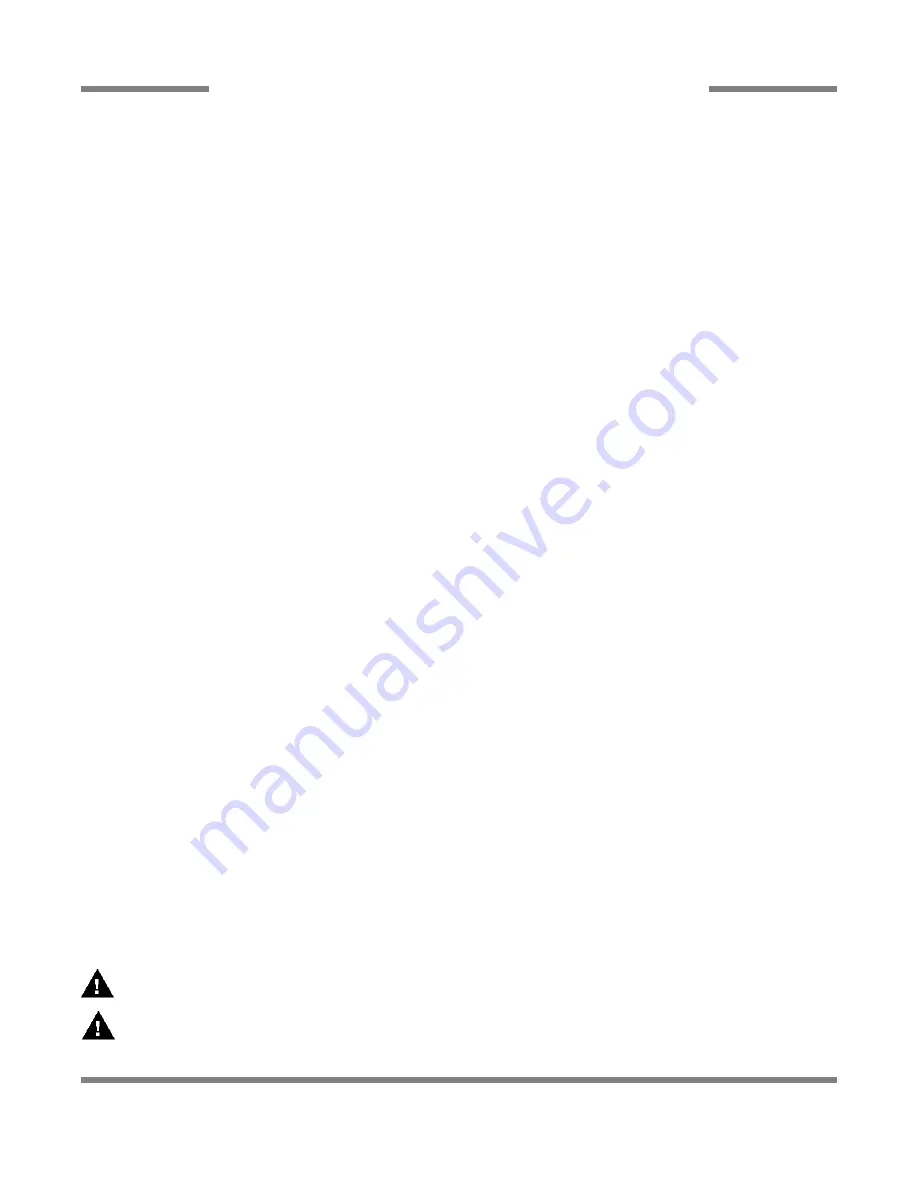
VISUAL INSPECTION:
Before installing the unit, check the container and machine for damage. A damaged container is an indi-
cator that the machine may have been hadled roughly during shipping. If there is damage to both the container and the
machine, do not throw away the container. The machine has been inspected at the factory and is expected to arrive to you in
new, undamaged condition. However, rough handling by carriers or others may have resulted in damage occuring to the
machine. If such a situation does occur, do not return the unit to Jackson. Instead contact both the dealer you purchased the
unit through and the carrier. Ask the carrier to send a representative out to inspect the damage and make a report of it. You
normally have 48 hours to contact a carrier to report damages, but this varies based on locale. The best advice is to contact
your carrier and dealer as soon as damage is discovered.
UNPACKING THE MACHINE:
Once the machine has been removed from the container, ensure that there are no obvious miss-
ing parts. This may not be apparent at first glance. If you discover that a part is missing, contact Jackson MSC Inc. immedi-
ately.
LEVEL THE MACHINE:
1. Position the Whirl Wizard under the sink drainboard.
2. Adjust left to right and front to back.
3. Align inlet and outlet tubes with plumbing from main flow chamber (item 2).
4. To adjust the height, loosen the allen screws in each leg socket connector.
5. Slide leg out to desired height. The drain connection on the machine should be at the same level as the sink drain connec-
tion.
6. Tighten the allen head screws in each leg socket connector.
7. Fine adjustments in height can be made by turning the bullet foot in each leg.
INSTALLING THE MACHINE:
1. Locate the sink at the highest end of the drain slope.
2. Disconnect the existing drain plumbing from the sink.
3. Remove the crumb cup.
4. Clean off old plumber’s putty from the sink. Add fresh putty to the sink flange.
5. Position the main flow chamber (item 2) through the bottom of the sink. From the bottom, slip the rubber washer (item 3),
fiber washer (item 4), back-up flange (item 5) and mounting flange (item 6) on the main flow chamber.
6. Once in position, mount the jam spring (item 7) on to the main flow chamber. This will hold items 3 through 5 in place.
7. Tighten the screws in item 6 until the assembly is held in place. Care must be taken to position screws where they are acces-
sible and will not be covered by the hose barb when assembled into the main flow chamber.
8. In the bottom of the main flow chamber (item 2), install the 1-1/2” NPT close nipple (item 10).
9. The 1-1/2” NPT tee (item 9) is screwed onto the 1-1/2” nipple (item 10).
10. From the tee (item 9) to the drain, install the following items: 1-1/2” close nipple (item 10) and 1-1/2” ball valve (item 11).
Make sure the handle of the ball valve (item 11) is easily accessible by the operator.
11. On the sink side of the tee (item 9) install a 1-1/2” NPT hose barb (item 12).
12. On the inlet side of the main flow chamber (item 2) install a 1” NPT hose barb (item 8).
13. With different styles and types of sinks, the directional manifold (item 1) may require modification. The directional tubing
may need to be bent to conform to the bottom of the sink or reduced in length. Since it is fabricated from thin wall stainless
steel, a hacksaw can be used to cut the tubing.
HOSE CONNECTIONS:
1. Position the 1-1/2” ID intake line hose (item 13) with the Whirl Wizard as xlose to the sink as possible, mark and cut to the
length required.
2. Repeat with the 1” ID discharge line hose (item 14).
3. Connect the intake and discharge line hoses with hose clamps (item 15) to their respective connections.
NOTE: ENSURE THAT THE HOSE CLAMPS ARE TIGHT BEFORE OPERATING THE UNIT.
CAUTION: IF DIRECT FLOOR DRAIN IS UNDER OR NEAR MACHINE, MAKE CERTAIN THAT ADEQUATE PROTEC-
TION IS PROVIDED TO PREVENT WATER SPLATTER FROM DAMAGING THE UNIT.
Whirl Wizard Technical Manual 7610-011-70-65
Issued: 08-20-2007 Revised: N/A
SECTION 2: INSTALLATION/OPERATION INSTRUCTIONS
INSTALLATION INSTRUCTIONS
5
Содержание Whirl Wizard
Страница 7: ...1 SECTION 1 SPECIFICATION INFORMATION ...
Страница 10: ...4 SECTION 2 INSTALLATION OPERATION INSTRUCTIONS ...
Страница 14: ...8 SECTION 3 PREVENTATIVE MAINTENANCE ...
Страница 16: ...10 SECTION 4 PARTS SECTION ...
Страница 19: ...13 SECTION 5 ELECTRICAL DIAGRAMS ...
Страница 22: ...16 SECTION 6 JACKSON MAINTENANCE REPAIR CENTERS ...
Страница 29: ......