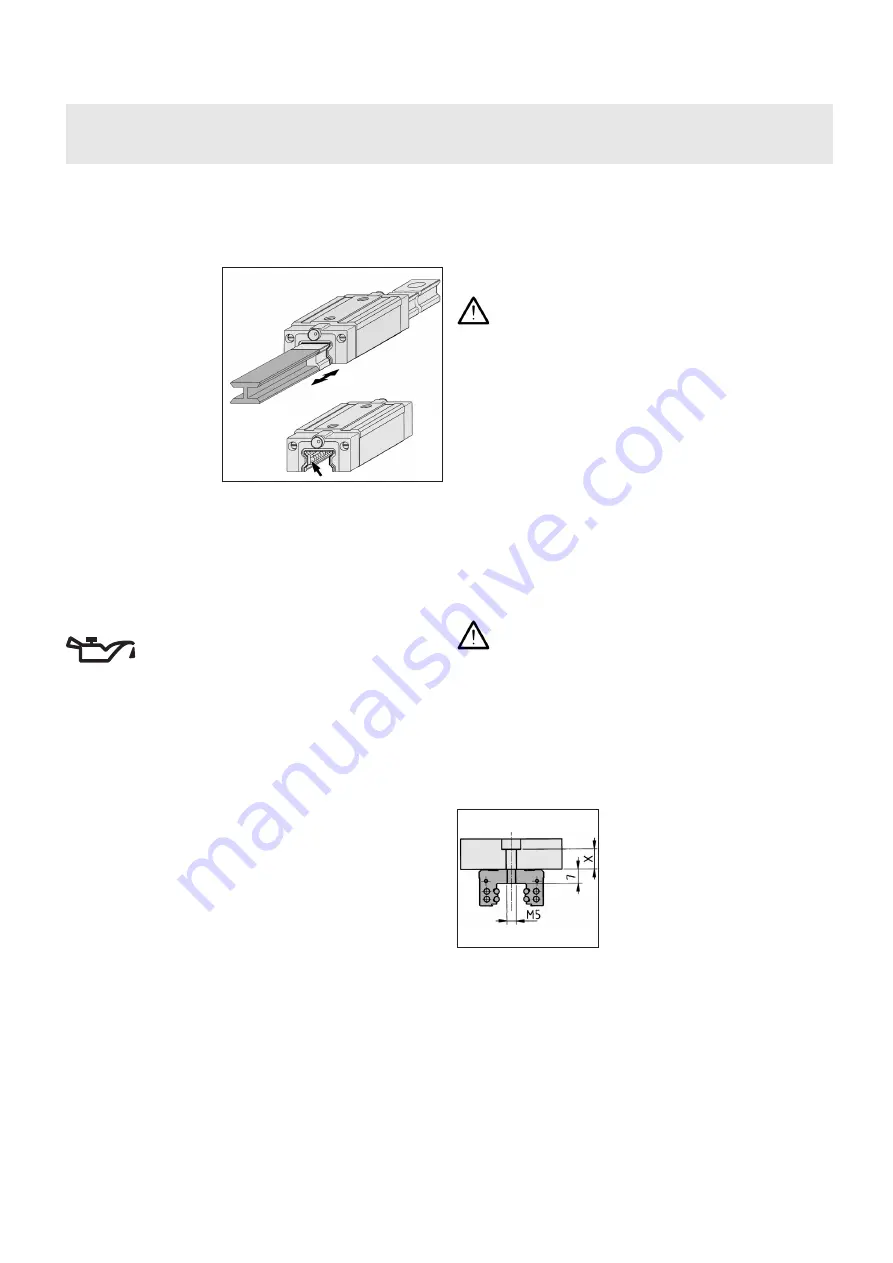
7
Setting up the Guide Carriage and Lubricating the Linear Guide System
Remove the guide carriage from its packaging. If lubrication with grease is
specified, withdraw the protective rail from the raceways and smear the ball
bearings with grease. For oil lubrication the grease should be wiped from the
ball rows carefully.
Place the carriage onto its protective rail in front of the guide rail and carefully
slide it onto the guide rail, ensuring that it is correctly aligned.
When placing the carriage onto the rail, pay particular attention to the
wipers at the head end:
they should not be dislodged from their seatings in the end caps and the lip
seals should not be allowed to fold over.
If the lip seals of the wipers have been fold over despite of careful fitting the car-
riage, it can be aligned by pushing the carriage over the ends of the guide rail.
Carefully push the carriage once along the entire length of the guide rail and
check the resistance to movement, particularly as the carriage passes over the
plastic plugs (reset them if necessary). Any perceptible friction is principally
attributable to the fact that the seals have not yet bedded in; this friction will
diminish when the flexible elements have settled and adjusted to the rail.
Make sure that the guide carriage is supplied with the specified
lubricant. Careful preparation greatly enhances the service life
of the Linear Guide System. The Linear Guide System can be
lubricated in two ways:
Oil lubrication:
Minimum oil volume 0.5 to 0.6 cm
3
Grade of oil: only EP-additive oils for mixed friction, CLP conforming to DIN 51
517 or HLP conforming to DIN 51 524
Viscosity grade: between ISO VG 32 and ISO VG 68 at an operating tempe-
rature range of 0°C to 70°C; other grades to be selected for lower or higher
temperatures.
The oil can be topped up through the funnel-type lubrication nipples.
Grease lubrication:
nitial grease capacity 0.8 to 1.0 g or at least until grease is expelled.
Type of grease: lithium-saponified greases, mineral-oil based.
The carriages are initially lubricated with grease.
The initial volume of grease should be applied by hand to the chains of ball
bearings; one stroke of the grease gun should then be applied to the grease
nipple to ensure that the lubrication channels are filled.
In the case of slide guides with two parallel guide rails, the fastening screws of
the slide should be securely attached to the guide carriage, following parallel
alignment. The loose screws of the rails should then be tightened in the
sequence indicated, by applying the specified tightening torque (refer to the
section ’Installing the Guide Rail’).
Once the guiding slides have been assembled, move the carriage again along
the entire available length of the track and, in particular, check for backlash and
consistent resistance to movement.After refilling with lubricant, the resistance
to movement may briefly increase until, after a number of strokes, the lubricant
has been evenly distributed.
A funnel-type lubrication nipple, with a 120º taper conforming to DIN 3405
(Form D), is located at each end of the carriage. However, it is only necessary
to apply lubricant to one end of the carriage, while moving it gently forward and
backward.
All types of lubrication give rise to lubricant seepage. For this reason,
you should design the connecting structure to ensure reliable collection
of the lubricant and ensure proper disposal.
Carefully place the slide structure onto the guide carriage(s) and move the
loosely-mounted slide several times along the entire length of the rail without
applying any load. Then securely assemble the components.In doing so,
carefully select the correct screw length and, in particular, note the maximum
permissible tightening torque for the screws: two M5 screws, Property Class
10.9, are supplied and these must be tightened to the permissible torque
MA = 5.8 Nm.