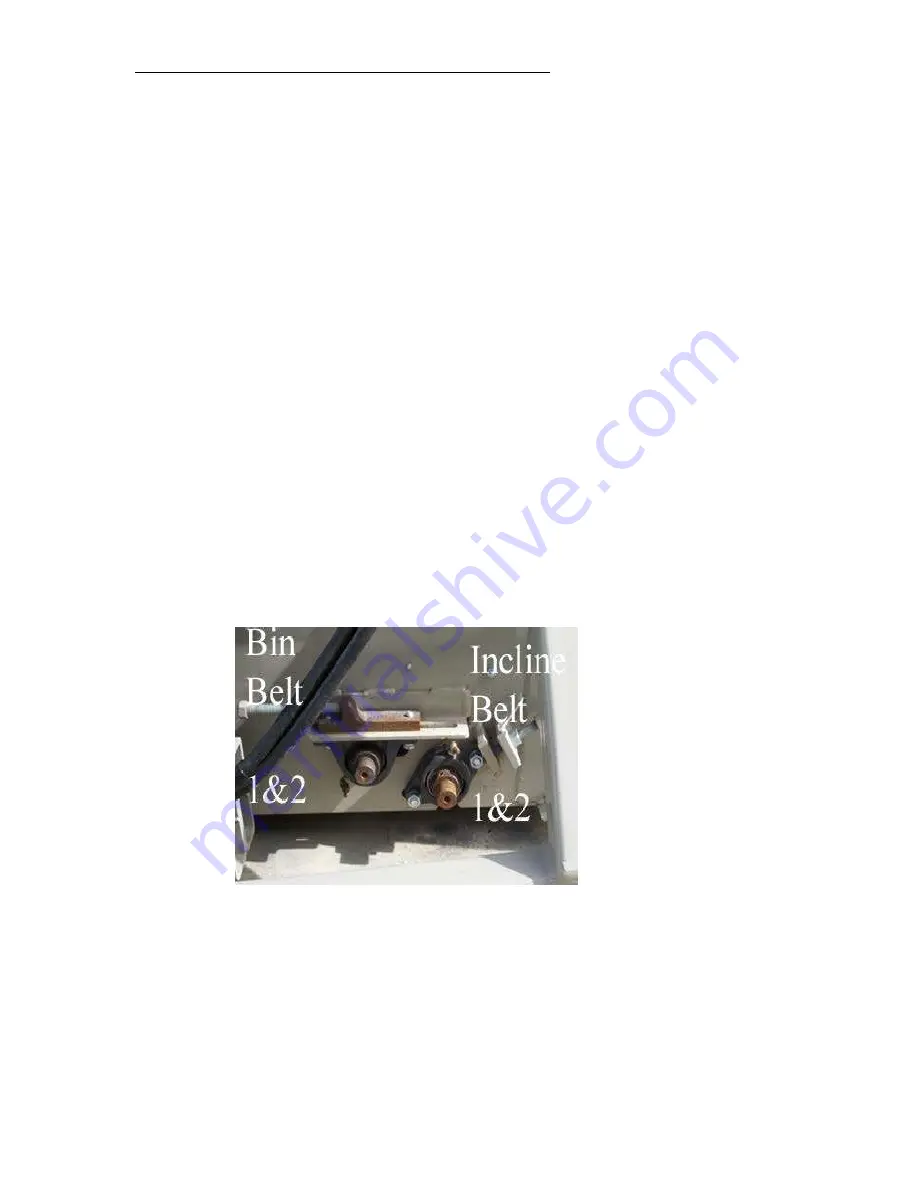
CONVEYOR BELT ADJUSTMENTS INSTRUCTIONS
The tension of the belts should be tight enough to prevent slipping when under maximum load.
Belt alignment and tension are maintained by adjusting bolts that slide the pulley shaft
bearings in the forward and reverse directions. All adjustments should be made in small
increments with the belt running 1 – 2 minutes between adjustments.
1. Change alignment of the belt: Loosen bearing hold-down bolts. Turn the
adjustment bolt to tighten the belt on the side where the belt is too close or
rubbing. Re-tighten bearing hold-down bolts.
A. Run belt at low speed for 1 - 2 minutes allowing belt to center on
pulley. Re-adjust if necessary.
B. Run belt at fast speed for 2 – 3 minutes while checking alignment.
2. Increase belt tension: Loosen bearing hold-down bolts on idler pulley shaft. Turn
adjustment bolts on each side of belt an equal amount increasing belt tension.
Re- tighten bearing hold-down bolts.
A. Run belt at low-speed checking for correct tension and alignment. Re-
adjust if necessary.
B. Run belt at fast speed for 2 – 3 minutes while checking tension and
alignment.
Drive over Belt idler pulley is not shown in above photo. To increase bin belt tension
adjust Idler pulley at front end of bin.
15