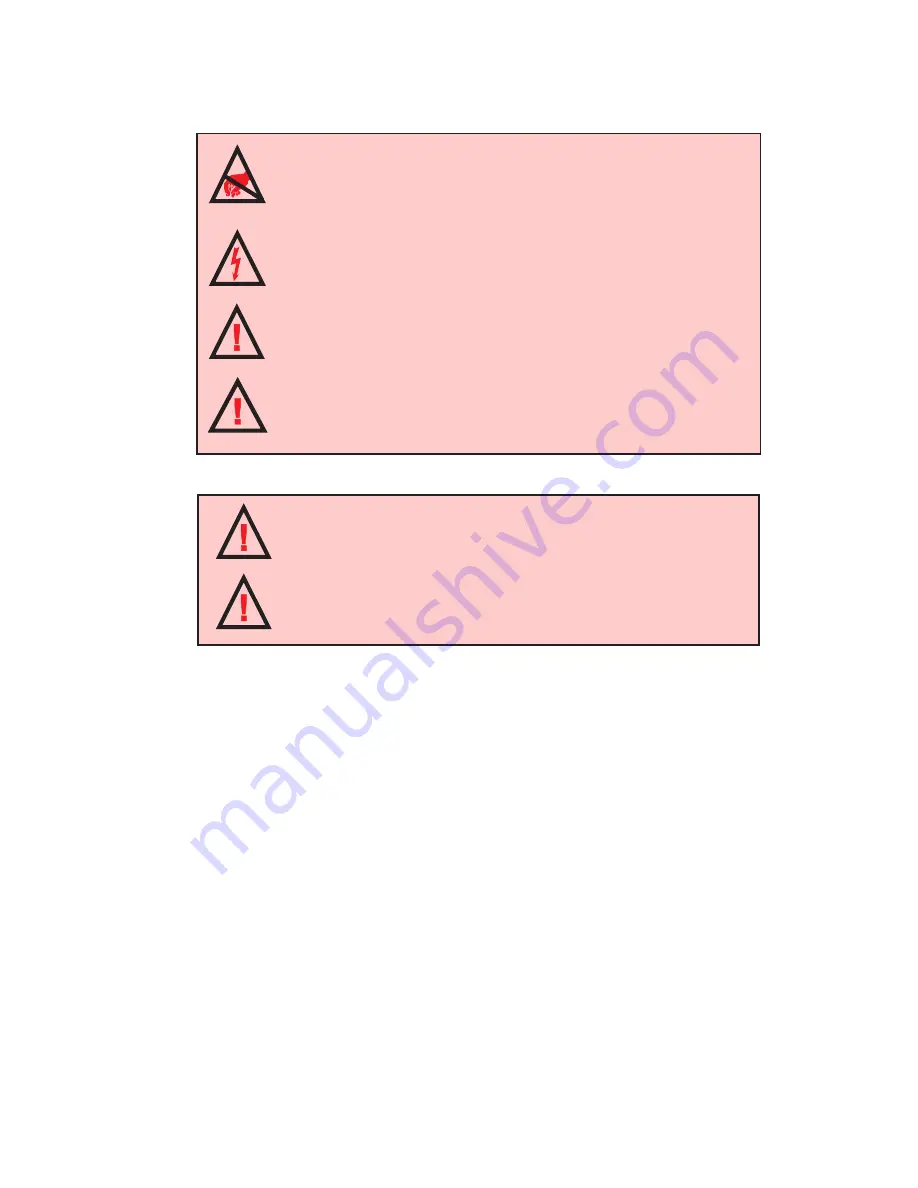
6
IM805 Operating Instructions Revision R032306
7
IM805 Operating Instructions Revision R032306
WARNING! The IM805 components are sensitive to ElectroStatic
Discharge (ESD). All handling should be done at an ESD protected
workstation.
WARNING! Hazardous voltage levels may be present if using an
open frame power supply to power the IM805.
WARNING! Ensure that the power supply output voltage does not
exceed the maximum input voltage of the IM805.
WARNING! A current adjustment resistor is always necessary to
keep the Driver and/or Motor in a safe operating range.
DO NOT operate the IM805 Driver without a current adjustment
resistor in place.
N o t e s a n d W a r n i n g s
WARNING! Turn off the AC power side to power down the DC
power supply.
WARNING! For battery operated systems connect a “transient
suppressor” across the power switch to prevent arcs and high
voltage spikes. Also place a “transorb” across the +V and GND of
the battery connections at the Driver.