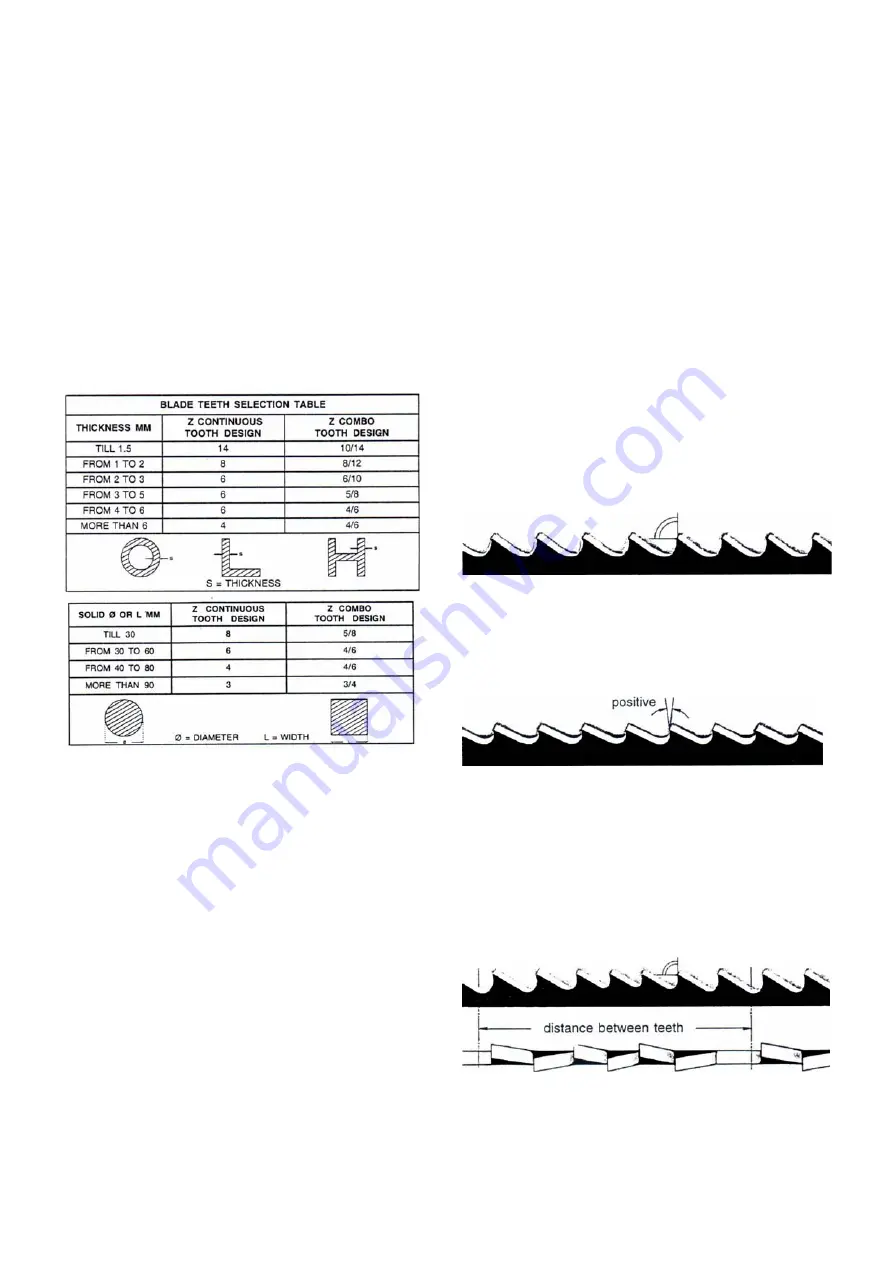
- 11 -
- Parts with a thin and/or variable section such as
profiles, pipes and plate, fine toothing is needed, so
that the number of teeth used simultaneously while
cutting is from 3 to 6;
- Parts with large transverse sections and solid
sections need widely spaced toothing to allow for the
greater volume of the shavings and better tooth
penetration;
- Parts made of soft material or plastic (light alloys,
mild bronze, Teflon, wood, etc.) also require widely
spaced toothing;
- Pieces cut in bundles require combo tooth design.
8.3 Teeth pitch
As
already
stated,
this
depends
on
the
following
factors:
-
Hardness of the material
-
Dimensions of the section
-
Wall thickness.
8.4 Cutting and advance speed
The
cutting
speed
(m/min)
and
the
advance
speed
(cm
2
/min
=area
traveled
by
the
disk
teeth
when
removing
shavings)
are limited
by
the
development
of
heat
close
to
the
tips
of
the
teeth.
- The
cutting
speed
is
subordinate
to
the
resistance
of
the
material
(R
= N/mm
2
),
to
its
hardness
(HRC)
and
to
the
dimensions
of
the
widest
section.
- Too
high
an
advance
speed
(=
lowering
of
the
saw
frame) tends
to
cause
the
disk
to
deviate
from
the
ideal
cutting
path, producing
non
rectilinear
cuts
on
bath
the
vertical
and
the horizontal
plane.
The
best
combination
of
these
two
parameters
can
be
seen directly
examining
the
chips.
Long
spiral-shaped
chips
indicate
ideal cutting.
Very
fine
or
pulverized
chips
indicate
lack of
feed
and/or
cutting
pressure
.
Thick
and/or
blue
chips
indicate
overload of
the
blade.
8.5 Blade running-in
When cutting for the first time, it is good practice
to run in the tool making a series of cuts at a low
advance speed
(=
30-35
cm
2
/min
on
material
of
average
dimensions
with
respect
to
the
cutting
capacity
and
solid
section
of
normal
steel with
R =
410-510
Nimm
2
).
Generously spraying the cutting
area with lubricating coolant.
8.6 Blade structure
Bi-metal
blades
are
the
most
commonly
used.
They
consist
of
a silicon-steel
blade
backing
by a
laser
welded high
speed
steel
(HHS)
cutting
edge.
The
type
of
stocks
are classified
in
M2,
M42,
M51
and
differ
from
each
other
because of
their
major
hardness
due
to
the
increasing
percentage
of Cobalt
(Cc)
and
molybdenum
(Mo)
contained
in
the
metal
alloy.
8.7 Blade type
They
differ
essentially
in
their
constructive
characteristics,
such as:
-
Shape
and
cutting
angle
of
tooth
-
Pitch
-
Set
Shape and angle of tooth
REGULAR TOOTH:
Oº
rake
and
constant
pitch.
Most
common
form
for
transversal
or
inclined
cutting
of
solid small
and
average
cross-sections
or
pipes,
in
laminated
mild steel
and
gray
iron
or
general
metal.
POSITIVE
RAKE
TOOTH:
9º
- 10º
positive
rake
and
constant pitch.
Particular
use
for
crosswise
or
inclined
cuts
in
solid
sections
or large
pipes,
but
above
all
harder
materials
(highly
alloyed
and stainless
steels,
special
bronze
and
forge
pig iron).
COMBO
TOOTH:
pitch
varies
between
teeth
and
consequently varying
teeth
size
and
varying
gullet
depths.
Pitch
varies
between
teeth,
which
ensures
a
smoother,
quieter
cut
and
longer blade
life
owing
to
the
lack
of
vibration.
Another
advantage
offered
in
the
use
of
this
type
of
blade
in
the fact
that
with
an
only
blade
it
is
possible
to
cut
a wide
range
of different materials
in
size
and
type.
COMBO
TOOTH:
9º
- 10º
positive
rake.