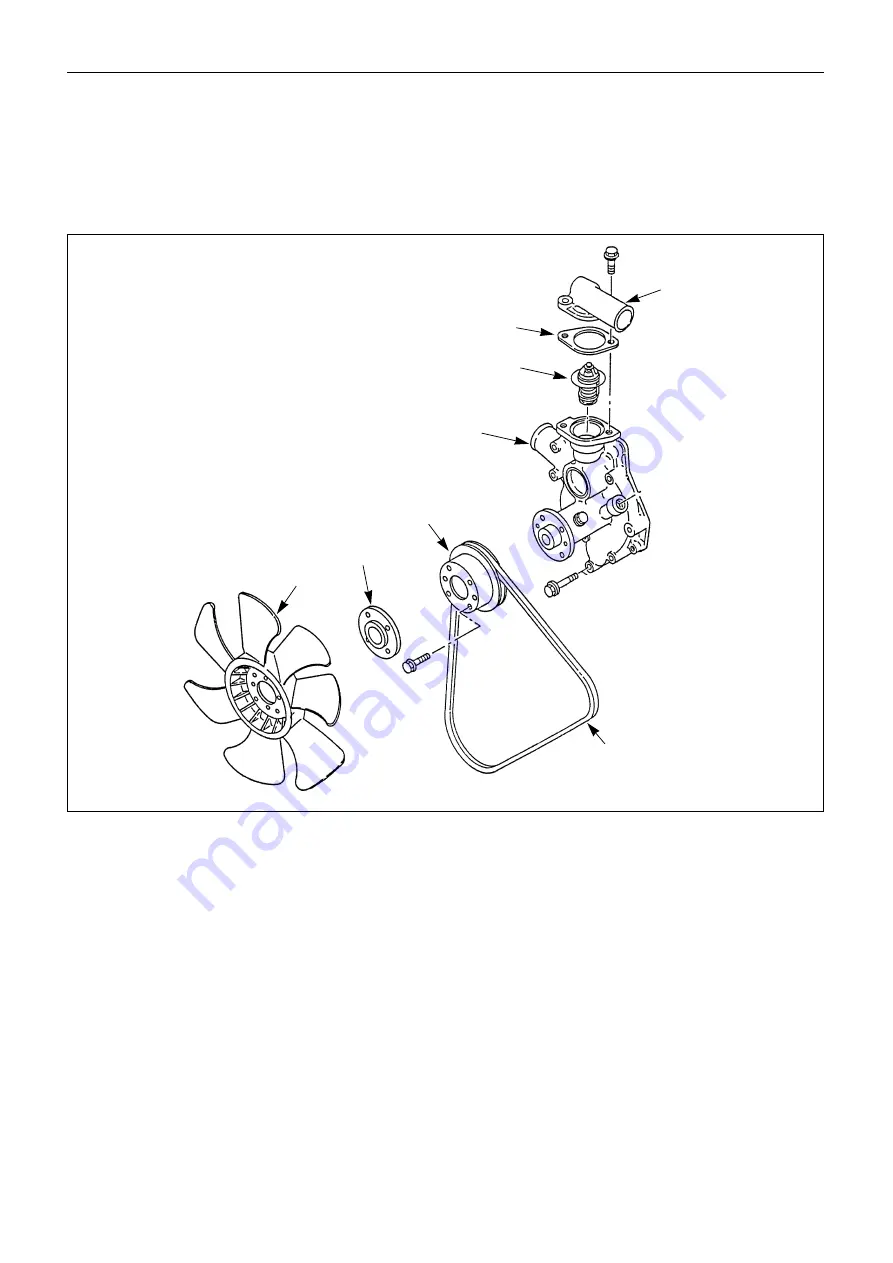
GENERAL INFORMATION
3
6. Each service operation section in this Workshop Manual begins with an exploded view of the applica-
ble area.
(Example)
Major components
Figures in parentheses “(
)” show the order of disassembling or reassembling.
7. Measurement criteria are defined by the terms “standard” and “limit”.
A measurement falling within the “standard” range indicates that the applicable part or parts are ser-
viceable.
“Limit” should be thought of as an absolute value.
A measurement which is outside the “limit” indicates that the applicable part or parts must be either
repaired or replaced.
8. Components and parts are listed in the singular form throughout the Manual.
Fig. 1
Water Outlet Pipe (5)
Packing (6)
Thermostat (7)
Water pump ASM (8)
Pulley; Fan (4)
Spacer (2)
Belt; Fan (3)
Fan; Cooling (1)
Содержание 4LE2
Страница 1: ...INDUSTRIAL DIESEL ENGINE 4LE2 MODEL 2003 ISUZU MOTORS LIMITED WORKSHOP MANUAL ...
Страница 8: ...GENERAL INFORMATION 5 APPEARANCE 1 MODEL 4LE2 1 Left side view 2 Right side view Fig 2 Fig 3 ...
Страница 16: ......
Страница 19: ...6 TURBOCHARGER N m kgf m ft lb 16 GENERAL INFORMATION Fig 16 19 28 1 9 2 9 14 21 ...
Страница 29: ...MEMO ...
Страница 36: ...ENGINE 33 Internal Parts 1 3 1 3 2 7 4 5 17 18 6 15 16 14 Fig 44 ...
Страница 37: ...34 ENGINE Internal Parts 2 3 Fig 45 Do not pull out this bolt 20 13 12 9 10 11 8 19 Rear 21 ...
Страница 38: ...ENGINE 35 14 1 14 2 15 Internal Parts 3 3 When provided with PTO Fig 46 ...
Страница 64: ...ENGINE 61 Internal Parts 1 3 Fig 119 Rear 3 14 2 13 12 11 1 10 9 ...
Страница 65: ...62 ENGINE 19 20 18 17 4 5 15 20 7 6 16 8 Internal Parts 2 3 Fig 120 ...
Страница 66: ...ENGINE 63 8 1 8 2 7 Internal Parts 3 3 Fig 121 ...
Страница 85: ...MEMO ...
Страница 91: ...MEMO ...
Страница 103: ...MEMO ...
Страница 109: ...MEMO ...
Страница 111: ...MEMO ...
Страница 121: ...PRINTED IN JAPAN IDE 2330 ...