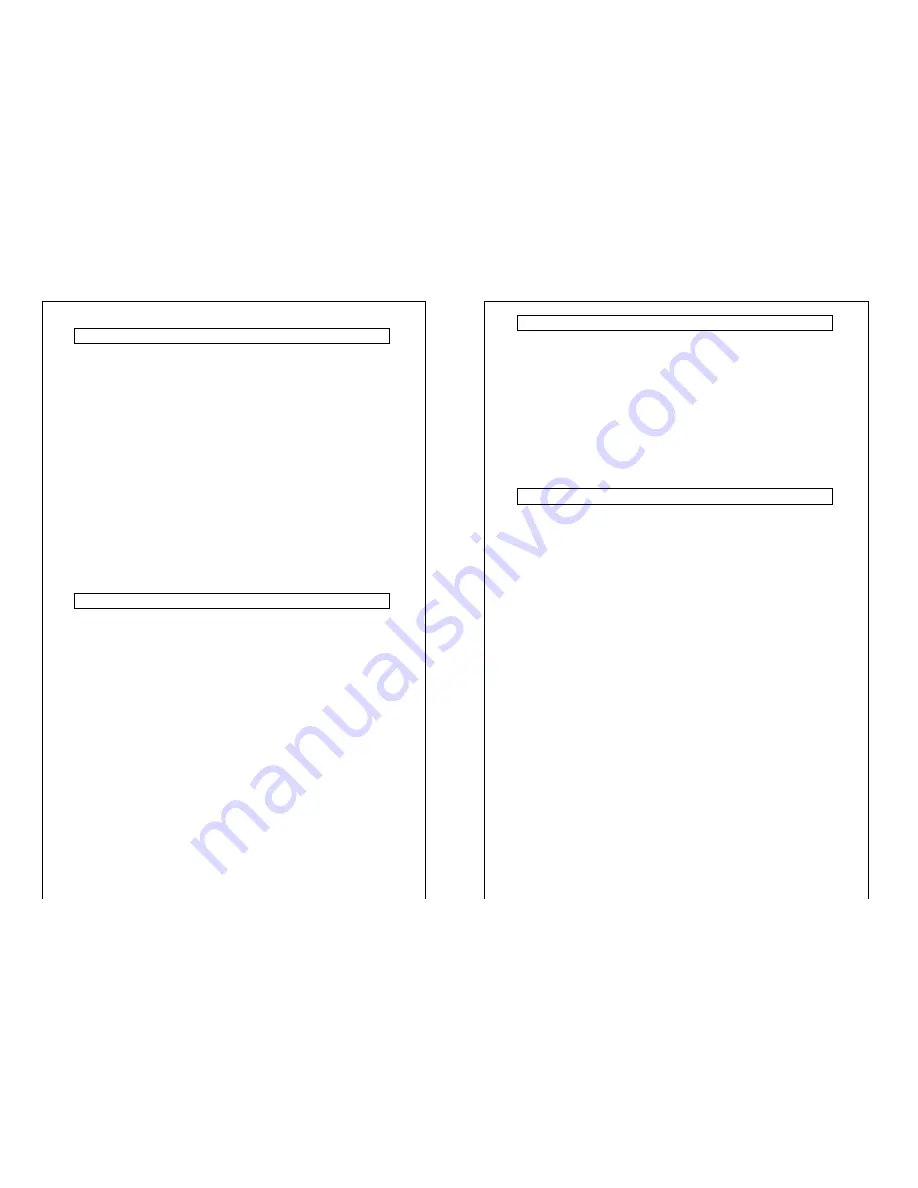
FIRST START UP
After performing the preliminary checks, to power on the boiler it is
necessary:
-
that the boiler thermostat on the control panel is set between 60 and 90°C,
according to the type of heating plant;
- that the environment thermostat is set on 20°C approx.;
- that the main switch is turned "ON";
-
that the main switch is pressed from the control panel (the lighting button is
lightened);
The appliance will run an ignition cycle which will last until set temperatures
have been reached.
After this operation has been completed, the system will run automatically.
FIRST START UP AND FURTHER CHECKS
After the start up operations have been carried out, the appliance must be
tested for standstill and further start up. Therefore:
- modify the boiler thermostat setting;
- actuate the main switch from the control panel;
- modify the environment thermostat setting.
Check the seal of all gaskets on the water and smoke sides.
This operation is of fundamental importance for the gaskets of the door, of the
burner plate and of the smokebox to prevent leakage of toxic and therefore
hazardous combustion fumes into the boiler room. To guarantee the perfect
seal, warm tighten.
The weight of the overhanging burner tends to loosen the gasket of the door at
the top.
IDENTIFICATION ELEMENTS
The appliance can be identified through the TECHNICAL PLATE that
contains the performing values and identification data.
The plate is applied in the front right upper part.
For any servicing and spare part the correct identification of the boiler model
will facilitate all operations.
IMPORTANT: ensure that the technical plate has been applied onto the
boiler: if not, ask your installation technician to apply it.
SPARE PART LIST
Spare parts recommended for two working years:
1 working thermostat 1 safety thermostat
1 door gasket 1 smoke box gasket
1 pilot flame glass 1 pilot flame gasket
1 burner plate gasket
The following parts may also be supplied in the event of accidental damage or
malfunctioning:
- thermometer
- complete control panel
- complete door
- complete smoke chamber
- complete or partial casing
- complete set of turbolators
Содержание SUPERAC 1045 SUPERAC 1220
Страница 2: ......
Страница 5: ......
Страница 6: ......
Страница 8: ......
Страница 9: ......
Страница 11: ......
Страница 12: ......
Страница 14: ......
Страница 15: ......
Страница 17: ......
Страница 19: ...Weight in empty conditions 2100 2350 3450 3850 5200 5800 8000 kg ...
Страница 20: ......
Страница 22: ......
Страница 23: ......
Страница 25: ......
Страница 27: ......
Страница 28: ......
Страница 30: ......
Страница 32: ......
Страница 34: ......
Страница 35: ......
Страница 38: ......
Страница 39: ......