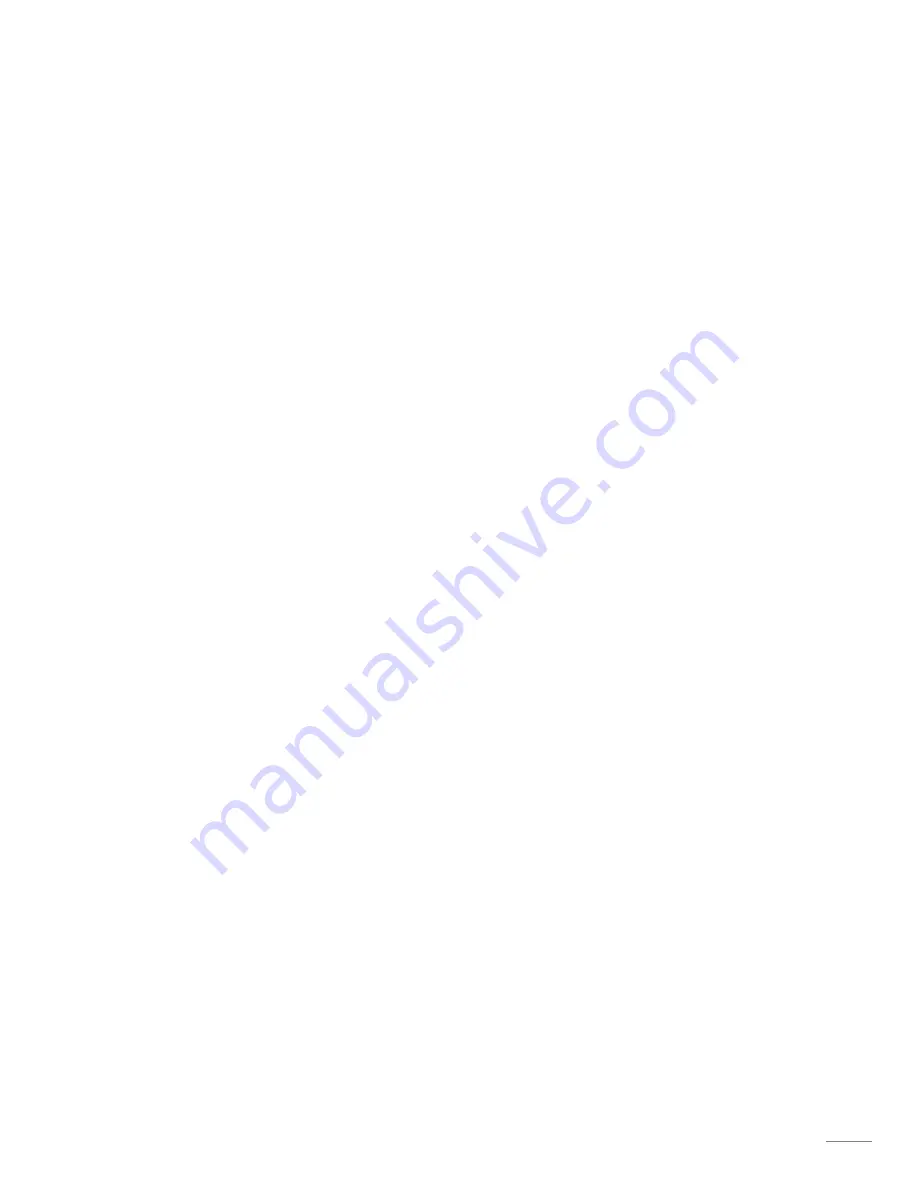
20
iii.
Fine-tuning initial value of servo
There might be some positioning errors in each servo that are possibly caused by installation
or mechanical errors. Therefore, before assembling and installing, it is necessary to perform a
two-step adjustment so as to allow the follow-up operations to be positioned correctly.
A.
Structure fine-tuning:
Prior to the final step of installation, the disks of all servos are not yet fixed to the
structure. You may unscrew the central black screw and adjust position of the disk
now.
Connect all servos to the Servo Module and connect to the power supply. Referring to
servo calibration procedures, let all servos move to their center point respectively.
Check if all screw holes align with holes on the disk. If not, unscrew the central screw
and pull up the disk, align disk holes to holes on the structure and lower the disk.
※
Both the PC and aluminum are flexible to a certain extent. In case hole positions on the PC board
misalign with the hole positions of servos, just slightly pull PC board up and adjust the disk, by lifting
it up, to a desired angle and replace it.
Align holes of all 12 servos one by one, and then proceed with final fixing of the
installation.
B.
Software fine-tuning:
After completing structure fine-tuning and fixing disks (the final step of installation),
proceed with software fine-tune program.
Enter fine-tune value of each servo respectively and adjust all motors to their desired
positions. In case satisfactory result cannot be achieved within the limit range
(127~-128), go back to structure fine-tune and readjust the structure.
※
Make sure all disk screws are tightened and all servos are within the tolerance range while
performing software fine-tuning.