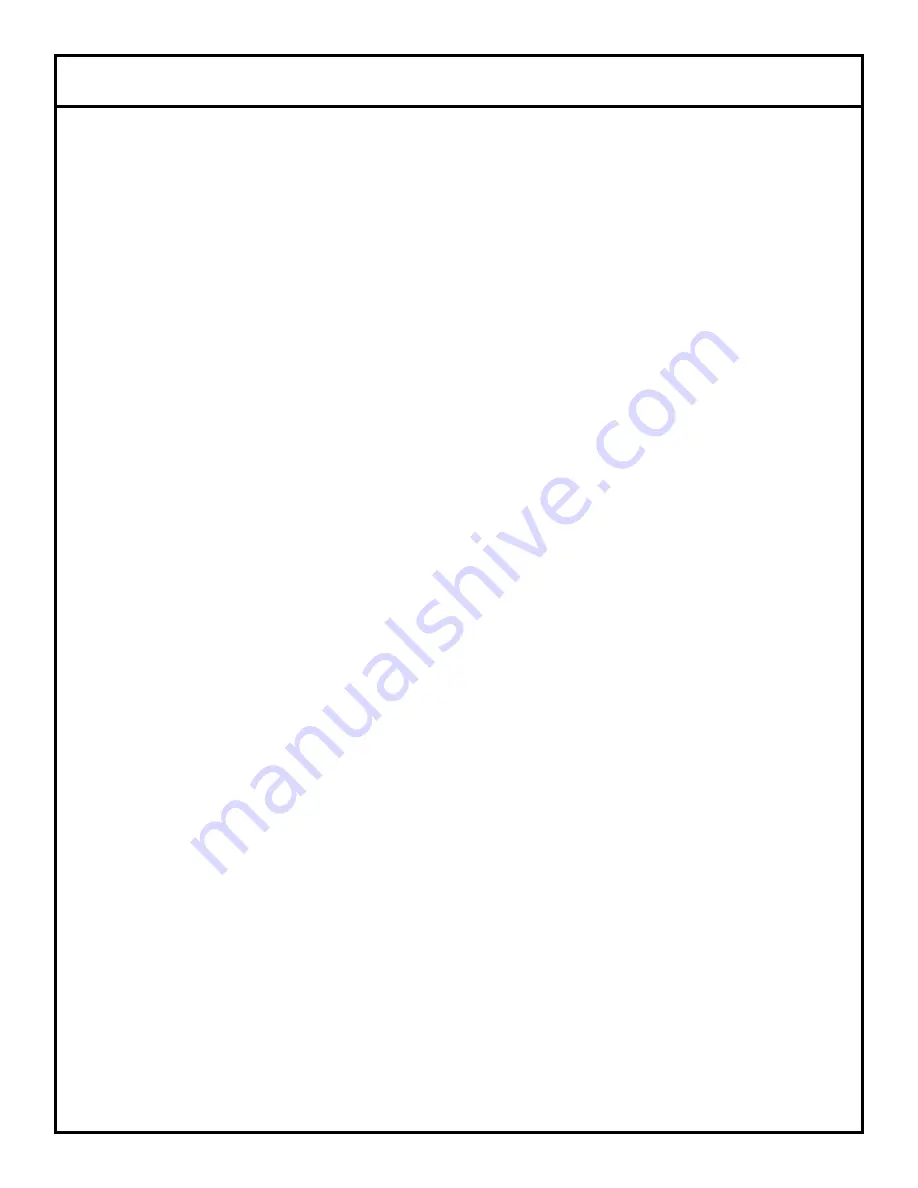
PREPARATION:
Before proceeding with the start-up of the unit,
verify the following:
1. The pan strainer and pump suction strainer are in
place and are clean.
2. The overflow tube and o-ring are installed.
3. That the wash and rinse arms are screwed securely
into place and that their endcaps are tight. The wash
and rinse arms should rotate freely.
POWER UP:
To energize the unit, turn on the power at the service
breaker. The voltage should have been previously verified as
being correct. If not, the voltage will have to be verified.
FILLING THE WASH TUB:
For the initial fill, ensure that the cycle
selection switch is in the “AUTO” (automatic) position, and place
the power switch in the “ON” position. The unit will fill automati-
cally and run through a rinse cycle. Open the doors and verify that
the water level is correct. Hereafter, the water level is controlled by
the overflow tube. Verify that the drain stopper is preventing the
wash tub water from draining excessively. There may be some
slight leakage from the drain hole. Verify that there are no other
leaks on the unit before proceeding any further. The wash tub
must be completely filled before operating the wash pump to pre-
vent damage to the component. Once the wash tub is filled, the
unit is ready for operation.
WARE PREPARATION:
Proper preparation of ware will help
ensure good results and less re-washes. If not done properly,
ware may not come out clean and the efficiency of the dishma-
chine will be reduced. It is important to remember that a dishma-
chine is not a garbage disposal and that simply throwing
unscraped dishes into the machine simply defeats the purpose
altogether of washing the ware. Scraps should be removed from
ware prior to being loaded into a rack.
Pre-rinsing and pre-soaking are required, especially for silverware
and casserole dishes. Place cups and glasses upside down in
racks so that they do not hold water during the cycle. The dish-
machine is meant not only to clean, but to sanitize as well, to
destroy all of the bacteria that could be harmful to human beings.
In order to do this, ware must be properly prepared prior to being
placed in the machine.
DAILY MACHINE PREPARATION:
Refer to the section entitled
“PREPARATION” at the top of this page and follow the instructions
there. Afterwards, check that all of the chemical levels are correct
and/or that there is plenty of detergent available for the expected
workload.
WARM-UP CYCLES:
For a typical daily start-up, it is recom-
mended to run the machine through 3 cycles to ensure that all of
the cold water is out of the system and to verify that the unit is
operating correctly. To cycle the machine, ensure that the power
is on and that the tub has filled to the correct level. Lift the doors
and the cycle light will illuminate. When the light goes out, close
the doors, the unit will start, run through the cycle, and shut off
automatically. Repeat this two more times. The unit should now be
ready to proceed with the washing of ware.
WASHING A RACK OF WARE:
To wash a rack, open the doors
completely (being careful for hot water that may drip from the
doors) and slide the rack into the unit. Close the doors and the unit
will start automatically. Once the cycle is completed, the cycle light
will turn off, open the door (again watching for the dripping hot
water) and remove the rack of clean ware. Replace with a rack of
soiled ware and close the doors. The process will then repeat
itself.
OPERATIONAL INSPECTION:
Based upon usage, the pan
strainer may become clogged with soil and debris as the workday
progresses. Operators should regularly inspect the pan strainer to
ensure it has not become clogged. If the strainer does, it will
reduce the washing capability of the machine. Instruct operators
to clean out the pan strainer at regular intervals or as required by
work load.
SHUTDOWN AND CLEANING:
At the end of the workday, close
the doors. When the unit completes the cycle, turn the power
switch to the OFF position and open the doors. Remove and clean
the pan strainer. Remove the drain stopper from the tub and allow
the tub to drain (NOTE: The wash tank water will be hot so cau-
tion is advised). Once the wash tub is drained, remove the pump
suction strainer. Remove soil and debris from the strainer and set
to the side. Unscrew the wash and rinse arms from their mani-
folds. Remove the endcaps and flush the arms with water. Use a
brush to clean out the inside of the arms. If the nozzles appear to
be clogged, use a toothpick to remove the obstruction. Wipe the
inside of the unit, removing all soil and scraps. Reassemble the
wash and rinse arms and replace them in the unit. The arms only
need to be hand tight, do not use tools to tighten them down.
Reinstall the drain stopper and strainers and close the doors.
WATER CONSUMPTION ISSUES AND EFFICIENCY:
The
Tempstar HH provides you, the customer, with the ability to con-
trol the hourly rack capacity of the machine. Extending the wash
cycle to wash severely soiled ware, such as mixing bowls, does
not increase the machine’s water consumption. However, select-
ing a longer time cycle does lower the amount of dishes the
machine will be able to wash per hour. It is important for operators
to select the correct wash cycle depending on the amount of
washing required. Not every rack of dishes requires the machine
to be set on the longest wash cycle!
Using good prescrapping procedures and observing the results of
individual racks of ware, operators will soon gain the experience
and knowledge required to ensure that the dishmachine operates
at peak efficiency for your needs. Water hardness and detergent
usage will also effect the results of the dishmachine.
It is recommended that owners and operators take the time to
carefully review this section in order to ensure that everything is
done to make sure the Tempstar HH operates at peak perfor-
mance!
OPERATION INSTRUCTIONS
3
Содержание TEMPSTAR HH
Страница 10: ...MAIN ASSEMBLY 8 1 3 4 2 5 6 2 7 8 11 10 12 9 Represents an item not shown...
Страница 19: ...CANTILEVER ARM ASSEMBLY 17 1 2 3 4 5 6 9 10 7 8 18 19 18 21 20 17 14 16 12 15 13 11 12 14 22...
Страница 32: ...30 Tempstar HH ELECTRICAL DIAGRAM 208 230 Volt 60 Hertz Single Three Phase...
Страница 33: ...Tempstar HH ELECTRICAL DIAGRAM 460 Volt 60 Hertz Three Phase 31...
Страница 35: ...Tempstar HH NB ELECTRICAL DIAGRAM 460 Volt 60 Hertz Three Phase 33...