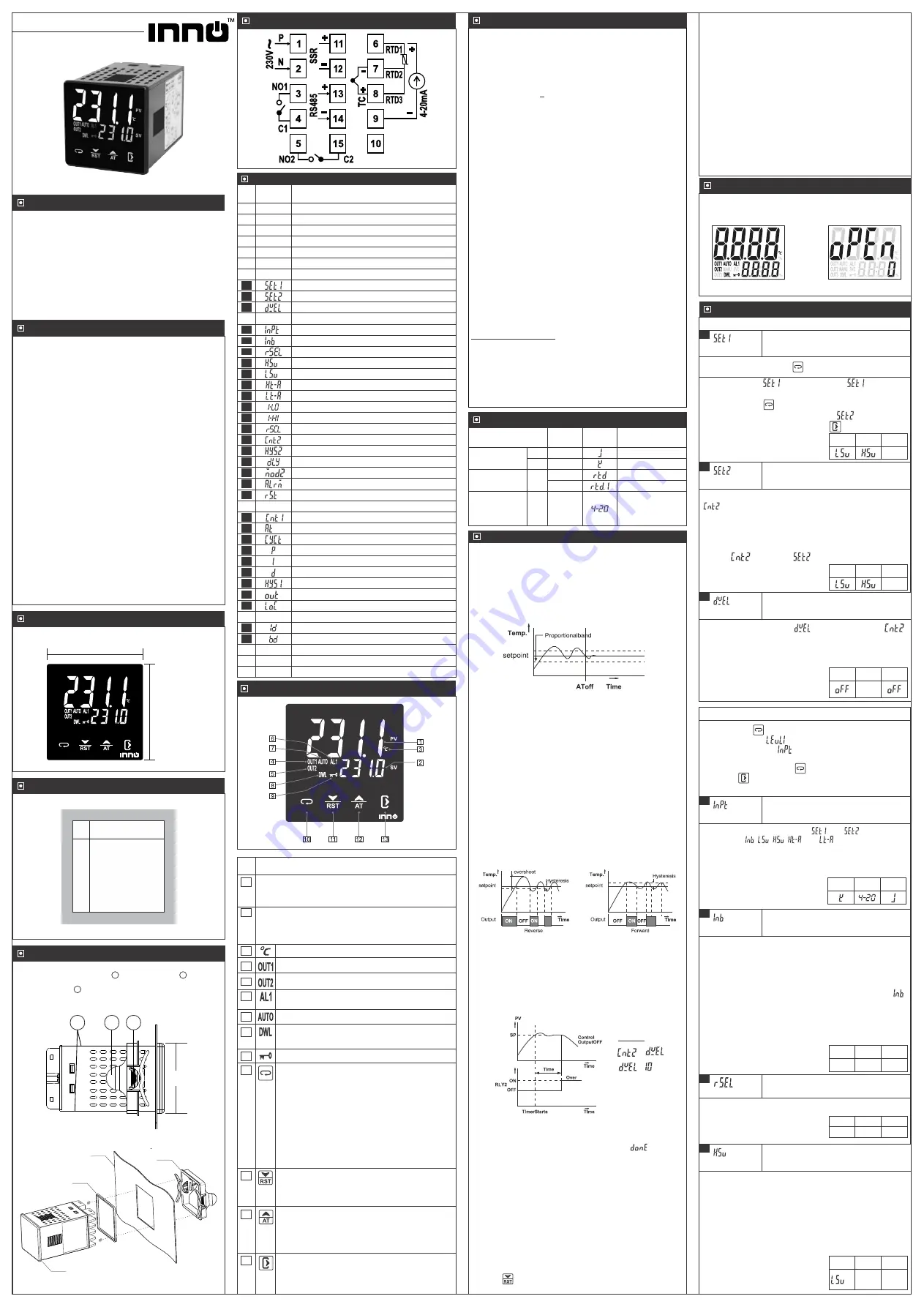
Technical Specification
7 Iconic LEDs for Indication
Control output : (For TCW-S2-UAMR2-230AC)
Thermocouple : 0.3% of F.S
Sampling Period :
1 second
Relay :
5A, 230V AC (Res.) or
Data storage :
Non-volatile flash memory
Storage temp :
-25°C to 60°C (non-condensing)
O
Display Accuracy:
RTD : 0.1% of F.S +/- 1 C
(20 min of settling time for TC)
Serial Communication:
Interface Standard :
RS485
Transmission Mode :
Half Duplex
Parity :
None/Odd/Even
SSR (field selectable) : 10V DC, 30mA
Thermocouple : J, K
Analog: 4-20 mA.
Communication Address :
1 to 255, max of 32 units per line.
Transmission Protocol :
Modbus RTU
Stop Bit :
1 or 2
Transmission Speed :
2400/4800/9600/19200/38400
Operating temp. :
0°C to 60°C (non-condensing)
Input Type :
RTD : Pt100
O
1 C for Thermocouple (J, K) input
85 to 265Vac
Analog : 0.3% of F.S
Operating humidity :
20% to 85% (non-condensing)
O
O
Resolution :
0.1 C / 1 C for RTD (Pt100) input
Power input :
230 Vac ±15 % , 50/60Hz Standard.
4 X 8mm 7 segment Green display
Auxiliary output : Relay :
5A, 230V AC (Res.)
O
O
O
O
1 C/0.1 C/0.01 C/ 0.001 C for Analog Input
Mounting :
Flush panel mounting with fasteners.
Protection :
IP65 Front
Connections :
Terminal connectors.
<
2.5sq mm terminal only.
Display :
4 X 17mm 7 segment Red/White display,
Housing :
Polycarbonate Plastic
Dimensions :
Frontal : 48 X 48mm, Depth : 78mm
Panel Cutout :
45.5 X 45.5mm
Input types & Input range
Input Type
Thermocouple
J
K
1
Decimal
Point
1
Display
Input Range
O
-50 to 750 C
O
-50 to 1200 C
RTD
Analog Input
Pt
100
1
0.1
1/0.1/0.01/
0.001
O
-99 to 400 C
O
-99.9 to 400.0 C
-1999 to 9999
(as per rSEL
decimal point
selected)
4-20
Note:
4) When soak in progress & dwell time is modified, new dwell
time is applicable .
6) Once the timer output was energized it can be reset with
2) DWL icon LED blinking indicates that dwell timer is in
progress. It switches to continuous ‘ON’ when dwell
timer is over.
3) If Dwell time programmed as OFF, it will disable the dwell
timer.
1) Countdown timer is displayed on the lower display. Once
total time elapsed lower display will show " ".
5) The dwell period can be reduced or increased when the
timer is running. if it is reduced to meet the time elapsed.
the timer will change to the end state.
the Reset key.
A dwell timer is used to control a process at a fixed temperature
for a defined period. Once the process reaches the setpoint,
dwell timer starts to count until time out . After the time
completes, control output goes OFF and auxiliary output
energises as an alarm.
3. Dwell Timer:
Settings
=
= min
10min
After Auto-tuning is complete the
"AUTO"
led will turn OFF.
While Auto-tune is in progress
"AUTO"
led will turn ON.
The Auto-tuning function automatically computes and sets the
proportional band (P), Integral time (I), Derivative time (D) as
per process characteristics.
Carry out the auto-tuning again, if there is a change in setpoint
or process parameters.
If auto -tuning is not complete after 3-4 cycles, it is suspected to
fail. In this case, check the wiring & parameters such as the
control action, input type etc.
PID-time proportional
with auto reset & rate
Working
2. ON/OFF control action (For reverse mode)
The relay is ‘ON’ up to the set temperature and cuts”OFF”
above the set temperature . As the temperature of the system
drops ,the relay is switched ‘ON’ at a temperature lower than
the set point .
HYSTERESIS:
The difference between the temperature at which relay
switches ‘OFF’ is the hysteresis or dead band.
1. Auto tuning
Note : In Auto Tuning running time, user can not change
the parameter value.
SETTING mode : Displays set value of parameter.
RUN mode : Displays set value.
Set value (SV)
Displays countdown time when Dwell timer is running.
4. RS 485 COMMUNICATION:
3 sec, software version will flash for 3 sec and then enter in to
RUN mode.
When power is On, entire display part will flash for
Initial Display when Power is ON
1. Entire display Part
2. Run Mode
Parameter Setting Mode
Function: To set control1 set point.
1
Parameter
SET MODE
Note:
If set to OFF, will not be shown in the SET
MODE.
This parameter is prompted only if Relay 2 is configured in
2. As deviation auxiliary control or as a deviation alarm mode.
,
1. As absolute auxiliary control or as an alarm (High/Low)
mode.
Function: To set control2 set point.
2
Parameter
Min
Max Fac.
O
0 C
Press & hold key for 2 second.
Display will show . User can change value using
UP/ DOWN keys. Holding the key, will change the value at a
faster rate. Press key to store the desired value & move
on to the next parameter.( For 2 relays / Dwell). Set
value also can be stored by pressing Key
Min
Max Fac.
O
0 C
Function: Sets the dwell time.
3
Parameter
Min
Max Fac.
9999
min
For dwell timer operation please refer Working section.
It is used to control process at a fixed temp. for defined period.
This parameter prompted if function is selected in .
Function: Sets input correction.
5
Parameter
Min
Max
Fac.
In time it may be possible that the display may be offset by a
degree or so.
To compensate for this error, user may need to add or minus
the degrees required to achieve the correct temperature.
O
Example :
The temperature on the display is 28 C, whereas
O
the actual temperature is 30 C. User will have to set the " "
O
parameter to 2 C, which means that once out of the
O
programming mode, the temperature on display will be 30 C
O
O
(28 C+ 2 C).
Note:
For 4-20 Input, as per rSEL decimal point will be
selected.
O
-20 C
O
20 C
O
0 C
LEVEL1 Parameter
Press the key to save the set value and to come out of
parameter setting after changing the set value.
Press & hold key for 4 seconds to enter into Level1
parameter setting( will flash).
When release the key, will flash.
Press
UP/DOWN
keys to modify the set value and to go to the
next parameter by pressing key.
Function: Sets the type of input sensor .
4
Parameter
For type of input sensor & range please refer
"Input types
& Input range"
table.
While changing the sensor type and , parameter
of level 1 ie, , , , and will reset
accordingly.
Function: To set resolution for Analog
Input.
6
Parameter
Min
Max
Fac.
This parameter is prompted when input is selected as 4-20.
1
1
0.001
Function: Sets the upper limit of PV input.
7
Parameter
Once set at a particular value, this will not allow the set
point to go above this value.
When changing the setting value and SV > HSV, SV is reset
as HSV.
Min
Max
Fac.
O
750 C
For J type sensor
Sets the maximum limit for set point adjustment. It can be
set from LSV+1 value to maximum specified range of
selected sensor.
O
750 C
+1
Min
Max
Fac.
Ÿ
User can read/write any parameter value in memory
resistor map.
Ÿ
If communication is not working then check related
hardware.
Ÿ
If baud rate and slave Id does not match communication
will not take place.
Note:
2. Open the Communication software like ModbusMat
/Modpoll or any custom software.
5. Once communication is established all present values of
TCW-S2 will be displayed.
1.
Connect the TCW-S2 to PC/Laptop with the help of
suitable Converter (RS-485 to USB).
3. Do following configuration - COM Port , Baud rate, Device Id
at both side.
4. Select Register Address of required parameters as per
register map and start communication.
Caution for your safety
Maintenance:
Cleaning: Clean the surface of the controller with a
soft moist cloth. Do not use abrasive detergents, petrol, alcohol or
solvents.
Probe :
To give a correct reading, the probe must be installed
in a place protected from thermal influences, which may
affect the temperature to be controlled.
Notice:
The information in this document is
subject
to change in
order to improve reliability , design or function without prior notice
and does not represent
a commitment on the part of the company.
In no
event will the company be liable for direct, indirect, special,
incidental or consequential damage arising out of the use or
inability to use the product or documentation, even if advised of
the possibility of such damages. No part of this manual may be
reproduced or transmitted in any form or by any means without
the prior written permission of the company.
Controller
:Controller should be installed in a place
protected by vibration, water and corrosive gasses and
where ambient temperature does not exceed the values
specified in the technical data.
WIRING:
The probe and its corresponding wires should
never be
installed in a conduit next to control or power
supply lines. The
electrical wiring should be done as shown in the diagram. The
power supply circuit should be connected to a protection switch.
The terminals admit wires of upto 2.5sq mm.
WARNING:
Improper wiring may cause irreparable damage and
personal injury. Kindly ensure that wiring is done by qualified
personnel only.
Product Mounting
Installation :
Fixing and dimensions of panel models:
To fix the unit, slide the fastener 1 through the guides 2 as per the
position shown in the figure. Move the fastener in the direction of the
arrow, pressing tab 3 it permits to move the fastener in the opposite
direction of the arrow.
45.5mm
45.5mm
Panel Cutout
Dimensions
48mm
48mm
PV
SV
TCW-S2
Operating Manual
TCW-S2-UAMR2
Introduction
A proportional–integral–derivative controller (PID controller or three
term controller) is a control loop feedback mechanism widely used in
industrial control systems and a variety of other applications requiring
continuously modulated control. A PID controller continuously
calculates an error value as the difference between a desired
setpoint (SV) and a measured process variable (PV) and applies a
correction based on proportional, integral, and derivative terms
(denoted P, I, and D respectively) which give the controller its name.
PT244-TX is a two set point PID controller. It is available in touch with
RS-485 communication. Customized iconic display interprets status
easily.
CONTROLLER
GASKET
PANEL
Side Lock
48mm
1
2
3
User Interface
Connection Diagram ( for TCW-S2-UAMR2)
Sr.
No. Description
RUN mode : Displays current measured value.
SETTING mode : Displays parameter.
Process Value (PV)
Turns ON while control output1 is ON.
4
2
1
Displays the Temperature unit.
3
8
Turns ON while control output2 is ON.
Turns ON when auto tuning is in progress.
5
7
Flashes during Dwell timer is in progress.
Continuous ON : Dwell time elapsed.
ON.
Turns ON when the corresponding alarm out turns
6
9
Turns ON when keypad is locked.
10
Used to enters parameters level, moves to next
Next key :
parameters.
in Level1 Parameters.
in Level2 Parameters.
Press & hold this key atleast 8 seconds to enter
in Level3 Parameters.
Press & hold this key atleast 2 seconds to enter
in set mode.
Press & hold this key atleast 4 seconds to enter
Press & hold this key atleast 6 seconds to enter
11
Used to reset the Dwell timer..
value.
Down / Reset Key :
Used in Program mode to decrement parameter
13
Press this key for 2 seconds to start or stop auto-
tuning.
value.
Up / AT Key :
Used in Program mode to increment parameter
12
the programing mode.
Press this key to save the setting value and to exit
Exit Key :
1
3
4
5
6
7
9
10
14
11
Control1 set point.
Sets the type of input sensor .
Sets input correction.
Sets the upper limit of PV input.
To set resolution for Analog Input.
Sets control action for relay2.
Input value scaling point 1.
Sets the hysteresis2.
Sets the dwell time.
15
Level1 Parameter
2
Control2 set point.
8
Sets the lower limit of PV input.
Sets the alarm type.
Sets AL1 icon as alarm relay.
17
18
19
Factory reset parameter.
Index
Sr.
No.
Para.
Description
User Interface
Technical Specification
Initial display when Power is ON
Parameter setting mode
Working
Input types & Input range
Set mode
Low temperature limit.
High temperature limit.
LED Indications
Alarm Types
Error Messages
Sets cycle time for PID action.
Sets proportional band.
Sets integration time.
Sets differential time.
Sets the
hysteresis
1
Runs auto tuning.
Set control action for relay1 / SSR.
20
21
22
23
24
Sets Control1 output.
25
Lock keypad.
26
Level2 Parameter
27
28
12
Input value scaling point 2.
13
To set reverse scaling for Analog input.
Sets time delay between output relay restart.
16
To set baud rate for communication.
To set device ID.
29
30
Level3 Parameter
TCW-S2
Содержание TCW-S1-UR2-230AC
Страница 2: ......