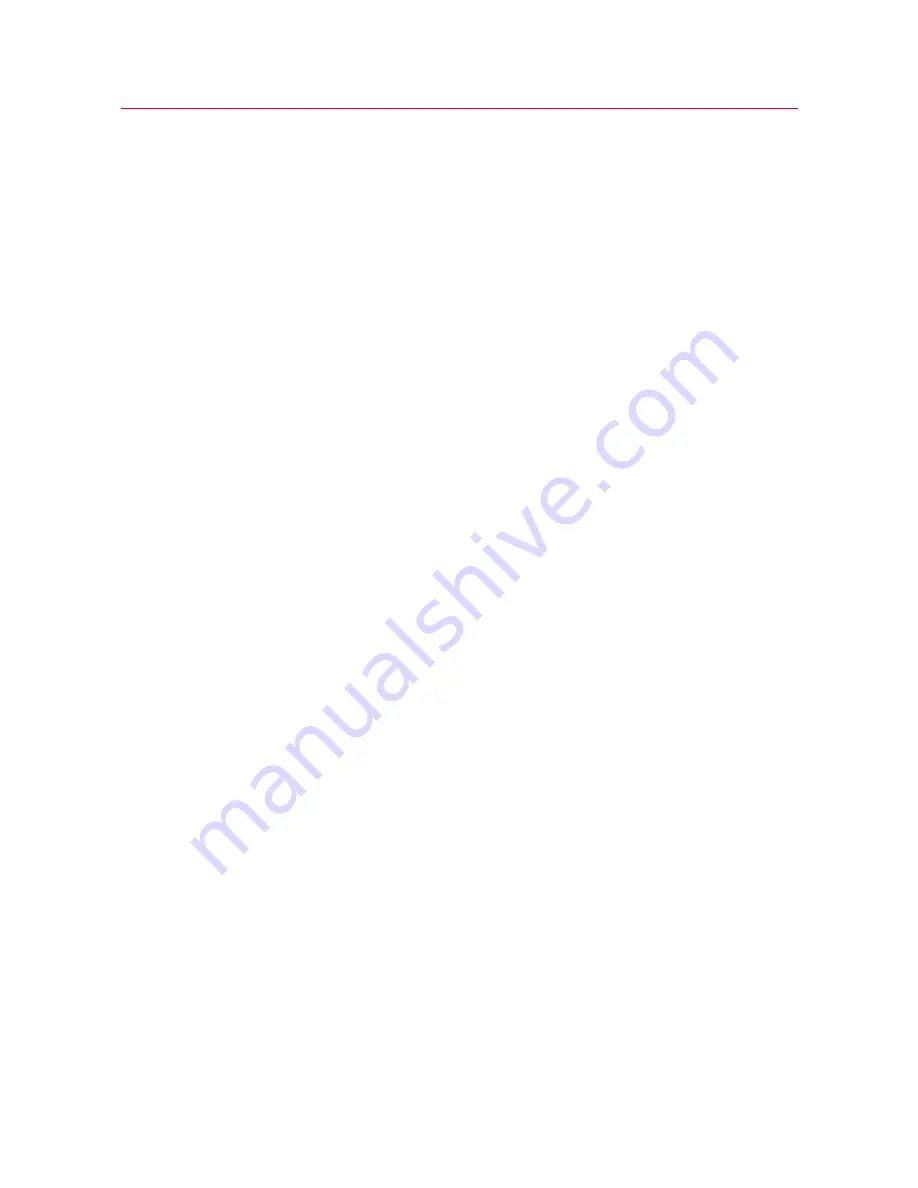
47
Troubleshooting
Product Support:
High Energy Breaks
In some circumstances, breaks that produce high energy release can cause the
extensometer to go into idle mode. The system detects this and re-initializes the
extensometer. A message displays in the software to inform you that the extensometer is
re-initializing.
Specimens that can damage the extensometer
Some specimens undergo extensive elongation before break and then exhibit a
“whipping” motion when they break. These types of breaks can damage the measuring
arms.
Arms resist being moved manually
You should only need a very light touch on the extensometer arms to move them gently
and smoothly along the entire range of travel.
If you encounter any resistance while manually moving the arms, this may indicate an
internal misalignment. Contact Instron Service for assistance.
Содержание AutoX
Страница 10: ...Chapter Introduction 10 M16 16654 EN Figure 1 Overview of the AutoX Automatic Contacting Extensometer...
Страница 30: ...Chapter Installation 30 M16 16654 EN...
Страница 42: ...Chapter Preparing to Test 42 M16 16654 EN...
Страница 48: ...Chapter Testing 48 M16 16654 EN...
Страница 54: ...Chapter Maintenance and Parts 54 M16 16654 EN...
Страница 58: ...W 58 M16 16654 EN...
Страница 59: ......
Страница 60: ...Product Support www instron com...