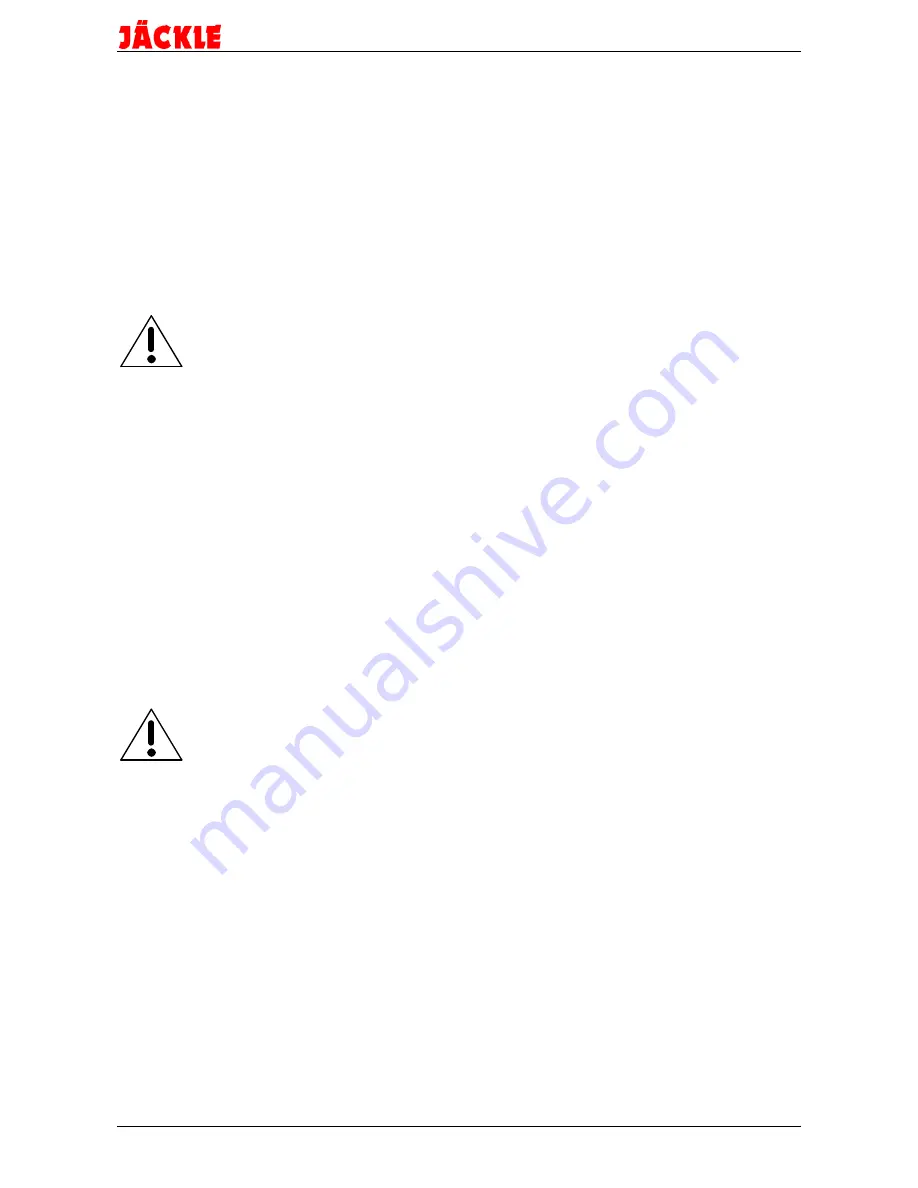
Plasma CUTTER 150
Operating Manual
Page 10
8.
Cutting
8.1 Pilot arc ignition
Bring the nozzle of the cutting torch to the starting point of the cut to be executed.
Press torch trigger. After a short preweld gas flow time the pilot arc is ignited, and at the
instant of the pilot arc impacting the workpiece, the cutting arc is formed.
In the event of a cutting arc failure, the pilot arc is switched off after approx. 3 sec.
Repeated ignition of the pilot arc without actually initiating a cutting process
should be avoided. An overload of the pilot arc resistance might occur, resulting
in unnecessary wear of the torch parts.
8.2 Cutting
In a hand-operated cutting process, move the torch with light contact over the workpiece
at a constant speed.
For achieving an optimum cut, make it a point to keep the right cutting speed correspon-
ding with material thickness. If the cutting speed is too low, a blunt cutting edge will be the
result because of the unduly high thermal input. Optimum cutting speed becomes
apparent when the cutting jet slightly slopes backwards.
At the instant of releasing the torch trigger, the plasma jet is extinguished and the current
source cut off. The gas is post-flowing for approx. 1 minute to cool the torch.
Overshooting the workpiece at pressed torch trigger will initiate the same procedure.
The machine must not be switched off during gas post-flow. Danger of torch
damage by overheating!
In hand-operated hole-piercing, the hand cutter must be held in an inclinded position and
then slowly brought to a vertical position to avoid the formation of spatter.
In machine-operated hole-piercing, bring the cutting nozzle of the machine torch to ap-
prox. 7 - 8 mm distance to the workpiece. Then slowly approach to approx. 4 mm dis-
tance.