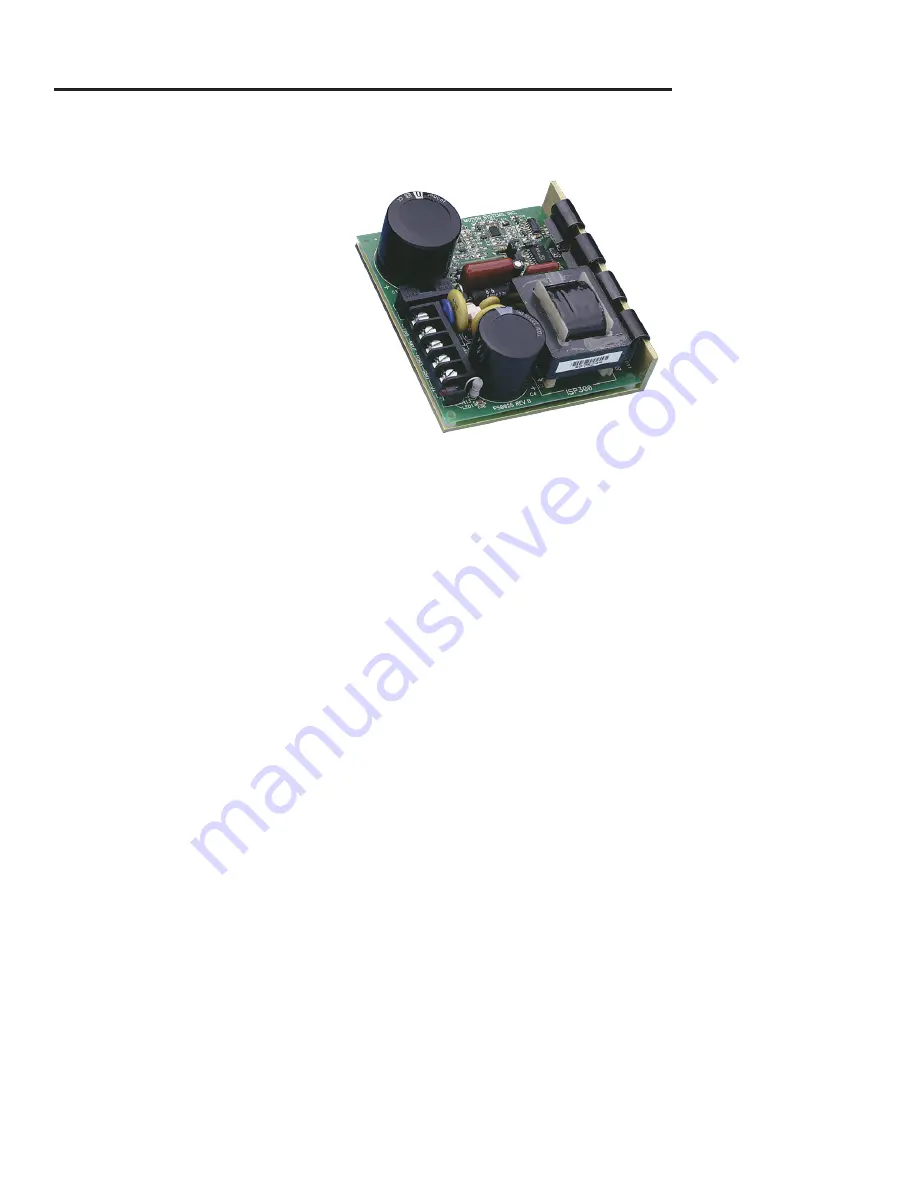
7
Part 2: Interfacing and Configuring
SECTION 2.2
Interfacing DC Power
Choosing a Power Supply for Your MForce PowerDrive
When choosing a power supply for your
MForce PowerDrive there are performance
and sizing issues that must be addressed. An
undersized power supply can lead to poor
performance and even possible damage to
the device, which can be both time consum-
ing and expensive. However, The design of
the MForce PowerDrive is quite efficient
and may not require as large a supply as you
might suspect.
Motors have windings that are electrically
just inductors, and with inductors comes re-
sistance and inductance. Winding resistance
and inductance result in a L/R time constant
that resists the change in current. It requires
five time constants to reach nominal current.
To effectively manipulate the di/dt or the rate
of charge, the voltage applied is increased.
When traveling at high speeds there is less
time between steps to reach current. The point where the rate of commutation does not allow the driver to reach
full current is referred to as Voltage Mode. Ideally you want to be in Current Mode, which is when the drive
is achieving the desired current between steps. Simply stated, a higher voltage will decrease the time it takes to
charge the coil, and therefore will allow for higher torque at higher speeds.
Another characteristic of all motors is Back EMF, and though nothing can be done about back EMF, we can give
a path of low impedance by supplying enough output capacitance. Back EMF is a source of current that can push
the output of a power supply beyond the maximum operating voltage of the driver and as a result could damage
the MForce PowerDrive over time.
The MForce PowerDrive is very current efficient as far as the power supply is concerned. Once the motor has
charged one or both windings of the motor, all the power supply has to do is replace losses in the system. The
charged winding acts as an energy storage in that the current will re-circulate within the bridge, and in and out of
each phase reservoir. While one phase is in the decaying stage of the variable chopping oscillator, the other phase
is in the charging stage, this results in a less than expected current draw on the supply.
The MForce PowerDrive is designed with the intention that a user’s power supply output will ramp up to greater
or equal to the minimum operating voltage. The initial current surge is quite substantial and could damage the
driver if the supply is undersized. If a power supply is undersized, upon a current surge the supply could fall be-
low the operating range of the driver. This could cause the power supply to start oscillating in and out of the volt-
age range of the driver and result in damaging either the supply, driver or both. There are two types of supplies
commonly used, regulated and unregulated, both of which can be switching or linear. All have their advantages
and disadvantages.
An unregulated linear supply is less expensive and more resilient to current surges, however, voltage decreases
with increasing current draw. This can cause serious problems if the voltage drops below the working range of the
drive. Also of concern is the fluctuations in line voltage. This can cause the unregulated linear supply to be above
or below the anticipated voltage.
A regulated supply maintains a stable output voltage, which is good for high speed performance. They are also
not bothered by line fluctuations, however, they are more expensive. Depending on the current regulation, a
regulated supply may crowbar or current clamp and lead to an oscillation that as previously stated can lead to
damage. Back EMF can cause problems for regulated supplies as well. The current regeneration may be too large
for the regulated supply to absorb and may lead to an over voltage condition.
Switching supplies are typically regulated and require little real-estate, which makes them attractive. However,
their output response time is slow, making them ineffective for inductive loads. IMS has designed a series of low
cost miniature non-regulated switchers that can handle the extreme varying load conditions which makes them
ideal for the MForce PowerDrive.
Figure 2.2.1: IMS ISP300 Switch Mode Power Supply
Содержание MForce PowerDrive Plus MForce Series Microstepping PowerDrive
Страница 1: ...Operating Instructions TM Excellence in Motion TM FORCE POWER DRIVE MICROSTEPPING...
Страница 10: ...1 4 Microstepping MForce PowerDrive Manual Revision R040507 Page Intentionally Left Blank...
Страница 18: ...1 12 Microstepping MForce PowerDrive Manual Revision R040507 Page Intentionally Left Blank...
Страница 20: ...Microstepping MForce PowerDrive Manual Revision R040507 Page Intentionally Left Blank...
Страница 24: ...Microstepping MForce PowerDrive Manual Revision R040507 Page Intentionally Left Blank...
Страница 36: ...18 Microstepping MForce PowerDrive Manual Revision R040507...
Страница 60: ...A 2 Microstepping MForce PowerDrive Manual Revision R040507 Page Intentionally Left Blank...