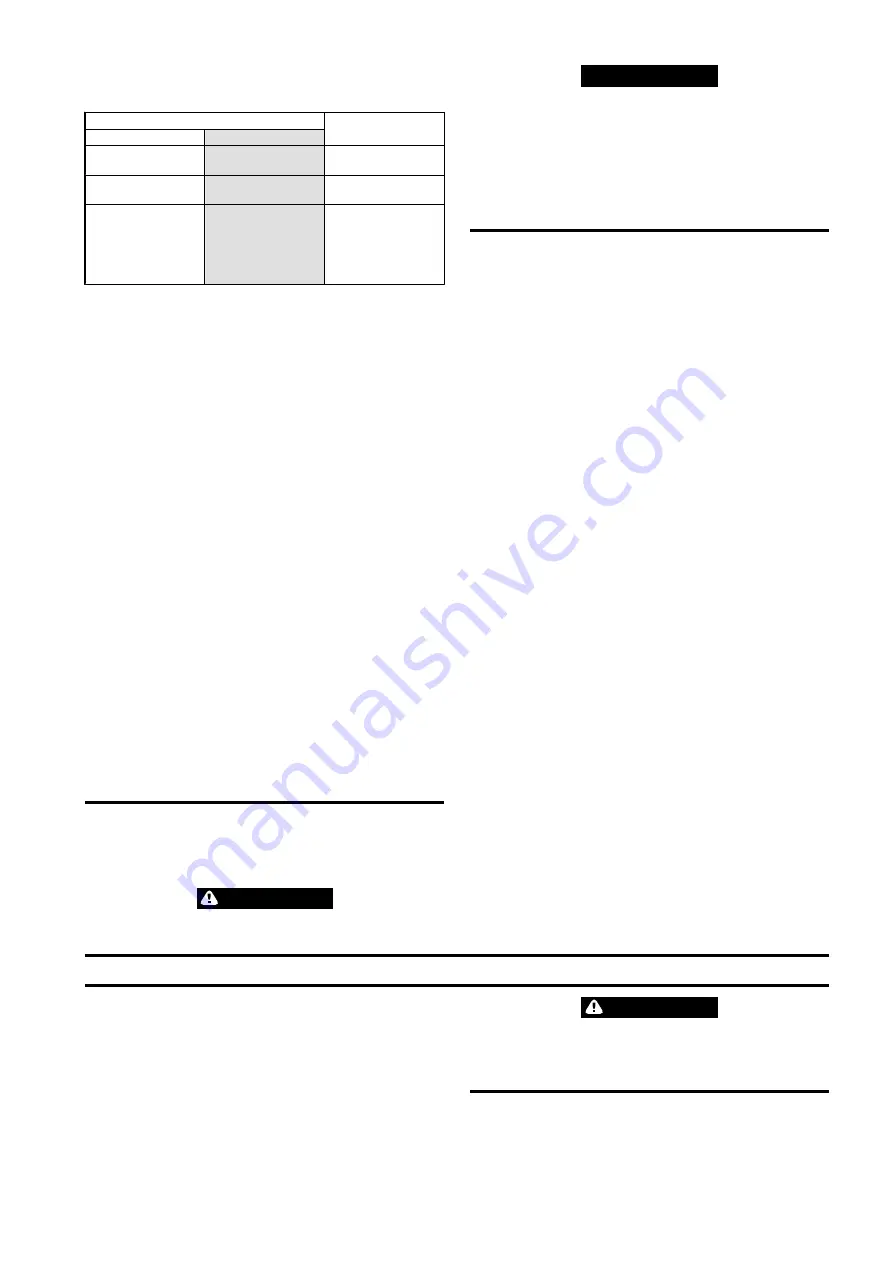
Use a premium anti-wear (AW) hydraulic fluid in the hydraulic system. The following
specifications are intended to serve as a general guide in selecting suitable oils.
Table 5: Recommended Hydraulic Oil
Temperature
Recommended Hydraulic
Oil
Fahrenheit
Celsius
above 32° F
0° C
ISO VG 46
(SSU 230-240 @ 100° F)
0° to 32° F
-17.7° to 0° C
ISO VG 32
(SSU 60-165 @ 100° F)
below 0° F
below -17.7° C
Consult local oil company
representative for oil
having a maximum
viscosity of 7,400 SSU’s at
the minimum temperature
encountered.
n
Filters
Filters should be equipped with dirty filter indicators, which should be checked daily.
Replace filters if indicators show filter is dirty. It is also recommended that filters be
changed if hydraulic oil is changed or a major component (pump, valve, motor, etc.)
is repaired or replaced.
When product is installed with its own hydraulic system or when there is no filter in
existing circuit, a partial flow microfilter should be installed between control valve
and reservoir. This filter should be rated at Beta 200=6μm. Filters must include an
integral 345 kPa/3.45 bar (50 psi) bypass check valve which will open when filter
element is filled to 80% capacity.
Refer to ‘Filter Maintenance’ in “MAINTENANCE” section for servicing information.
n
Connections
When repairing or servicing any hydraulic lines or fittings in the system, always flush
each line and connection of all foreign contaminants before making the final
connection. Always cap or plug open connections or lines. Verify port connections
match motor and installation information provided.
n
Pump
Ensure pump used with motor is capable of producing pressure and volume as specified
for the product.
n
Controls
Ensure control valve moves smoothly in both directions before operating product with
full load.
n
Motor
For optimum performance and maximum durability of parts, ensure hydraulic supply
does not exceed recommended pressures and flows. When feasible motor should be
installed as near as possible to the pump. Refer to Table 2 ‘Specifications’
on page 4. Motor case drain lines must be ported to reservoir and must not exceed
207 kPa/2 bar (30 psi).
n
Reduction Gear
Product is shipped with petroleum based cooling oil. Prior to operation, check oil
level. Refer to “LUBRICATION” section on page 7.
n
Chain Container
Refer to Dwg. MHP2658 and MHP3059 in Product Parts Information Manual.
Check the chain container size to make sure the length of the load chain is within
the capacity of the chain container. Replace with a larger chain container if required.
WARNING
• Allow chain to pile naturally in the chain container. Load chain that does not
pile naturally can chafe excessively, leading to sparks.
NOTICE
• Make certain to adjust the balance chain so that the chain container does not
contact the load chain.
n
Attaching Limit Stop
Refer to “MAINTENANCE” section in Product Maintenance Information Manual.
1. On hoists without a chain bucket, slide buffer and limit stop washer onto chain.
2. Install limit stop as described under “Load Chain Replacement”.
3. Run hoist slowly in the both directions to verify limit stops activate and hoist
ceases to operate.
n
Trolley Rack Drive (optional)
Install the trolley rack drive onto the support beam. Installation should only be done
by authorized service personnel.
n
Pre-Installation Checks
Refer to Dwg. MHP2990 on page 10,
A
. Rack;
B
. Pinion;
C
. Maintain clearance
between rack and pinion teeth of 0.16 inch (minimum) to 0.20 inch (maximum) [4
to 5 mm] to prevent pinion binding during operation. Measure gap between the
outside diameter of drive pinion and root of rack segment.
Before welding the rack segments onto the trolley beam, install the rack segments
on the bottom of the beam lower flange and clamp in place. Mount the trolley on the
lower beam flange. Measure the gap between the outside diameter of the drive pinion
and root of rack segment teeth. As shown in Dwg. MHP2990, the trolley drive pinion
and rack teeth must have a 0.16 to 0.20 inch (4 to 5 mm) clearance.
n
To Adjust Clearance
Refer to Dwg. MHP2991on page 10,
A
. Mounting Capscrew;
B
. Jam Nut;
C
.
Adjustment Screw.
There is an adjustment screw located below the reducer adapter.
1. Loosen capscrews attaching trolley drive to sideplate.
2. Loosen jam nut and rotate adjustment screw to achieve clearance as shown inDwg.
3. Tighten jam nut and mounting screws.
If a larger adjustment is required:
1. Add shims between the rack segment and beam to decrease distance.
2. Remove material from rack segment to increase distance.
n
Installing Rack Segments Onto Beam
Refer to Dwg. MHP1178 on page 10,
A
. Hoist Trolley Drive Assembly mounted this
side;
B
. Lower Beam Flange;
C
. Rack Segment;
D
. Fillet Weld: Allow 1/4 inch (6.5 mm)
clearance between edge of lower flange and rack segment. Apply weld to both sides
of rack segment. Refer to Dwg. MHP3016 on page 10,
A
. Stagger welds along rack;
B
. (Not to scale);
C
. Check clearance between racks;
D
. Use the rack guide for correct
track positioning.
Rack segments should be installed on the outside edge of the lower flange of the
trolley beam. Allow 1/4 inch (6.5 mm) clearance between the edge of the lower flange
and rack segment for fillet weld. The rack segments should be clamped tight against
the lower flange so that there is no sagging. Sagging of the rack could cause the drive
pinion to bind as it traverses along the runway beam.
Racks are provided in segments. These segments should be tack welded (refer to
Dwg. MHP3016 on page 10) in place and the trolley traversed the entire length.
During this movement observe for any high or low spots and correct. Also check each
segment connection for drive tooth contact and correct as necessary. When all
clearances are achieved, weld both sides of the rack to the beam flange to prevent
corrosion between the rack segment and beam.
OPERATION
It is recommended that the user and owner check all appropriate and applicable
regulations before placing this product into use. Refer to Product Safety Information
Manual.
The product operator must be carefully instructed in his or her duties and must
understand the operation of the product, including a study of the manufacturer’s
literature. The operator must thoroughly understand proper methods of hitching loads
and should have a good attitude regarding safety. It is the operator’s responsibility
to refuse to operate the product under unsafe conditions.
WARNING
• The product is not designed or suitable for lifting, lowering or moving people.
• Never lift loads over people.
• The hook latch is intended to retain loose slings or devices under slack
conditions. Use caution to prevent the latch from supporting any of the load.
• Refer to Product Safety Information Manual before operating any product.
n
Hydraulic System
Efficient operation of the product requires attention to hydraulic oil system. The most
important elements to ensure proper operation of the hydraulic system are:
Form MHD56465 Edition 3
5
Содержание Liftchain LC2H060S
Страница 11: ...SERVICE NOTES Form MHD56465 Edition 3 11...
Страница 12: ...www ingersollrandproducts com...