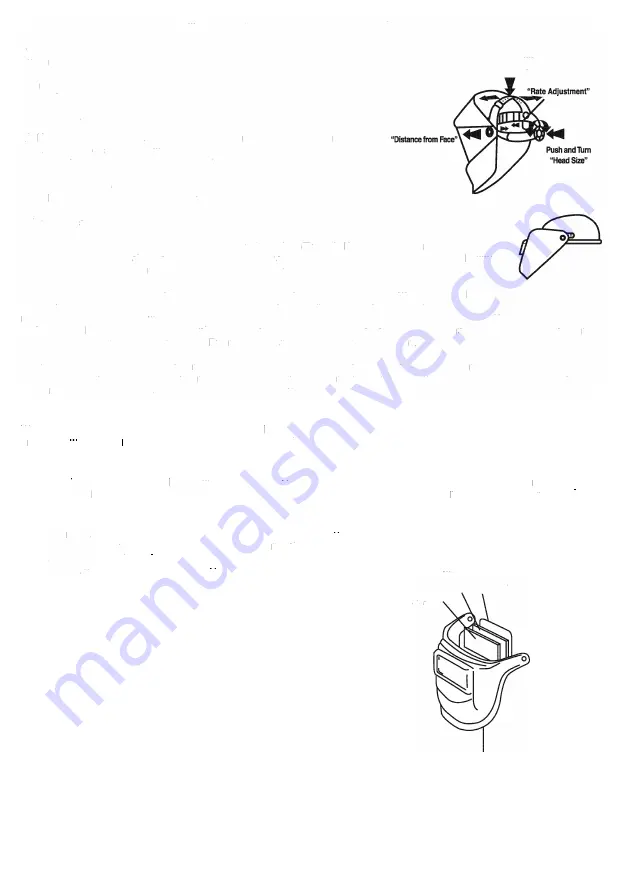
The JACKSON SAFETY
®
WH30 Albatross welding helmets are suitable, but not limited to the following applications:
AC/DC pulses
Inverters WIG/TIG
Stick welding
Argon/Helium
MIG/MAG
protective gas electrodes
Preparation for Operation
JACKSON SAFETY
®
WH30 Albatross welding helmets are fully assembled and ready to
be used after minor adjustments. All welding helmets are equipped
with
a comfortable
headgear that can be adjusted in four different
ways:
• Push and move to adjust the "head height'
• "Rake adjustment" to limit the upper and lower helmet positioning
• Push and turn to adjust the "Head Size"
• Turn to adjust the "Distance from face"
lJm
Puah and move
"H11d Hiighl"
The JACKSON SAFETY
®
WH30 Albatross welding helmets for hard hat (Type: JACKSON SAFETY
®
Hard Hat, product
code J8500 to be sold separately) are equipped
with
a complete fastening mechanism. Fastening the mechanism by
way
of
pushing the pins into the holes provided in the attachment adaptor of the mounting device.
The JACKSON SAFETY
®
WH30 Albatross welding PAPR head tops are designed to
work
exclusively
with
the JACKSON SAFETY
®
AIRMAX
R60
PAPR Blower Unit and are equipped
with
a modified head gear that incorporates an air duct and connector and a face seal to deliver additional
respiratory protection during the welding related activities. Please follow the instructions for use supplied with the AIRMAX R60 PAPR blower unit
(JACKSON SAFETY
®
code J5200, sold separately) to connect the head top the air delivery system. Do not operate or enter the contaminated
area before reading and following these instructions. Failure to do so may lead to serious respiratory injury.
Before commencing work please inspect carefully the welding helmet and the passive glass for any visible marks, cracks, pitted or scratched surtaces;
damaged surfaces even on protection plates reduce vision impair protection. If protection plates are scratched, damaged or built up with spatter
please replace. When changing glass lens please use Protective Gloves.
We recommend you to use the welding helmet for a period of
1
0 years. The duration of use depends on various factors such as way of use, cleaning,
storage and maintenance. Frequent inspections and replacement in case of damage are recommended.
Service and Maintenance
Welding helmets should not be dropped. Do not place heavy objects or tools on or inside the helmet as they might damage the components. If used
properly the welding filter requires no further maintenance during its lifetime.
Cleaning
Clean the shield with mild soap and lukewarm water. Do not use solvents. The welding filter should be cleaned when changing the protection lenses.
This can be done by wiping it with a clean, dry piece of cloth or with a piece of smooth cloth moistened with pure alcohol or a commercial disinfectant.
Replacing the outer spatter lens and welding filter
Lift the flip front place helmet on its top. Remove the screws that hold the protective
lenses and welding filter replace the component(s) and make sure that you put
them back in the same order. Make sure that the
welding filter stays within outer and inner protective lenses.
Outer
Protection
Lena
Welding
Filter
lnntr Protection Lena
Shell
Содержание SureWerx WH30 ALBATROSS
Страница 1: ...WH30 ALBATROSS 0194 ...