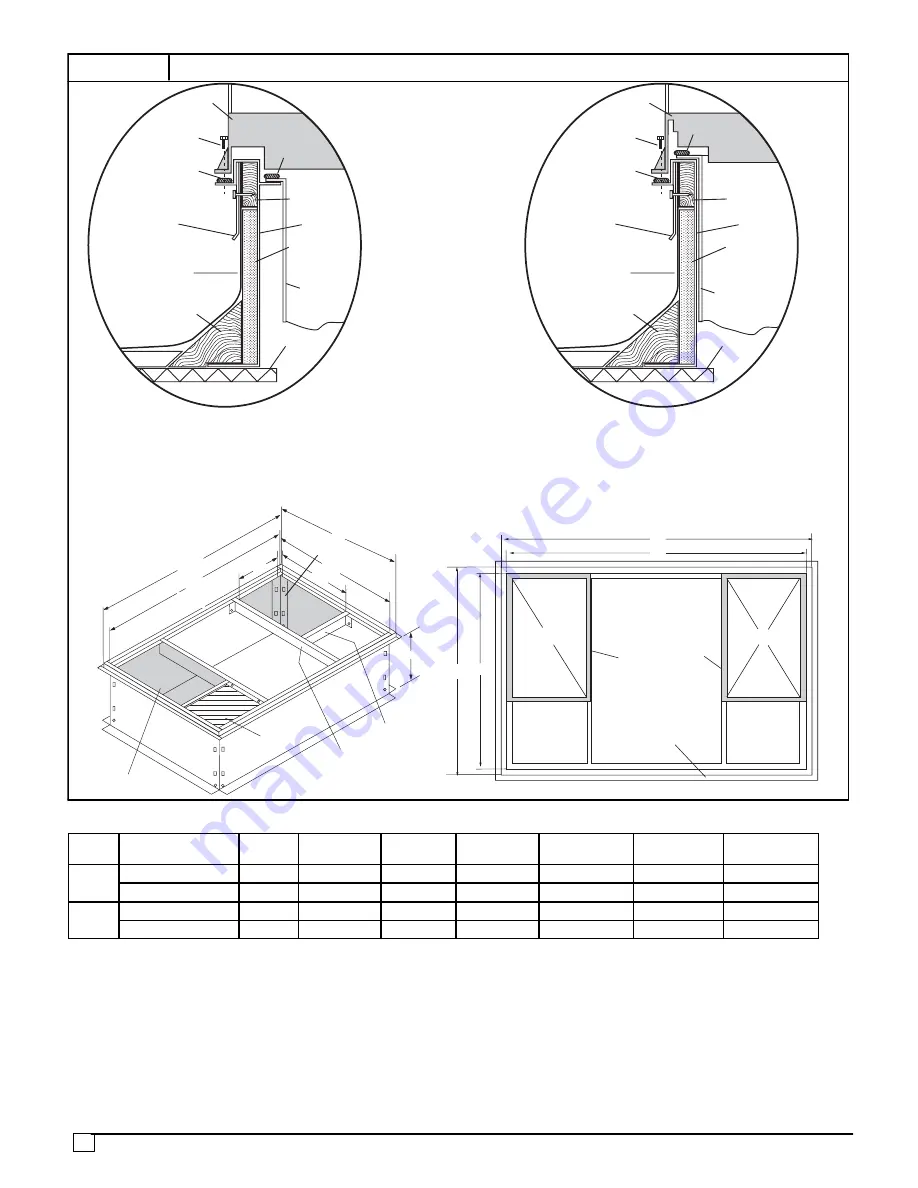
8
Gask et around
outer edge
Insulated
deck
pan
Gask et around
duct
S/A
R/A
HVAC
unit
base
*Gask eting
outer flange
Flashing field
supplied
Roofing material
field supplied
Cant str ip
field supplied
*Provided with roofcurb
Roof
Duct wo rk
field supplied
Insulation (field
supplied)
Roofcurb*
Wood nailer*
Gask eting
inner flange*
Scre w
(NO TE A)
Roof Curb for Small Cabinet
Note A: When unit mounting scre w is used
,
retainer bra cke t must also be used.
HVAC unit
base
*Gask eting
outer flange
Flashing field
supplied
Roofing material
field supplied
Cant str ip
field supplied
*Provided with roofcurb
Roof
Duct wo rk
field supplied
Insulation (field
supplied)
Roofcurb*
Wood nailer*
Gask eting
inner flange*
Scre w
(NOTE A)
Roof Curb for
Large Cabinet
Note A: When unit mounting scre w is used
,
retainer bra cket
must also be used.
A
B Typ.
Supply opening
(B x C)
Long
Support
D
F
Return opening
(B X C)
Insulated
deck pan
Short
Support
C Typ.
G
E
F
G
D
E
FIGURE 5
Roof Curb Dimensiona
F
Model
PHN5
MODEL NUMBER
A
IN. [MM]
B
IN. [MM]
C
IN. [MM]
D
IN. [MM]
E
IN. [MM]
F
IN. [MM]
G
IN. [MM]
24
NPRFCURB006A00
8 [203]
11 [279]
16--1/2 [419]
28--3/4 [730]
30--3/8 [771]
44--5/16 [1126]
45--15/16 [1167]
NPRFCURB007A00
14 [356]
11 [279]
16--1/2 [419]
28--3/4 [730]
30--3/8 [771]
44--5/16 [1126]
45--15/16 [1167]
36--60
NPRFCURB008A00
8 [203]
16--3/16 [411]
17--3/8 [441] 40--1/4 [1022]
41--15/16 [1065]
44--7/16 [1129]
46--1/16 [1169]
NPRFCURB009A00
14 [356]
16--3/16 [411]
17--3/8 [441] 40--1/4 [1022]
41--15/16 [1065]
44--7/16 [1129]
46--1/16 [1169]
Notes:
1.
Roof curb must be set up for unit being installed.
2.
Seal strip must be applied as required to unit being installed.
3.
Roof curb is made of 16 gauge steel.
4.
Attach ductwork to curb (flanges of duct rest on curb).
5.
Insulated panels: 1---in. (25.4mm) thick fiberglass 1 lb. density.
6.
When unit mounting screw is used (see Note A), a retainer bracket must be used as well. This bracket must also be used when required by
code for hurricane or seismic conditions. This bracket is available through Micrometl.
Содержание PHN524
Страница 5: ...5 FIGURE 3 PHN524 DIMENSIONS ...
Страница 6: ...6 FIGURE 4 PHN536 60 DIMENSIONS ...
Страница 13: ...13 FIGURE 12 PHN524 60 208 230 1 60 Wiring Diagram ...