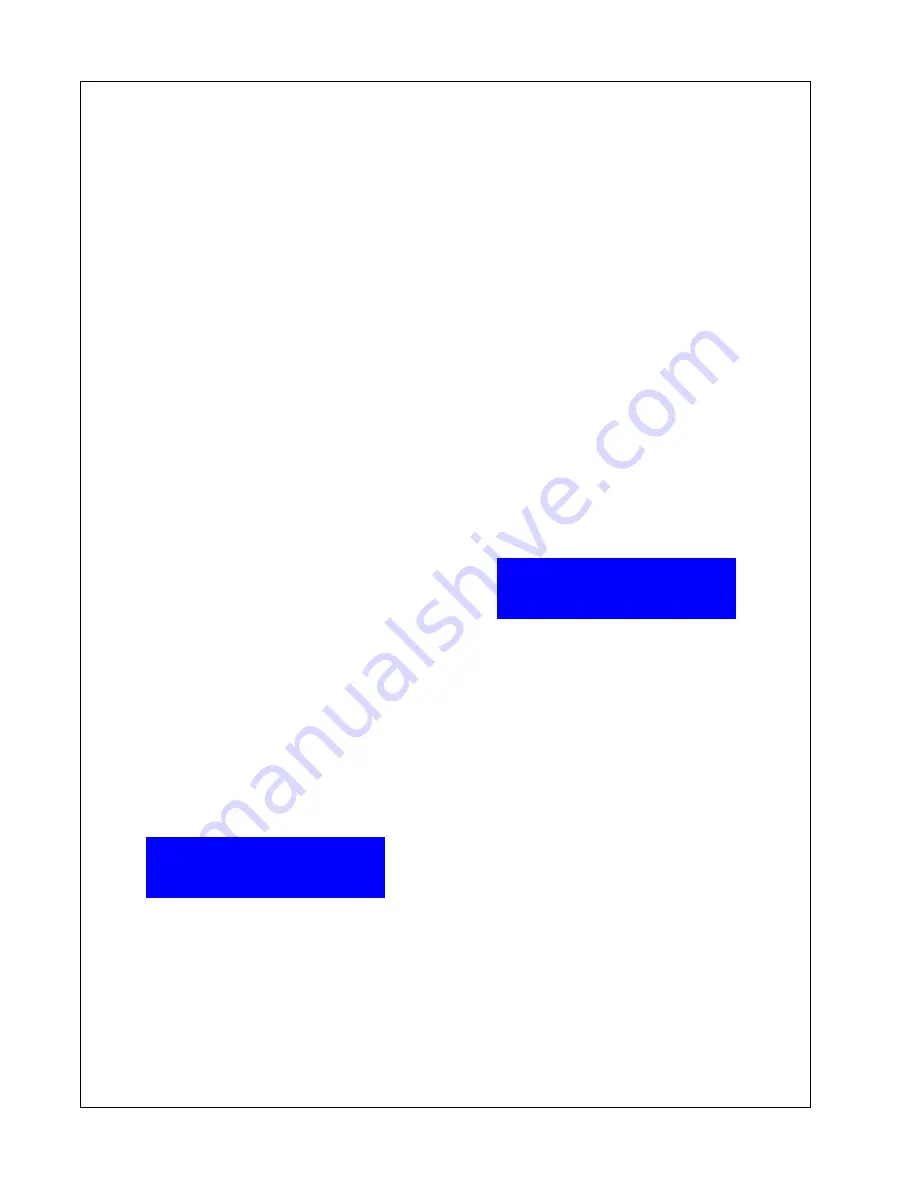
Operating & Maintenance Manual
Maintenance
42
Book: 22904767 (6/06) Rev. A
start-up. During operation observe the
gauges and any lamps for proper functioning.
Refer to Operating Controls, for the normal
readings.
Fuel Tank
CLEAN fuel in the fuel tanks is vitally
important and every precaution should be
taken to ensure that only clean fuel is poured
or pumped into the tank.
When filling the fuel tank on this unit, by
methods other than a pump and hose, use a
CLEAN non-metallic funnel.
Battery
Keep the battery posts-to-cable connections
clean, tight and lightly coated with a grease.
Also the electrolyte level in each cell should
cover the top of the plates. If necessary, top-
up with clean distilled water.
Fasteners
Visually check entire unit in regard to bolts,
nuts and screws being properly secured.
Spot check several capscrews and nuts for
proper torque. If any are found loose, a more
thorough inspection must be made. Take
corrective action.
Radiator
NOTICE
The use of water alone in this engine
can result in major engine failure.
Hoses
Each month it is recommended that all of the
intake lines to and from the air cleaners, the
engine cooling system hoses and all of the
flexible hoses used for air, oil, and fuel be
inspected.
To ensure freedom from air leaks, all rubber
hose joints and the screw-type hose clamps
must be absolutely tight. Regular inspection
of these connections for wear or deterioration
is necessary.
Premature wear of both the engine and
compressor is ASSURED whenever dust-
laden air is permitted to enter the engine’s
combustion chamber or compressor intake.
The flexible hoses used in the fuel, oil and air
lines on these units are primarily used for
their ability to accommodate relative
movement between components. It is
important they be periodically inspected for
wear and deterioration. It is also important
the operator does not use the hoses as
convenient hand hold or steps. Such use can
cause early cover wear and hose failure.
NOTICE
Piping systems operating at less than
150 psi (1050 kPa) may use a special
nylon tubing. The associated fittings
are also of a special “push-in” design.
If so, features are as follows:
Pulling on the tubing will cause the inner
sleeve to withdraw and compress, thus
tightening the connection. The tubing can be
withdrawn only while holding the sleeve
against the fitting. The tubing can be
removed and replaced numerous times
without losing its sealing ability.
To install the nylon tubing, make a mark (with
tape or grease pencil) approximately 7/8 inch
from the end of the tubing. Insert the tubing
into the sleeve and “push-in” past the first
resistance to the bottom. The mark should be
approximately 1/16 inch from the sleeve, for
the 3/8 inch O.D. tubing; 1/8 inch for the 0.25
inch O.D. tubing. This will ensure that tubing
is fully engaged in the sealing mechanism.
Содержание P250WJDU
Страница 5: ...Book 22904767 6 06 Rev A 7 Foreword ...
Страница 8: ...10 Book 22904767 6 06 Rev A Always use Ingersoll Rand Replacement parts ...
Страница 9: ...Book 22904767 6 06 Rev A 11 Safety ...
Страница 16: ...Operating Maintenance Manual Safety 18 Book 22904767 6 06 Rev A ...
Страница 17: ...Book 22904767 6 06 Rev A Noise Emission ...
Страница 23: ...Book 22904767 6 06 Rev A General Data ...
Страница 26: ...Operating Maintenance Manual General Data 28 Book 22904767 6 06 Rev A ...
Страница 27: ...Book 22904767 6 06 Rev A 29 Operation ...
Страница 30: ...Operating Maintenance Manual Operation 32 Book 22904767 6 06 Rev A ...
Страница 37: ...Book 22904767 6 06 Rev A 39 Maintenance ...
Страница 46: ...Operating Maintenance Manual Maintenance 48 Book 22904767 6 06 Rev A ...
Страница 47: ...Book 22904767 6 06 Rev A 49 Lubrication ...
Страница 49: ...Book 22904767 6 06 Rev A 53 Trouble Shooting ...
Страница 56: ...Operating Maintenance Manual Trouble Shooting 60 Book 22904767 6 06 Rev A ...