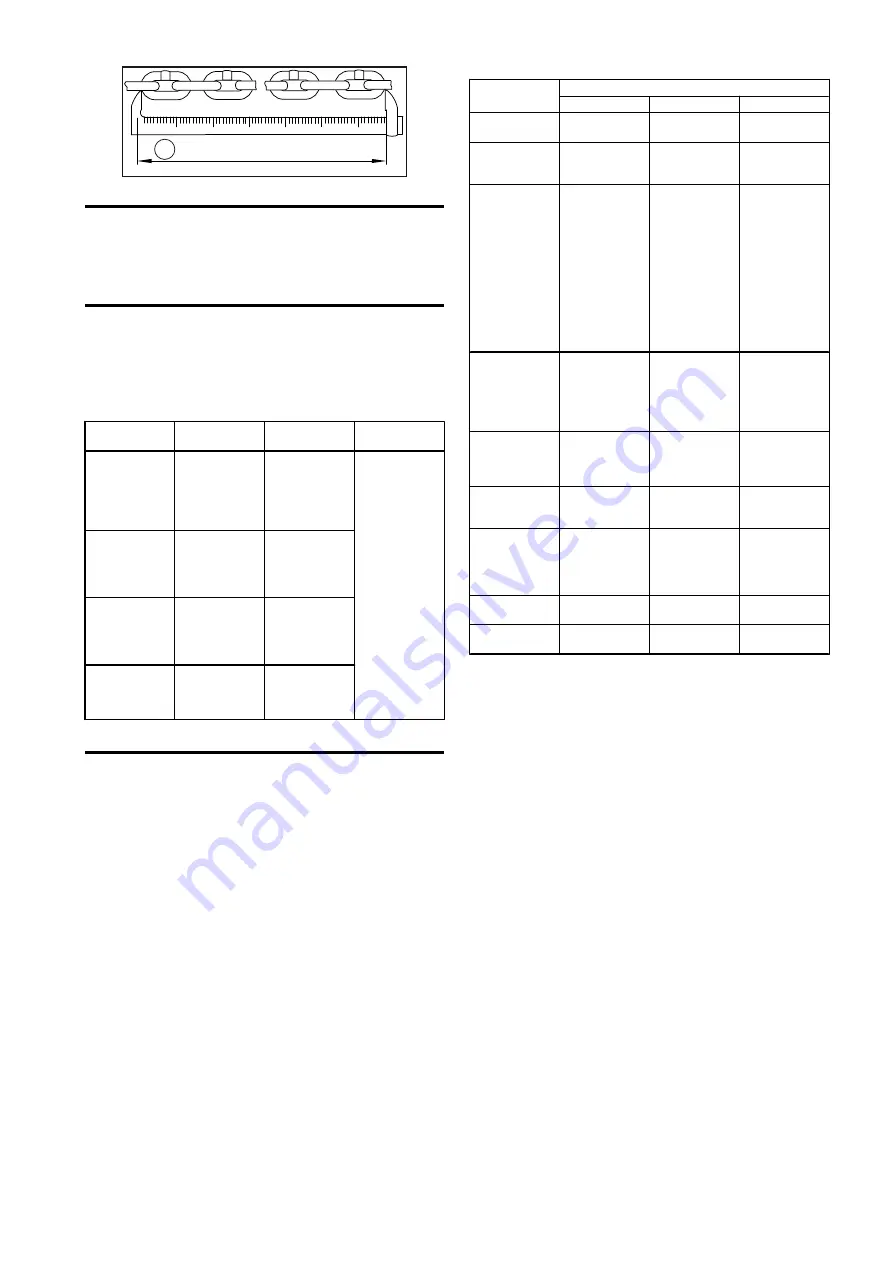
Gauge Length over ‘N’ links with
light load suspended from hook
A
(Dwg. MHP0455)
n
Records and Reports
Inspection records, listing all points requiring periodic inspection should be
maintained for all load bearing equipment. Written reports based on severity of
service, should be made of the condition of critical parts as a method of documenting
periodic inspection. These reports should be dated, signed by the person who
performed the inspection, and kept on file where they are readily available for review.
n
Maintenance Schedule
After considering the previous section, regarding loading, it is possible to determine
the necessary maintenance intervals. Given that the load spectrum has been
determined and the duration of use has been recorded, the following chart is
intended to be used to determine service intervals for major overhauls and unit gear
box lubrication. Accordingly, the following table is given:
Table 5: Service intervals for major overhauls
Load Spectrum
(LF)
Characterization
Time Before
Overhaul (hours)
Gear Box Grease
Change (*) (hours)
L1 - Light
0 < LF < = 0.50
Hoist is usually
subject to very
small loads and in
exceptional cases
only to maximum
loads.
3200
200
L2 - Medium
(normal)
0.5 < LF < = 0.63
Hoist is usually
subject to small
loads but rather
often to maximum
loads.
1600
L3 - Heavy
0.63 < LF < = 0.80
Hoist is usually
subject to medium
loads but
frequently to
maximum loads.
800
L4 - Heavy
0.80 < LF < = 1.00
Hoist is usually
subject to
maximum or almost
maximum loads.
400
(*) Operation specifics may warrant modification to these intervals.
n
Periodic Maintenance
While the information in the preceding section is used for major service intervals,
many items need to be checked at greater frequency depending on usage. The
following information is provided for that purpose, but it is important to note that
the information in the preceding section, regarding hours of service, is applicable in
all conditions of use. Refer to Table 6 ‘Periodic Maintenance/Inspection Interval’
Table 6: Periodic Maintenance/Inspection Interval
Item
Conditions
Normal
Heavy
Severe
Requirements of
frequent inspection
Annually
Semiannually
Quarterly
Evidence of loose
bolts, nuts, rivets,
snap rings
Annually
Semiannually
Quarterly
Evidence of worn
corroded, distorted,
or cracked parts
such as suspension
housing, chain
attachments,
clevises, yokes,
suspension bolts,
shafts, gears,
bearings, pins,
rollers, and locking
and clamping
devices
Annually
Semiannually
Quarterly
Evidence of
damage to hook
retaining nuts or
collars or pins, used
to secure the
retaining members
Annually
Semiannually
Quarterly
Evidence of
excessive wear, or
damage, to load
wheels
Annually
Semiannually
Quarterly
Evidence of
excessive wear on
motor or load brake
Annually
Semiannually
Quarterly
Evidence of
damage to
supporting
structure, and/or
trolley, if used
Annually
Semiannually
Quarterly
Product and safety
label for legibility
Annually
Semiannually
Quarterly
End connections of
load chain
Annually
Semiannually
Quarterly
Form 47099007 Edition 3
3
Содержание MHP3238
Страница 11: ...SERVICE NOTES Form 47099007 Edition 3 11 ...
Страница 12: ...R www ingersollrandproducts com ...