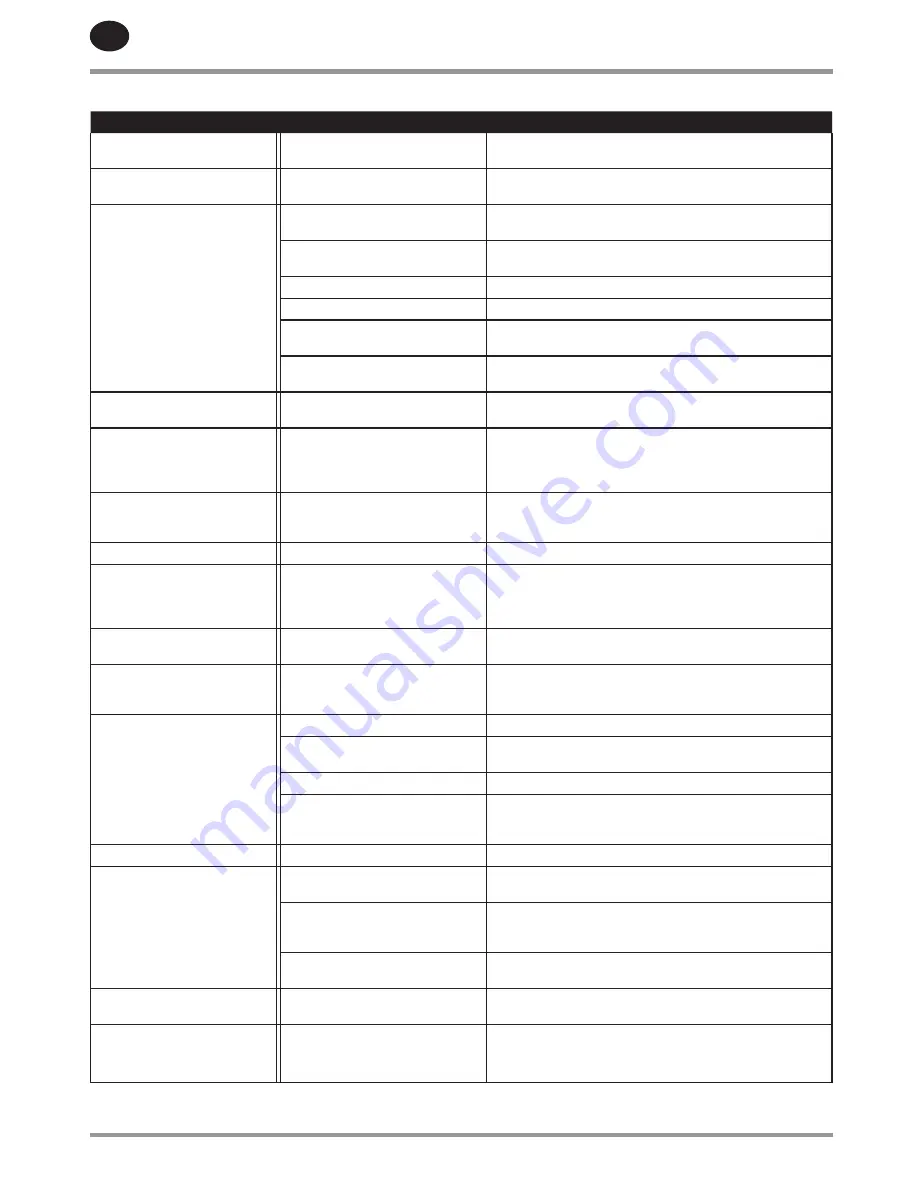
EN
EN-12
47612267 Rev B
Table 4: Controller Faults (indicated on the controller)
FAULT
CAUSE
REMEDY
Emergency stop.
Emergency stop button has
been pressed.
Identify reason why, repair fault, disengage button and
reset controller.
Blower motor overload.
Blower is blocked, damaged or
blower motor is faulty.
Remove blockage, repair or replace damaged
components.
High airend discharge
temperature.
Compressor operating above
rated pressure.
Check and modify settings. Review system requirements
and contact your local
Ingersoll Rand
representative.
Low coolant level.
Check for leaks. See also ‘discharge air is contaminated
with coolant’. Top up coolant.
High ambient temperature.
Review installation and system parameters.
Insufficient cooling air.
Check ducting and cooling air path.
Dirty, blocked coolant cooler
(cooling air side).
Clean or replace.
Blower motor direction of
rotation incorrect.
Wire correctly.
Check setpoints.
Controller software has been
changed.
Recalibrate all sensors and check setpoints.
Remote start failure.
Remote start button is pressed
after compressor is running or
remote start button remains
closed.
Check operation of buttons or operating procedures.
Remote stop failure.
Remote stop button remains
open and either start button is
pressed.
Check operation of buttons or operating procedures.
Sensor failure.
Sensor is missing or faulty.
Install, repair or replace faulty sensor.
Compressor trips indicating
a high compressor
temperature.
Insufficient cooling taking place.
If compressor is watercooled or sea watercooled, check
that the cooling water is flowing. Check that there is no
air in the water cooling system. Check that the strainer is
not blocked.
Controller has tripped the
compressor.
A fault has occurred.
Repair fault / reset controller.
Invalid calibration.
Calibration done with pressure
in compressor.
Depressurize and re calibrate with pressure pipe to
sensor disconnected. If fault still exists, replace pressure
transducer.
Low sump pressure.
System leak.
Located and repair.
Minimum pressure check valve
faulty.
Repair with service kit.
Blowdown valve faulty.
Repair with service kit.
Loss of control power.
Check 110V circuit breaker.
Check wiring.
Check contactor KM1.
Check motor rotation.
Drive system fault.
Contact your local
Ingersoll Rand
representative.
Change separator element
and/or high sump pressure.
Faulty pressure transducer
measurement.
Calibrate and validate the wet sump and package
discharge transducers.
Moisture separator condensate
drain trap faulty.
Ensure condensate drain system is functioning
properly, and condensate is being drained. See Table 4:
Troubleshooting Chart.
Separator element dirty or
blocked.
Change separator element.
Machine stops but no alarm
message
Loss of outputs of control power.
Check controller outputs (110V AC) power supply (fuses/
mini circuit breaker).
Motor current fault
Loss of control power.
Sump pressure too high.
Faulty motor or Airend.
Check control power circuit and breaker.
Check separator element pressure drop.
Contact your local Ingersoll Rand representative.
RELEASED 11/Feb/2019 01:43:20 GMT