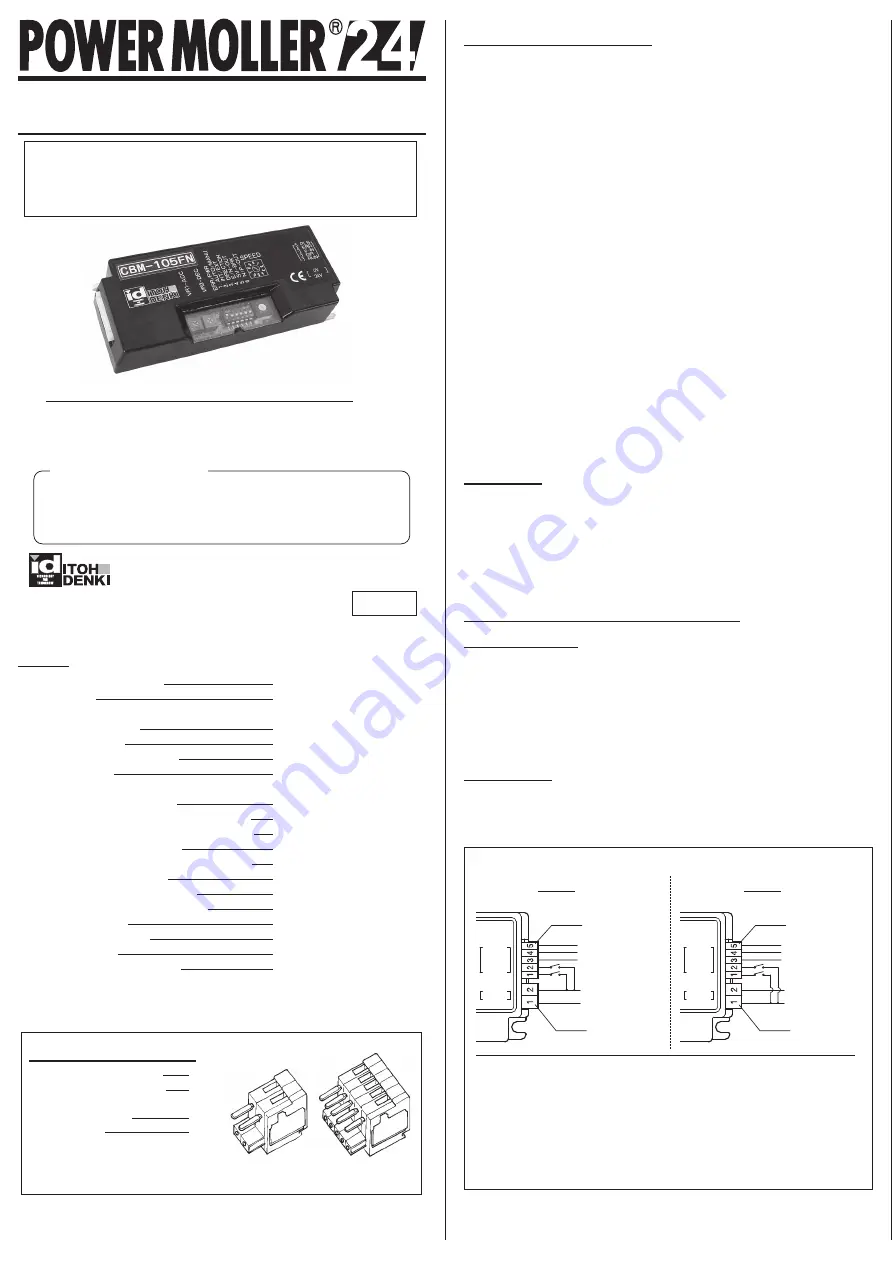
24V
1.RUN
3.V-IN
2.DIR
4.ERR
5.PLS
0V
24V
1.RUN
3.V-IN
2.DIR
4.ERR
5.PLS
0V
(
1
)
(
1
)
(
1
)
(
1
) ~ (
2
)
(
2
)
(
2
) ~ (
3
)
(
3
)
(
3
) ~ (
5
)
(
3
) ~ (
5
)
(
6
)
(
6
)
(
6
)
(
7
)
(
7
) ~ (
8
)
(
8
)
(
9
)
(
1 0
)
(
1 0
)
Safety Instructions
Power
Before Operating the Product
Mounting
Wiring
Direction Setting
Functions
Operation Instruction
Speed Variation
Internal Speed Variation
External Speed Variation
Direction Setting
Acceleration and Deceleration
Error Signal Output
Motor Plus Signal Output
Error Status, Reset, History
Servo Brake
Troubleshooting
Dimension
Product specifications
1
.
2
.
3
.
3 - 1 .
3 - 2 .
3 - 3 .
4
.
5
.
5 - 1 .
5 - 1 - 1 .
5 - 1 - 2 .
5 - 2 .
5 - 3 .
6
.
7
.
8
.
9
.
1 0
.
11
.
1 2
.
Standard Accessories
INDEX
●
Power Connector (CN1)
●
Control Connector(CN2)
●
Mounting screws and nut
Screw
:
M4×15
Nut
:
M4
×
1
×
1
×
2
×
2
Power connector
(
CN-1
)
Control connector
(
CN-2
)
(
1
)
CN1
DC24V
0V
CW/CCW
RUN/STOP
0-10V IN
Error signal output
Motor pulse signal output
Error signal output
Motor pulse signal output
CN2
CN1
DC24V
0V
CW/CCW
RUN/STOP
0-10V IN
CN2
PM486FE , PM486FP , PM486FS , PM500FE
PM500FP , PM570FE , PM605FE , PMT42FE
*
BR(Brake) and LT(Low temperature) is not available on CBM-105
Thank you for purchasing a Itoh Denki CBM-105 series motor
driver.
Please read this manual before operating the product,
and keep this manual readily accessible for reference.
●
DC24V battery
●
Switching power (24VDC 5A) or smoothed and rectified power
●
Smoothed and rectified power (
≦
10% ripple)
※
Use stable power supply with 5A or over. The power supply should not be affected
by peak current 20A for 1msec.
NPN
PNP
Switch off the power, when removing from conveyor, wiring or maintenance is done,
otherwise you have a risk of electrical shock or injury
Respect the electrical regulations of the site or equipment, where the product in installed.
(Labor safety and sanitary regulations, electrical equipment technical standard, etc)
Operate the motor driver within its intended design and specifications to avoid electrical
shock, injury or fire.
Do not disassemble, repair nor modify the product (For which we do not warrant)
It might cause electrical shock, injury or failure.
Separately set the circuitry to monitor the important input and/or output signal status,
which might cause accident, because the signal may stay ON or OFF in case of the
CBM-105 driver card failure.
Be sure to shut off the power before inserting or removing any connector. Do not wire
connector left in the CBM-105 driver card.
Do not drop, give external impact nor pressure to the CBM-105 driver card. If that
happened, do not reuse it.
Make sure all the connectors are properly engaged with cables.
Make sure the conveyor frame and control box where the CBM-105 driver card is
mounted are grounded.
Do not switch ON or OFF the relay or contractor in close proximity to power or signal line,
or the CBM-10 driver card as the generated noise could cause malfunction.
Be sure to inject power or input signal for 15msec or over to ensure the proper reaction.
Do not remove any connector during operation. It may cause of damage to the driver card
or shorten its life time.
Do not shut power off during MDR is running. It may cause of damage to the driver card or
shorten its life time.
Do not get on the conveyor if power is ON to the driver cards. Do not turn on power, if
totes are not steady on conveyor. It might cause electrical shock, injury or failure.
Do not pull by force the Power Moller to turn.
It may cause of damage to driver card or shorten its life cycle.
Without power on to the driver card, dynamic brake or servo brake is not worked.
1. Safety Instructions
3. Before Operating the Product
3-1. Mounting
3-2. Wiring
2. Power
●
●
●
●
●
●
●
●
●
●
●
●
●
●
●
●
①
Make mounting holes in the conveyor frame to fit the fixing holes in the product.
(
See Dimensions in section 11
)
※
The product’s back place should be paid to prevent the metallic dust entry to
the product.
※
Make sure the conveyor us adequately grounded.
②
Fix the product tightly to the conveyor frame with the supplied mounting screws
and nuts with the recommended fastening torque between 1.5Nm and 1.9Nm.
・
Wiring should be made while the product is not powered.
・
Switch for Run/Stop or CW/CCW is an option and is not supplied.
・
Relay contact or PLC output is available instead of the above switch.
・
Wiring to the supplied connectors should be made before inserting into the driver.
-1 MDR run and stop
(
Mandatory
)
→
See section 5
-2 MDR direction (CW/CCW)
*
→
See section 5-2
*
Turning direction setting can also be done by dip switch on the PCB.
-3 External speed variation by analog voltage change
→
See section 5-1
*
Speed variation setting also can be done by Rotary Switch on the PCB.
-4 Discharge of error signal
→
See section 6
-5 Discharge of motor pulse
→
See section 7
【
Wiring diagram
】
CN2
Brushless DC Motor Driver
【
CBM-105 FN/FP
】
User Manual
Applicable Power Moller
(
MDR
)
models:
MDR (Motor Driven Roller)
MDR is DC brushless motorized roller for conveyor.
MDR is defined by Conveyor Equipment Manufacturers
Association (CEMA) and conveyor built by MDR is well
established technology in Material Handling Industry.
No.561
ITOH DENKI CO.,LTD.