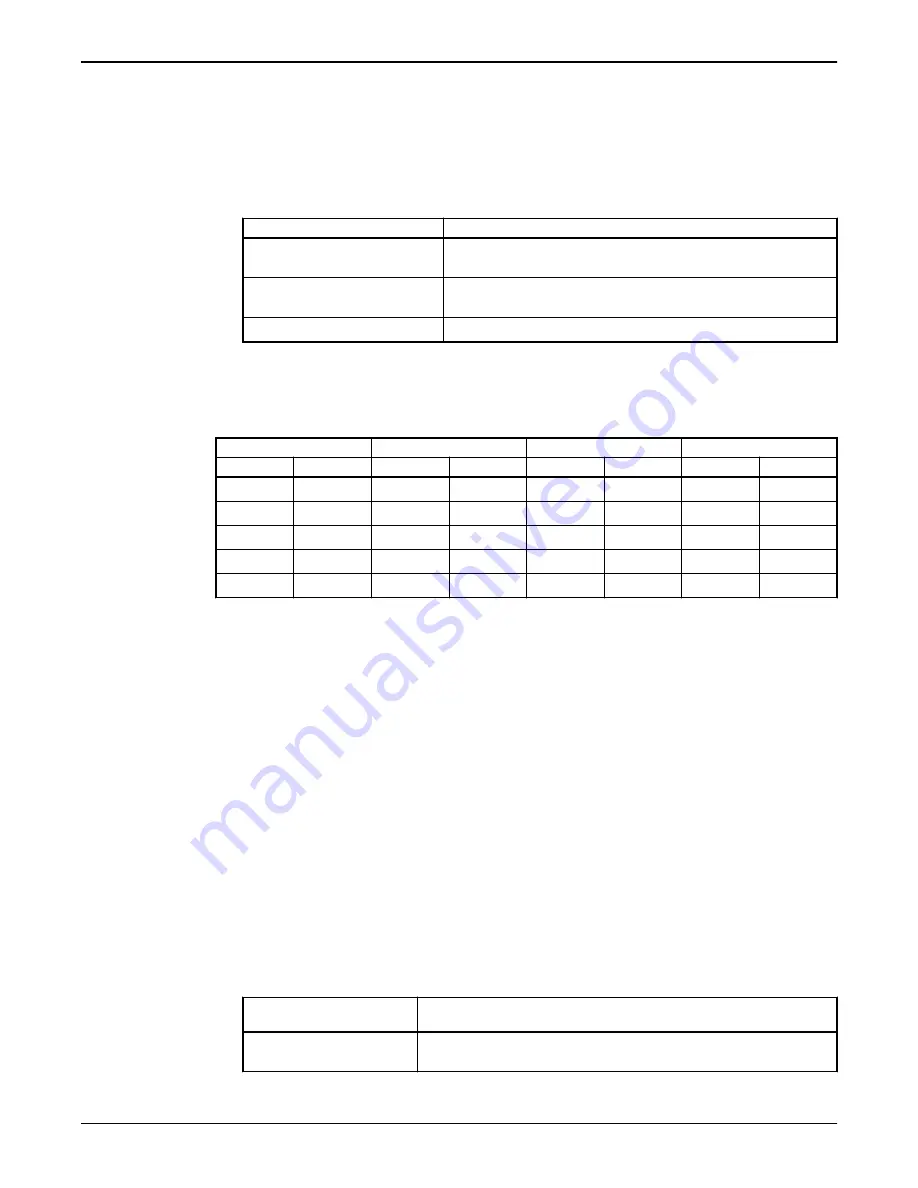
3. Tighten the bonnet fasteners in a crisscross pattern.
For more information, see Fastener torque table for valve body to topworks in this manual.
4. Make multiple crisscross passes to build up torque to the final table value. Make additional crisscross
passes using final table values to evenly tighten each fastener to within 5% of torque value.
5. Retighten the bonnet fasteners as noted above at ambient conditions after the system has cycled
through operating pressure and temperature.
6. Monitor the valve for leakage:
If leakage ...
Then ...
Occurs at the body/bonnet
flange sealing area
Depressurize the system and retighten the bonnet fasteners as
noted above.
Continues
Depressurize the system and retighten the bonnet fasteners as
noted above. (maximum 3rd re-torque)
Continues
Replace the valve diaphragm.
For more information, see Replace the valve diaphragm in this manual.
Fastener torque table for valve body to topworks
Values given are for lubricated fasteners.
Valve size
Bolt size
PTFE diaphragm
Elastomer diaphragm
Inch
DN
Imperial
Metric
in-lb
N-m
in-lb
N-m
0.50
15
1/4"
M6
25-60
2.8-6.8
20-40
2.3-4.5
0.75
20
1/4"
M6
50-65
5.7-9.1
20-50
2.3-5.7
1.00
25
5/16"
M8
65-90
7.4-11.3
45-70
5.1-7.9
1.50
40
3/8"
M10
200-225
23-25
75-130
8.5-14.7
2.00
50
7/16"
M12
225-275
25-31
100-180
11-20
Guidelines
• Minimum values given will provide a longer diaphragm cycle life for valves in non-autoclave and low
thermal cycle conditions.
• Maximum values given may be necessary for autoclave conditions and for high thermal cycle
conditions.
• Torques should be applied at near ambient conditions (less than 100ºF (38ºC)).
Disassemble the valve
1. Remove all line pressure.
2. Do you have a switch package?
• If yes: Proceed to step 3.
• If no: Proceed to step 5.
3. Do you have a fail open or double acting actuator?
• If yes: Proceed to step 4.
• If no: Proceed to step 5.
4. Do you have a series 33 actuator or adjustable opening stop?
• If yes: Remove the switch package.
• If no: Proceed to step 5.
5. If the actuator mode of operation is fail open or fail close, then load the actuator with air.
If the actuator mode of
operation is ...
Then ...
Fail open
Load the air port in the upper cover of the actuator with sufficient air
to partially close the valve.
Maintenance
8
Advantage
®
Actuator 2.0 Maintenance Manual
Содержание Advantage Actuator 2.0
Страница 1: ...Industrial Process Maintenance Manual Advantage Actuator 2 0...
Страница 2: ......
Страница 21: ......