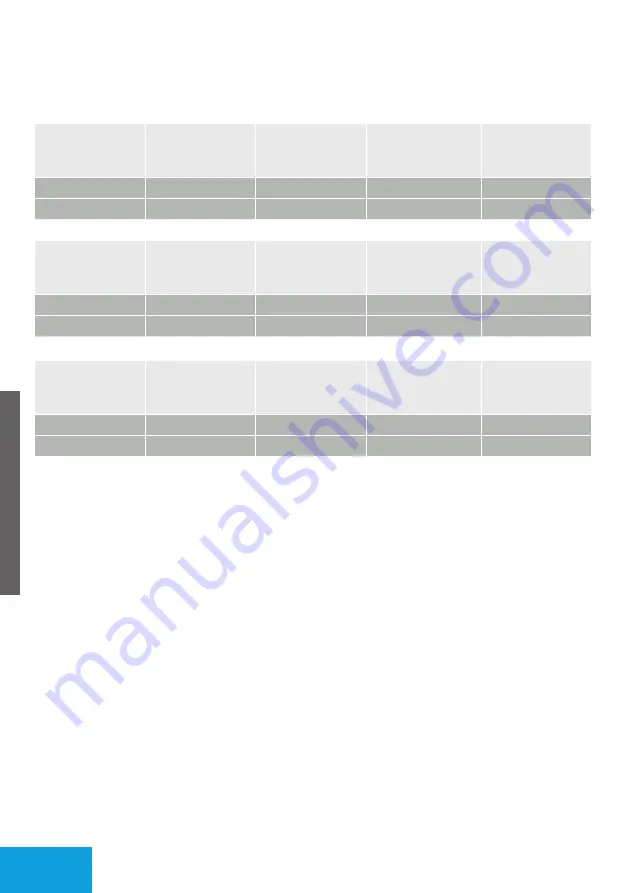
• When preparing for cutting, hold the cutting gun (the cutting gun does not contact the work
-
piece for a model of non-contact arc striking) and press the gun switch; at this time, plasma
arc will eject from the nozzle hole, indicating the electrode, nozzle, etc., are installed correctly.
If there is no plasma arc or only weak plasma arc ejected from the nozzle hole, it indicates the
electrode and nozzle are installed improperly, so reinstallation is necessary after power-on.
• When cutting starts, the outer edge of the nozzle hole should be aligned to the edge of the
workpiece. Press the cutting torch switch to strike the arc; if the arc is not struck, release the
switch and press it again. After successful arc striking, move the cutting torch at a constant
speed to conduct normal cutting (the moving speed should vary from different plate thick
-
nesses; if the sparks upturn, it indicates the moving speed is too fast and the workpiece is not
cut through, and the moving speed should be slower. If the sparks splash vertically to the work
-
piece, it indicates the moving speed is too slow and the adhering slags may increase, and the
speed should be improved properly.
• At the end of the cutting, when the workpiece will be cut off, the cutting speed should be
slowed down, release the cutting torch switch to complete the cutting.
• Splashes adhering to the nozzle surface will affect the cooling effect of the nozzle, so they should
be removed in time, and dust and splashes on the cutting gun head should be removed regu
-
larly so as to maintain a good heat emission effect.
• The cutting torch rack ensures the distance from the nozzle to the plate. Never remove the cut
-
ting torch rack during cutting; otherwise the normal distance from the nozzle to the plate can
not be guaranteed, thus causing the nozzle to touch the plate so as to lead to the gun burned.
3-4.
Notices to Cutting
- Given current :
The cutting power within the specified range of the parameter table, the
corresponding value for the work must be adjusted. The current is adjustable and the
display shows.
3-3.
Working Parameters of Cutter
EN
Air plasma cutting specs for low-carbon steel
Plate
thickness
(mm)
Conduction
nozzle
aperture
(mm)
Cutting
current
(A)
Airflow
(l/min)
Cutting
speed
(m/min)
6
ø 1
30
8
0,24
10
ø 1,2
40
70
0,3
Air plasma cutting specs for stainless steel
Plate
thickness
(mm)
Conduction
nozzle
aperture
(mm)
Cutting
current
(A)
Airflow
(l/min)
Cutting
speed
(m/min)
6
ø 1
30
8
0-2,5
10
ø 1,2
40
70
0-2,5
Air plasma cutting specs for aluminium and aluminium alloy
Plate
thickness
(mm)
Conduction
nozzle
aperture
(mm)
Cutting
current
(A)
Airflow
(l/min)
Cutting
speed
(m/min)
6
ø 1,2
40
10
0-30
10
ø 1,5
100
70
0-30
28
Содержание CUT 50 CNC PILOT
Страница 1: ...R CUTTING EDGE WELDING HASZNÁLATI UTASÍTÁS IGBT inverter technológiás plazmavágógép CUT 50 CNC PILOT ...
Страница 31: ......
Страница 32: ......
Страница 33: ......
Страница 34: ...www iweld hu ...