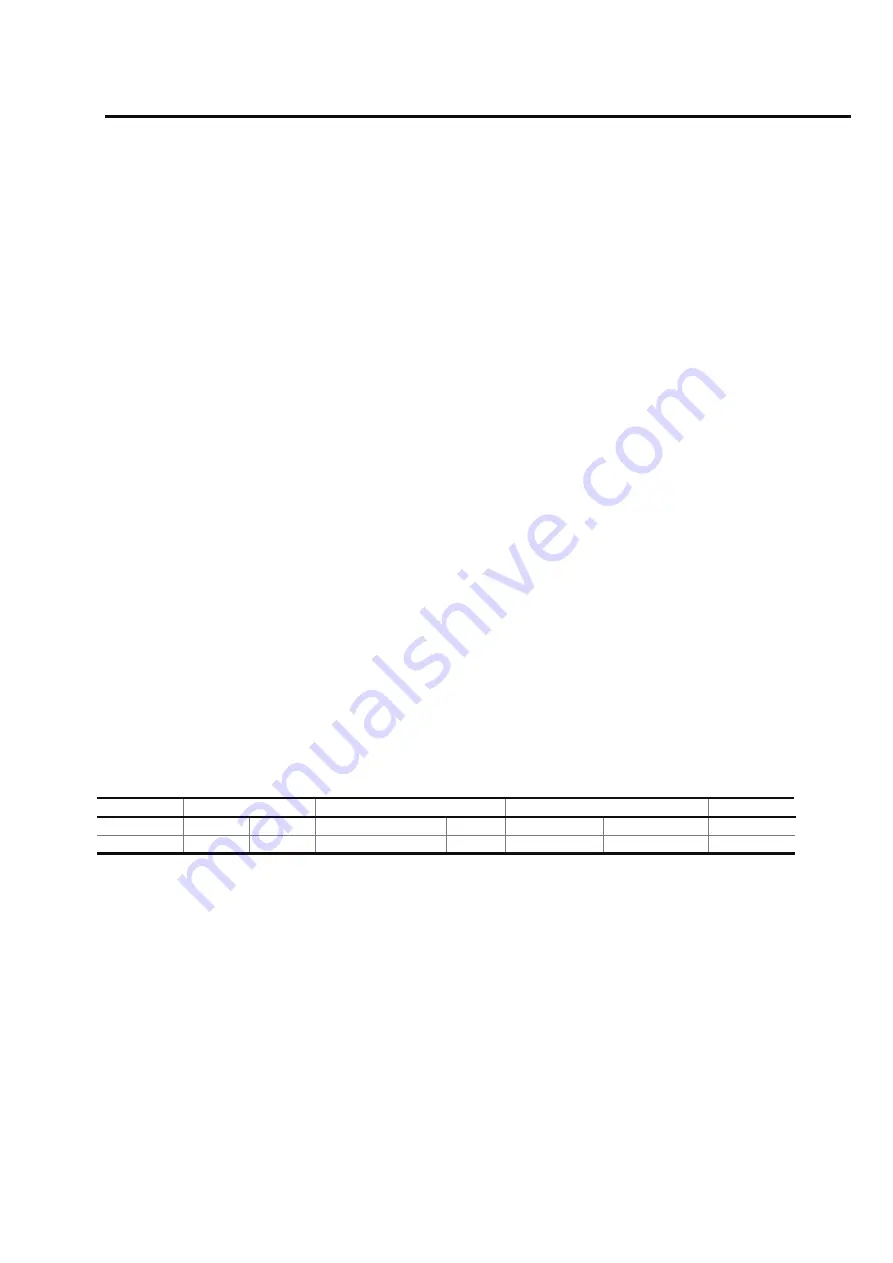
Manual No. 54771142 (7/01)
(
19
)
07/18/01
Receiver separator Discharge Piping
The receiver separator discharge piping must be furnished by the customer. Refer to the appropriate
separator fitting location for a typical piping arrangement for these units. A minimum pressure valve and a
manual shut-off valve is supplied with each unit and must be piped into the customer’s system as
indicated. The minimum pressure valve is supplied to maintain approximately 125 psig (862 kPa) in the air
receiver tank to ensure proper oil circulation and also to prevent excessive oil carryover into the customer’s
air service system. The manual shut-off valve must be installed between the minimum pressure valve and
the customer’s air service system to serve as an isolation valve.
In addition, whenever this unit is connected to a high volume customer’s service air system, a terminal
check valve must also be installed downstream of the minimum pressure valve and the isolation valve to
prevent air from the system from bleeding back into the compressor system on shutdown.
Wiring
The compressor is protected against overheating by a thermal-type discharge air temperature switch
located in the compressor discharge piping. A “normally-closed” type thermal switch, factory set at 248
°
F
(120
°
C), is supplied as standard equipment on these units. This switch is supplied for 12/24 volt DC. As
an option, this switch may be supplied for 125 volt AC. A thermal sensor switch, also set at 248
°
F (120
°
C),
normally closed, is provided as extra protection in the receiver separator. It is to be wired in series with the
airend temperature switch by the user and then into the end user’s shutdown system. The end user’s
system must be capable of initiating shutdown of the driver engine within 3-5 seconds of opening of either
of the shutdown switches. This switch is supplied for 12/24 volts DC, with optional AC switches available
as an option.
Driver
The installation of a CM Series Compressor with any drive such as a power take-off drive or a hydraulic
motor drive is very flexible. The proper rotation of the compressor is clockwise when viewed from the
driver end.
NOTE
Because the compressor is of the axial
screw type, the rotation cannot be changed.
MODEL
CAPACITY
TORQUE REQUIRED
POWER REQUIRED
INPUT
CFM
M
3
/MIN.
POUND - FEET
N
.
M
BHP
KILOWATTS
RPM
XHP900
900
25.4
1152
1563
395
294
1800
Note: Power requirements include fan.
A drive shaft from the source of power take-off is used to drive the compressor. It is extremely important
that the angularity of the drive shaft, including the universal joints, be within the limits specified by the
manufacturer. The power take-off shaft and the compressor rotor drive shaft must always be parallel.
This gives the same angle at each universal joint and prevents excessive wear. The forks of the universal
joint on the drive end must be installed parallel to the forks on the driven end universal. There are many
types of universal joints that can be used. However, a constant velocity universal joint as previously
described will reduce the possibility of torsional vibration. If a slip joint or spline is used on the drive
system, it should be placed between the two universal joints for best results.
It is NOT permissible to directly belt drive this unit, or use any configuration of drive that puts side
load on the compressor drive shaft. Belt or other side loads must be supported by external
bearings.
Содержание XHP900CM
Страница 9: ...Manual No 54771142 7 01 9 07 18 01 SAFETY CARD...
Страница 15: ...Manual No 54771142 7 01 15 07 18 01 fold...
Страница 42: ...xhp900cm doc 42 7 18 2001...
Страница 48: ...xhp900cm doc 48 7 18 2001...
Страница 49: ...xhp900cm doc 49 7 18 2001...
Страница 50: ...xhp900cm doc 50 7 18 2001...
Страница 62: ...xhp900cm doc 62 7 18 2001...
Страница 63: ...xhp900cm doc 63 7 18 2001...
Страница 64: ...xhp900cm doc 64 7 18 2001...
Страница 71: ...xhp900cm doc 71 7 18 2001 DECALS ITEM PART NUMBER DESCRIPTION A 36522050 Warning Rotating Fan 2 DECALS A...
Страница 72: ...xhp900cm doc 72 7 18 2001 ITEM PART NUMBER DESCRIPTION A 36527810 I R Signature 1 ea Side A...
Страница 76: ......
Страница 77: ...xhp900cm doc 77 07 18 01...