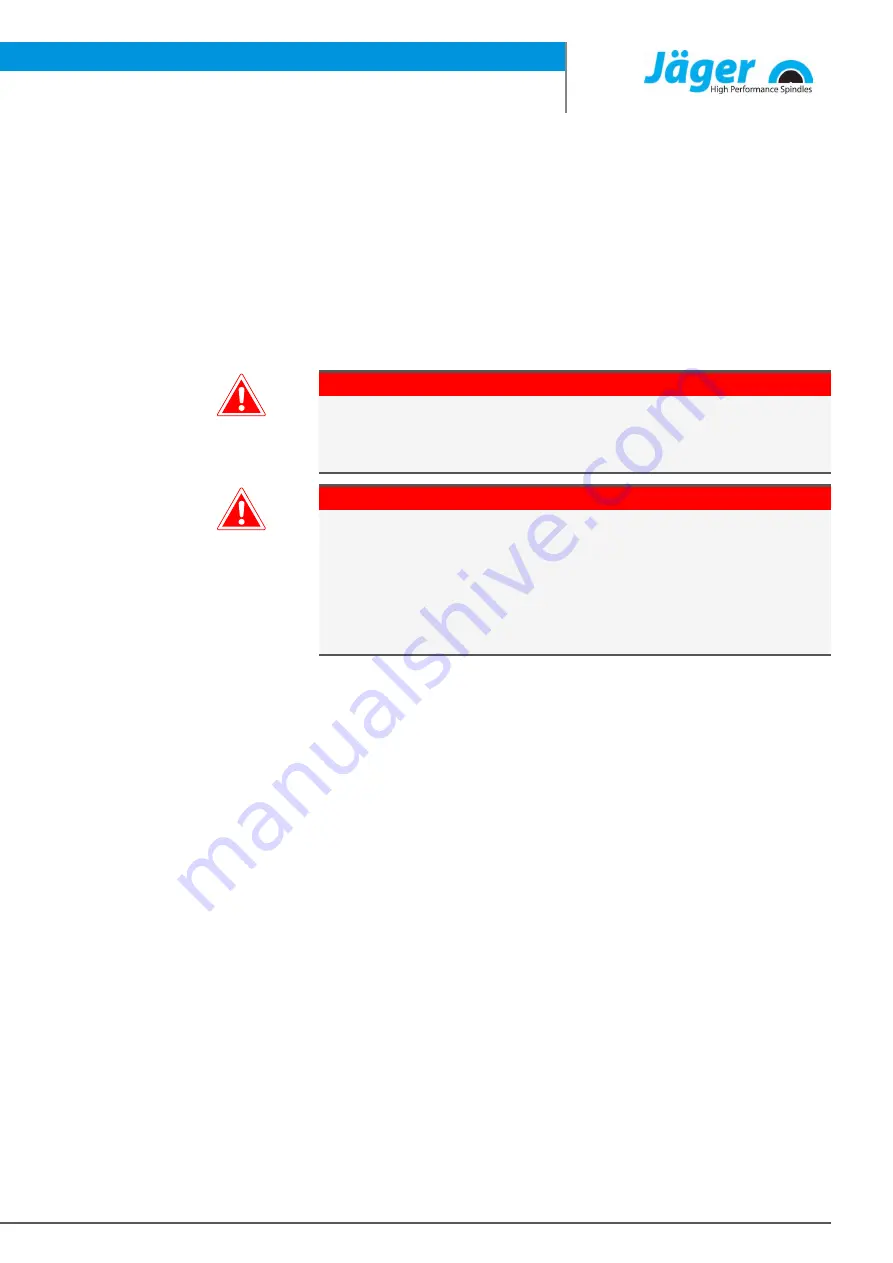
Tools for high speed cutting
Item no. 10004007, Revision 06
25 ( 32 )
The collet is inserted correctly when it is flush with the end face of the clamp-
ing nut. This is the only way in which to guarantee that the collet is also pulled
out when the clamping nut is loosened.
Ü
Insert the tool.
Ü
Make sure that the shank of the clamped tool does not press on the inner
stop of the tool mount once the clamping nut has been tightened.
Ü
To prevent the clamping nut from loosening, tighten it again after a short
period of operation and when the shaft is at a standstill.
11
Tools for high speed cutting
DANGER: Due to flying parts.
If the wrong direction of rotation is used, the tool is damaged when load is
applied. The centrifugal forces cause the broken part to be flung out.
u
Only use tools with the correct direction of rotation for the HF spindle.
DANGER: Due to flying parts.
If the speed is selected incorrectly, the HF spindle or the tool may be de-
stroyed and their fragments may be flung out.
u
Note the maximum speed for the selected tool.
u
Note the maximum speed for the HF spindle.
u
The maximum permissible speed of the HF spindle for commissioning /
processing is always the
lowest
specified speed.
Ü
Only use tools that are technically sound.
Ü
Only use tools with a tool shank diameter that corresponds to the inner di-
ameter of the collet. For example, do not use shanks with a diameter of 3
mm in collets for 1/8” (=3.175 mm).
Ä
Also see the Technical Specifications
Ü
Only use tool shanks with a diameter tolerance of h6.
Ü
Do not use tool shanks with a clamping surface (e.g. Weldon).
Ü
Only use a balanced tool.
Ä
DIN ISO 1940, balance grade 2,5 .