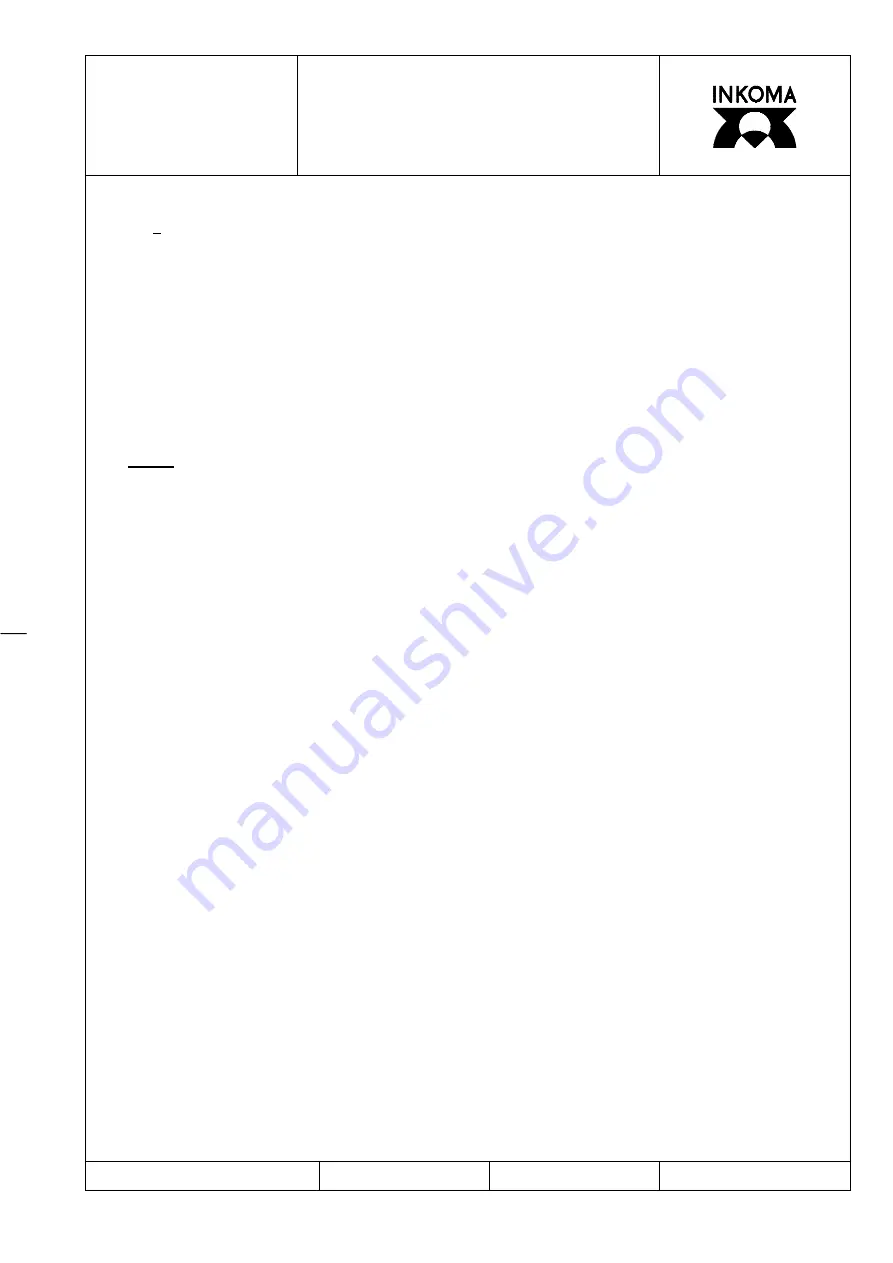
Datum: 29.05.2006
Installation/Maintenance
of Precision Screw Jacks
(HSG)
Seite 2 von 4
T 7-031-03
INKOMA Maschinenbau GmbH
Neue Reihe 44,
D-38162 Schandelah
Tel.: 0 53 06/ 92 21 - 0
Fax: 0 53 06/ 92 21 - 50
Internet: www.INKOMA.de
1.2 Oil Lubrication
Synthetic gear oil to ISO VG 460 DIN 51 519 specification (Klübersynth GH 6-460) is used.
As the efficiency of the worm geared drive is dependent on the quality of the oil, we recommend that either the original
specification or a direct equivalent is used when replacing the oil. It is vital that high standards of cleanliness be maintained (use
a filter or a fine sieve).
During operation oil is deposited inside the gear housing. After commissioning the oil level should be re-checked at
standstill
and replenished if necessary. The correct oil filling is when the level is in the upper third of the sight glass.
During the running-in period metal particles are deposited in the oil. The oil should initially be changed after 50
operating hours. Further oil changes, depending on the load, should be at 1000 operating hour intervals or after 2
years at the latest.
Oil should be drained when the gearbox is warm. Flush with a clean, thin flushing oil before refilling.
NOTE:
Klübersynth GH-6 oils do not mix with Mineral Oils and synthetic hydro-carbons. We therefore recommend that the
gearbox be flushed out with the same oil with which it will be refilled.
During operation oil is deposited inside the gear housing.
Please refer to us for the correct amount of oil required.
Check the level at standstill and top up if necessary. The correct oil filling is when the level is in the upper third of the sight glass.
1.3 Lubrication of Trapezoidal Spindles
The spindle should be generously greased. Dependent on the application and whether protection is fitted, the spindle should be
regularly cleaned and re-greased.
In this case
Klueber Microlube GB-0, Klueberplex GE 11-680
(or equivalent
specification)
can be used.
1.4 Lubrication of Ball-Screw Spindles (KGS)
The Ball-Screw should be cleaned at regular intervals. Lubrication is via the Ball Nut and may be with grease or oil.
1.4.1 Grease Lubrication (KGS)
For grease lubrication, Mineral Oils Grade K2K, DIN 51825 are recommended. If the load is in excess of 10% of the dynamic
load capacity of the spindle, greased with EP additives (KP2K, DIN 51825) should be used. For high speeds (nominal velocity
n*d>50000) Grade K1K or KP1K should be selected. Speeds below 2000 n*d require Consistency Class 3 (K3K or KP3K, DIN
51825). The frequency of re-lubrication depends on the ambient conditions. Generally, re-lubrication should be every 200-600
operating hours. As a guide the amount of grease is 1 cm
3
per nut for 1 cm of spindle diameter. Only greases having the same
specification should be used.
1.4.2 Oil Lubrication (KGS)
Lubricating Oils Class CL to DIN 51517 Part 2 are suitable. At operating temperature the oil should have a viscosity of
68-100 mm
2
/s. For high speeds (speeds of n*d>50000) select oils having a Viscosity Class of ISO VG 46-22. For speeds below
2000 n*d use oils having Viscosity Class ISO VG 150-460. For oil bath lubrication the spindle should be 0.5 -1 mm below the oil
surface. Oil feed for oil circulation should be 3-8 cm3/h per ball circuit.