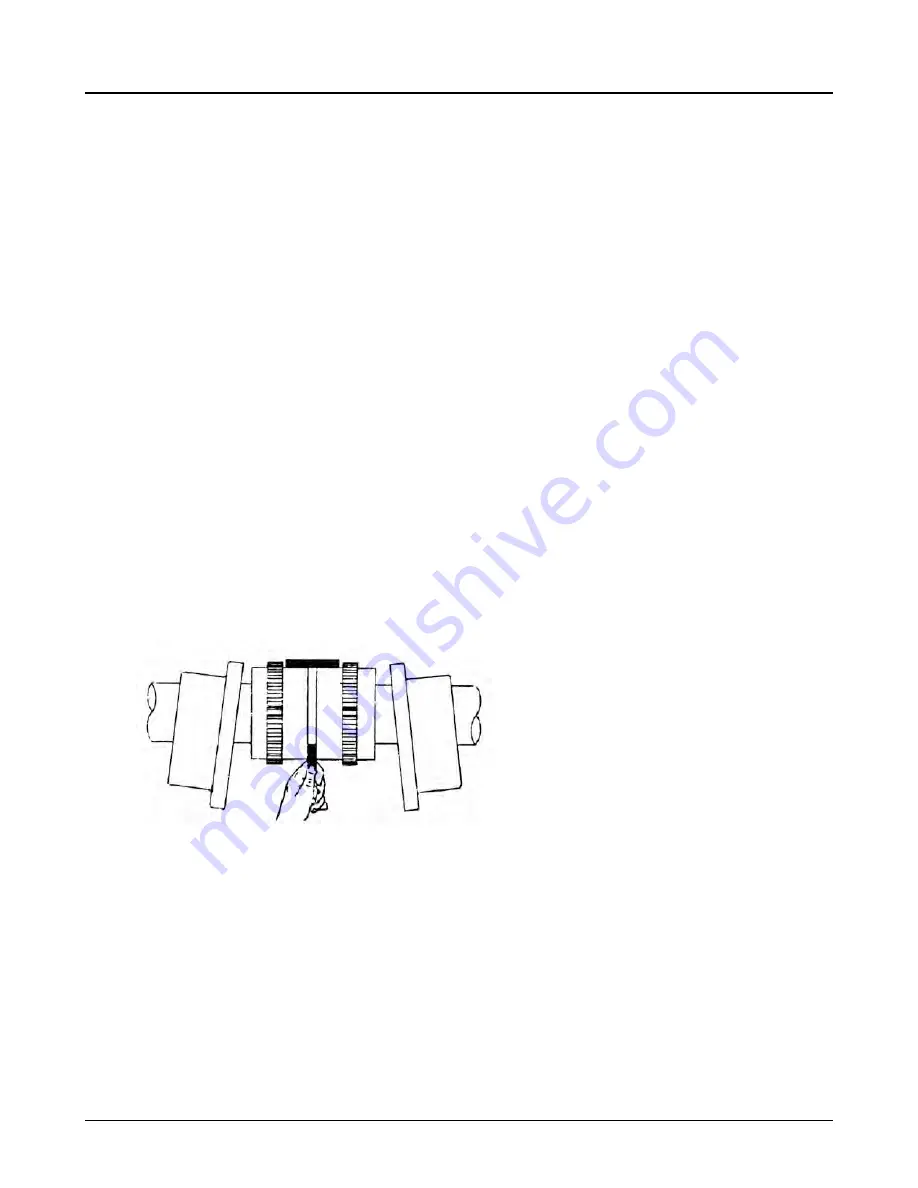
When the units are lined up cold, it may be necessary to make an allowance for the vertical rise of the
driver and/or pump caused by heating. Goulds Pumps recommendations should be obtained and fol-
lowed.
3.5.3 Alternate method of alignment
An approved method for putting the coupling halves in final accurate alignment is by the use of a dial
indicator. Check alignment by straight edge, taper gauge or feelers as accurately as possible by the pro-
cedure indicated above.
Bolt the indicator to the pump half of the coupling, with the indicator button resting on the other half cou-
pling periphery, set the dial to zero, and chalk mark the coupling half at the point where the button rests.
For any check, top, bottom, or sides, rotate both shafts by the same amount; i.e., all readings on the dial
must be made with button on the chalk mark.
The readings will indicate whether the driver has to be raised or lowered or moved to either side. After
each movement, check to see that coupling faces remain parallel to one another.
With this method, accurate alignment of shaft centers can be obtained even where faces or outside di-
ameters of the coupling halves are not square or concentric with the bores, provided all measurements
for angular alignment are made between the same two points on the faces, and all measurements for
parallel alignment are made between the same two points on the outside diameters. Gross deviations in
squareness or concentricity, however, may cause problems due to coupling unbalance or abnormal cou-
pling wear and may need to be corrected for reasons other than accomplishment of shaft alignment.
3.5.4 Alignment of gear type couplings
Gear type couplings are aligned in the same manner as outlined above. However, the coupling covers
must be moved back out of the way and measurements made on the coupling hubs as shown
Gear cou-
pling alignment
.
Figure 9: Gear coupling alignment
3.5.5 Factors that may disturb alignment
The unit should be checked periodically for alignment. If the unit does not stay in line after being properly
installed, the following are possible causes:
•
Settling, seasoning or spring of the foundation.
•
Wear of the bearings.
•
Pipe strains distorting or shifting the machine.
3.5 Pump-driver alignment
18
Model JC Installation, Operation and Maintenance Instructions
Содержание Goulds Pumps JC
Страница 1: ...Installation Operation and Maintenance Instructions Model JC ...
Страница 2: ......