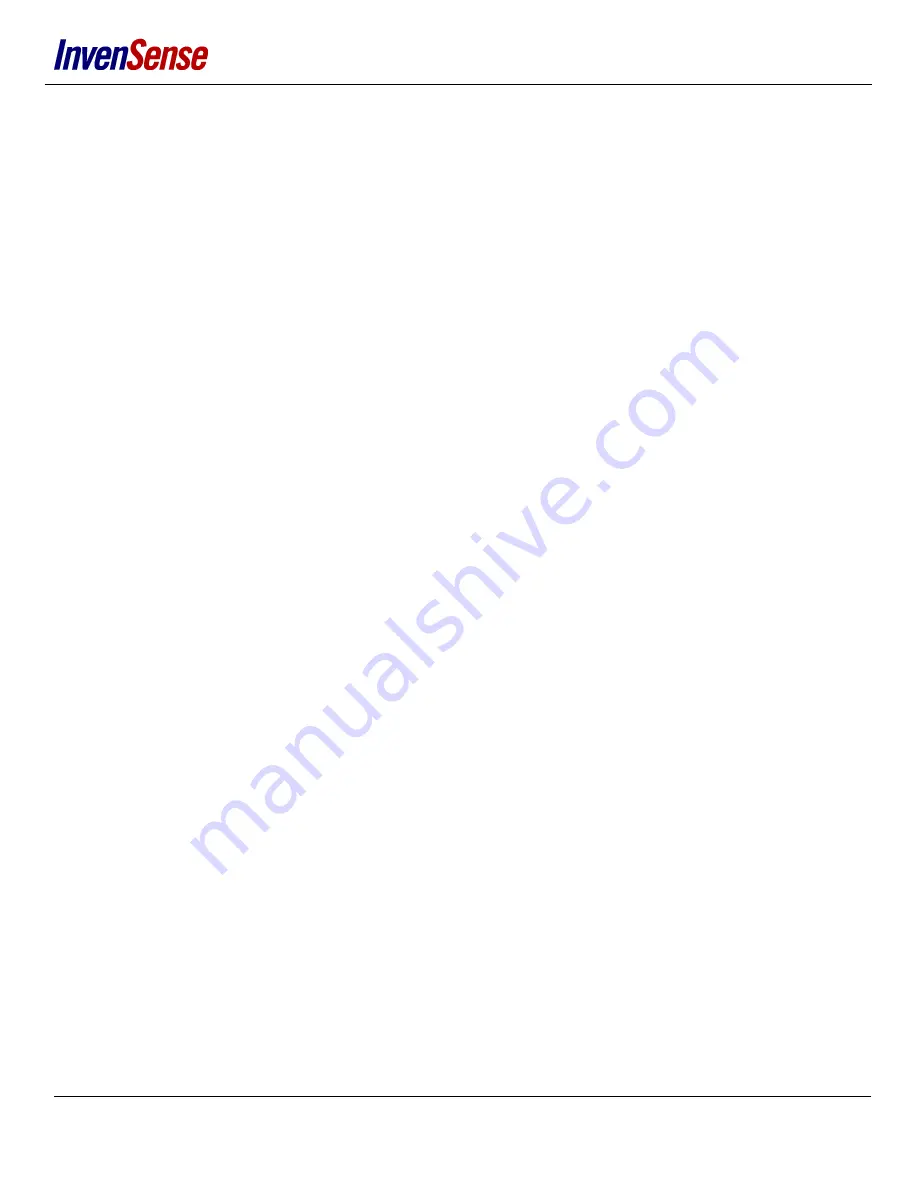
AN-MPU-x000A-01
InvenSense reserves the right to change the detail
specifications as may be required to permit improvements
in the design of its products.
InvenSense Inc.
1745 Technology Drive, San Jose, CA 95110 U.S.A
+1(408) 988–7339
www.invensense.com
Document Number: AN-MPU-x000A-01
Revision: 1.1
Date: 06/12/2015
PCB Design Guidelines for InvenSense
MotionTracking™ Devices