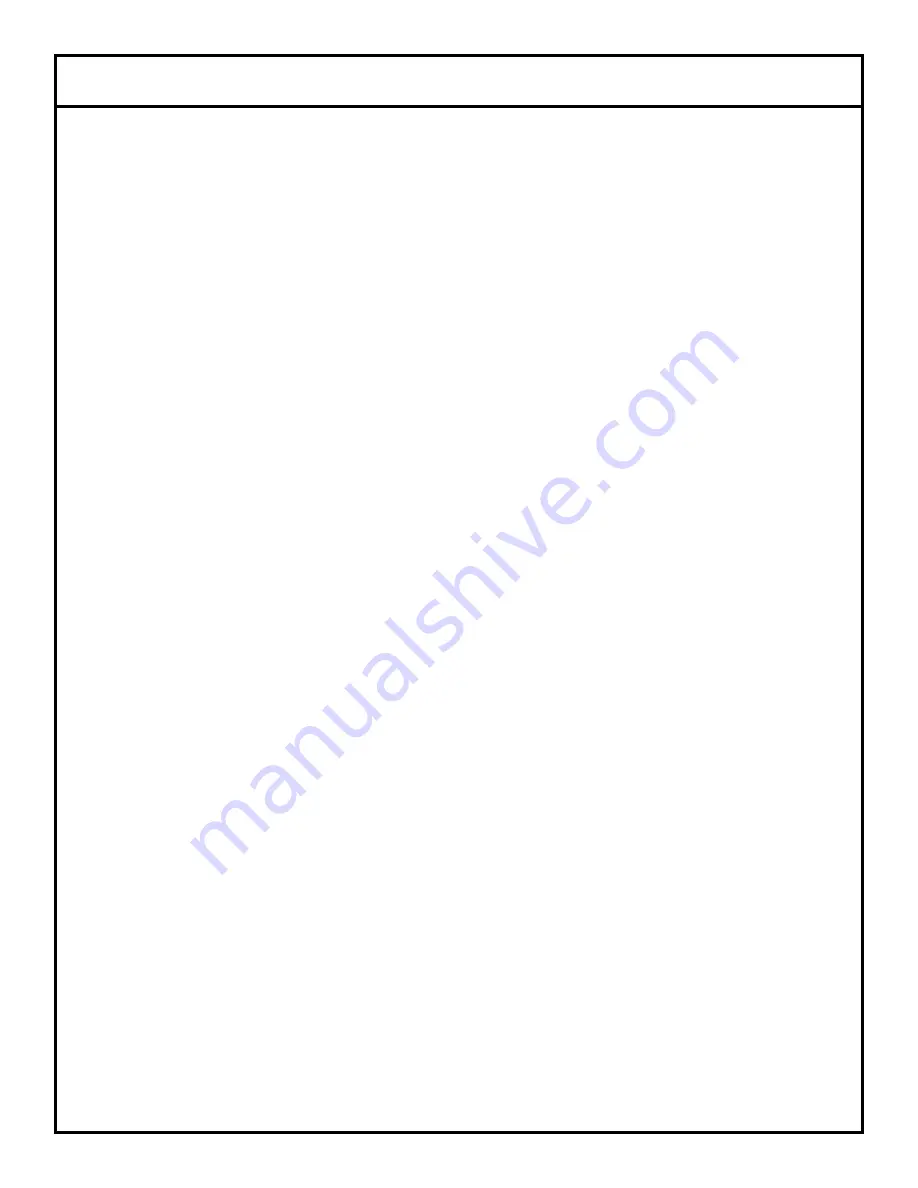
PREPARATION:
Before proceeding with the start-up of the unit,
verify the following:
1. The pump intake, and wash tank strainers are in place
and is clean.
2. The drain stopper is installed.
3. That the wash and rinse arms are screwed securely
into place and that their endcaps are tight. The wash
and rinse arms should rotate freely.
POWER UP:
To energize the unit, turn on the power at the service
breaker. The voltage should have been previously verified as
being correct. If not, the voltage will have to be verified.
FILLING THE WASH TUB:
Ensure that the delime switch is in the
NORMAL position, and place the power switch into the ON posi-
tion. The Tempstar-TGP should fill automatically and shut off
when the appropriate level is reached (just below the wash tank
strainer). Verify that the drain stopper is preventing the wash tub
water from pouring out excessively. There will probably be some
slight leakage from the drain hole. Verify that there are no other
leaks on the unit before proceeding any further. The wash tub
must be completely filled before operating the wash pump to pre-
vent damage to the component. Once the wash tub is filled, the
unit is ready for operation.
The water level was set at the factory. If the water level is not at
the level noted above, it will require adjustment. Check to ensure
that the recommended water pressure is being supplied to the
machine (20 PSI). If the water pressure is correct then the fill
valve will need adjustment. Use the following steps to adjust the
cam. Turn power off at the machine circuit breaker. Open the
control box cover. Locate the timer fill valve cam (Cam 4 from the
timer motor). Locate the spanner wrench taped to the electrical
panel. The spanner wrench is used to adjust the cam.
WARE PREPARATION:
Proper preparation of ware will help
ensure good results and less re-washes. If not done properly,
ware may not come out clean and the efficiency of the dishma-
chine will be reduced. It is important to remember that a dishma-
chine is not a garbage disposal and that simply throwing
unscraped dishes into the machine simply defeats the purpose
altogether of washing the ware. Scraps should be removed from
ware prior to being loaded into a rack.
Pre-rinsing and pre-soaking are recomended, especially for sil-
verware and casserole dishes. Place cups and glasses upside
down in racks so that they do not hold water during the cycle. The
dishmachine is meant not only to clean, but to sanitize as well, to
destroy all of the bacteria that could be harmful to human beings.
In order to do this, ware must be properly prepared prior to being
placed in the machine.
DAILY MACHINE PREPARATION:
Refer to the section entitled
“PREPARATION” at the top of this page and follow the instructions
there. Afterwards, check that all of the chemical levels are correct
and/or that there is plenty of detergent available for the expected
workload.
WARM-UP CYCLES:
For a typical daily start-up, it is recom-
mended to run the machine through 3 cycles to ensure that all of
the cold water is out of the system and to verify that the unit is
operating correctly. To cycle the machine, ensure that the power
is on and that the tub has filled to the correct level. Lift the doors
and the cycle light will illuminate. When the light goes out, close
the doors, the unit will start, run through the cycle, and shut off
automatically. Repeat this two more times. The unit should now be
ready to proceed with the washing of ware.
WASHING A RACK OF WARE:
To wash a rack, open the doors
completely (being careful for hot water that may drip from the
doors) and slide the rack into the unit. Close the doors and the
unit will start automatically. Once the cycle is completed, open the
door (again watching for the dripping hot water) and remove the
rack of clean ware. Replace with a rack of soiled ware and close
the doors. The process will then repeat itself.
OPERATIONAL INSPECTION:
Based upon usage, the wash tank
strainer may become clogged with soil and debris as the workday
progresses. Operators should regularly inspect the wash tank
strainer to ensure it has not become clogged. If the strainer does,
it will reduce the washing capability of the machine. Instruct oper-
ators to clean out the wash tank strainer at regular intervals or as
required by work load.
SHUTDOWN AND CLEANING:
At the end of the workday, close
the doors. When the unit completes the cycle, turn the power
switch to the OFF position and open the doors. Manually remove
the drain stopper from the tub and allow the tub to drain (NOTE:
the wash tank water will be hot so caution is advised). Once the
wash tub is drained, remove the wash tank strainer and the pump
suction strainer. Remove soil and debris from the strainer and set
to the side. Unscrew the wash and rinse arms from their mani-
folds. Remove the endcaps and flush the arms with water. Use a
brush to clean out the inside of the arms. If the nozzles appear to
be clogged, use a toothpick to remove the obstruction. Wipe the
inside of the unit out, removing all soil and scraps. Reassemble
the wash and rinse arms and replace them in the unit. The arms
only need to be hand tight, do not use tools to tighten them down.
Reinstall the strainers and close the doors.
OPERATION INSTRUCTIONS
4
Содержание Gas Heated Door-Type Dishmachines Tempstar...
Страница 31: ...INCOMING PLUMBING ASSEMBLY 29 11 12 13 15 16 10 09 08 07 17 18 19 20 06 05 04 03 02 01 26 25 24 23 22 21 14...
Страница 36: ...STEAM COIL ASSEMBLY 34 01 02 03 05 06 07 08 10 11 12 13 14 15 16 04 09 17 18...
Страница 41: ...Tempstar TGP ELECTRICAL DIAGRAM 208 240 VOLT 50 HERTZ 1 PHASE 39...