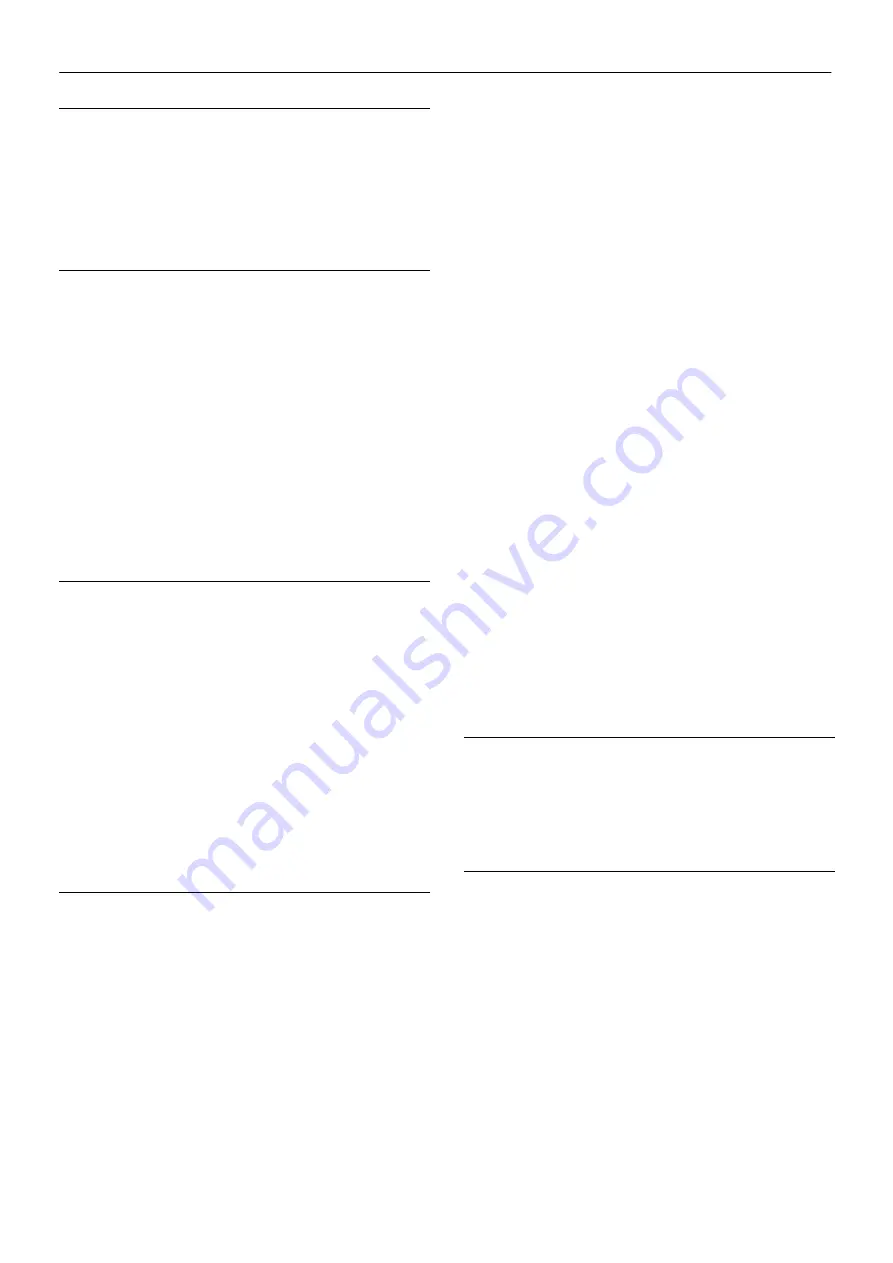
GENERAL INFORMATION
22
SL, SM & SH 90, 110, 132, 150, 200, 250 &300 (50Hz)
L, H & HH 125, 150, 200, 250, 300, 350 & 400 (60Hz)
COOLING SYSTEM (WATERCOOLED)
The intercooler, aftercooler and oilcooler are shell and tube type
heat exchangers. The intercooler and aftercooler are ”water in the
shell” design. the oil cooler employs ”water in the tube”.
Cooling water flows through each of the three components in
parallel. A water solenoid shut off valve is provided in the water
discharge line from the package.
The tube bundles are removable for ease of cleaning.
ELECTRICAL SYSTEM
The electrical system of the compressor utilises the
microprocessor–based INTELLISYS controller. The standard
electrical/electronic components, contained within a readily accessible
enclosure include:
1. INTELLISYS controller
2. Star–Delta compressor motor starter, with auxiliary contacts and
overload relays
3. Cooling fan manual motor starter and circuitbreaker or fuses
4. Power supply board
5. Main motor overload relay
6. Control relay control transformers, and fuses
Star–delta type starter
By use of the Star–Delta type starter, the compressor motor can be
started and accelerated using a greatly reduced ”inrush” electric
current. The starter is completely automatic and controlled by the
INTELLISYS controller. Refer to the electrical schematic.
CAPACITY CONTROL
Automatic unloaded start
The compressor will always start in the unload mode. When
unloaded, the inlet valve is nearly closed, the blowdown valve is open
and the compressor is operating at minimum power.
On–off line control
On–off line control will deliver air at full capacity (compressor
maximum efficiency condition) or will operate at zero capacity
(compressor minimum power condition). The compressor is controlled
by the INTELLISYS controller responding to changes in plant air
pressure. The INTELLISYS controller energises the load solenoid
valve (1SV) to actuate the hydraulic cylinder and load the compressor
whenever plant air pressure drops below the on–line pressure set
point. The compressor will then operate to deliver full capacity air to the
plant system. If the plant air system pressure rises to the off line set
point of the INTELLISYS, the load solenoid valve is de–energised, the
hydraulic cylinder is de–actuated allowing the machine to unload. The
compressor will continue to run with minimum power draw.
AUTOMATIC START/STOP CONTROL OPTION
Many plant air systems have widely varying air demands or large
air storage capacity which allows for automatic standby air capacity
control.
The Intellisys system has been designed to carry out this function
utilising a software module. Automatic Start–Stop is standard on all
Sierra compressors.
During periods of low air demand, if the line pressure rises to the
upper set point, the INTELLISYS controller begins to time out. If the line
pressure remains above the lower set point for as long as the set time,
the compressor will stop. At the same time, the Automatic Restart
warning message will appear in the display to indicate the compressor
has shut down automatically and will restart automatically. An
automatic restart will occur when the line pressure drops to the lower
set point.
The upper and lower set points and shutdown delay time are set on
the control panel. There is a 10 second delay after shutdown during
which the compressor will not restart even if line air pressure drops
below the lower set point. This is to allow the motor to come to a
complete stop and the controller to collect current data of operating
condition. If line air pressure is below the lower set point at the end of
10 seconds, the unit will start unless the load delay timer is set greater
than 10 seconds.
Delay load time
This is the amount of time the line pressure must remain below the
online set point before the compressor will load or start (if the unit was
stopped due to an auto start/stop situation). This timer will not delay
loading after a start or if the time is set to 0. When the delay load timer
becomes active, the display will switch to line pressure (if not displaying
line pressure at that time) and then display the delay load countdown.
Once the countdown reaches 0, the unit will load or start and the display
will return to line pressure. The display select arrows are inactive during
the delay load countdown.
Automatic start/stop operation
When in operation, the compressor must meet two specific timing
intervals before the Intellisys controller will stop the unit in an Automatic
Start/Stop situation.
A timer prevents the compressor from automatically starting more
than 6 times an hour by requiring the unit to run at least 10 minutes after
each automatic start.
This 10 minute run period can be loaded, unloaded or a combination
of the two and allows dissipation of heat generated within the motor
windings at start.
When the compressor has completed the settings of the timer, the
controller stops the compressor, turns on the automatic restart light and
displays AUTOMATIC RESTART in the message display.
Pressure sensor 4APT continues to monitor the package discharge
pressure and sends information to the controller which automatically
restarts the compressor when the pressure falls to the on–line setting.
REMOTE LOAD / UNLOAD OPTION
This option allows the operator to remotely load and unload the
machine.
With the option enabled, two different switches can be wired (refer
to the electrical schematic for wiring locations). The switches are
customer supplied.
REMOTE START/STOP OPTION
The remote start/stop option allows the operator to control the
compressor from a remote mounted start/stop station. This option may
be selected from the customer set–up routine.
With the option enabled, two different switches can be wired to the
INTELLISYS for remote start/stop. (Refer to the electrical schematic
for wiring locations). The switches are customer supplied and must be
of momentary type. The stop switch contacts are normally closed / the
start switch contacts are normally open.
The following notice must be permanently fixed to the unit in a
prominent position.
(Factory fitted on 60Hz machines).
Содержание Sierra H 125
Страница 2: ......
Страница 4: ......
Страница 12: ...DECALS 60Hz 8 SL SM SH 90 110 132 150 200 250 300 50Hz L H HH 125 150 200 250 300 350 400 60Hz...
Страница 13: ...DECALS 60Hz 9 SL SM SH 90 110 132 150 200 250 300 50Hz L H HH 125 150 200 250 300 350 400 60Hz...
Страница 14: ...DECALS 60Hz 10 SL SM SH 90 110 132 150 200 250 300 50Hz L H HH 125 150 200 250 300 350 400 60Hz...