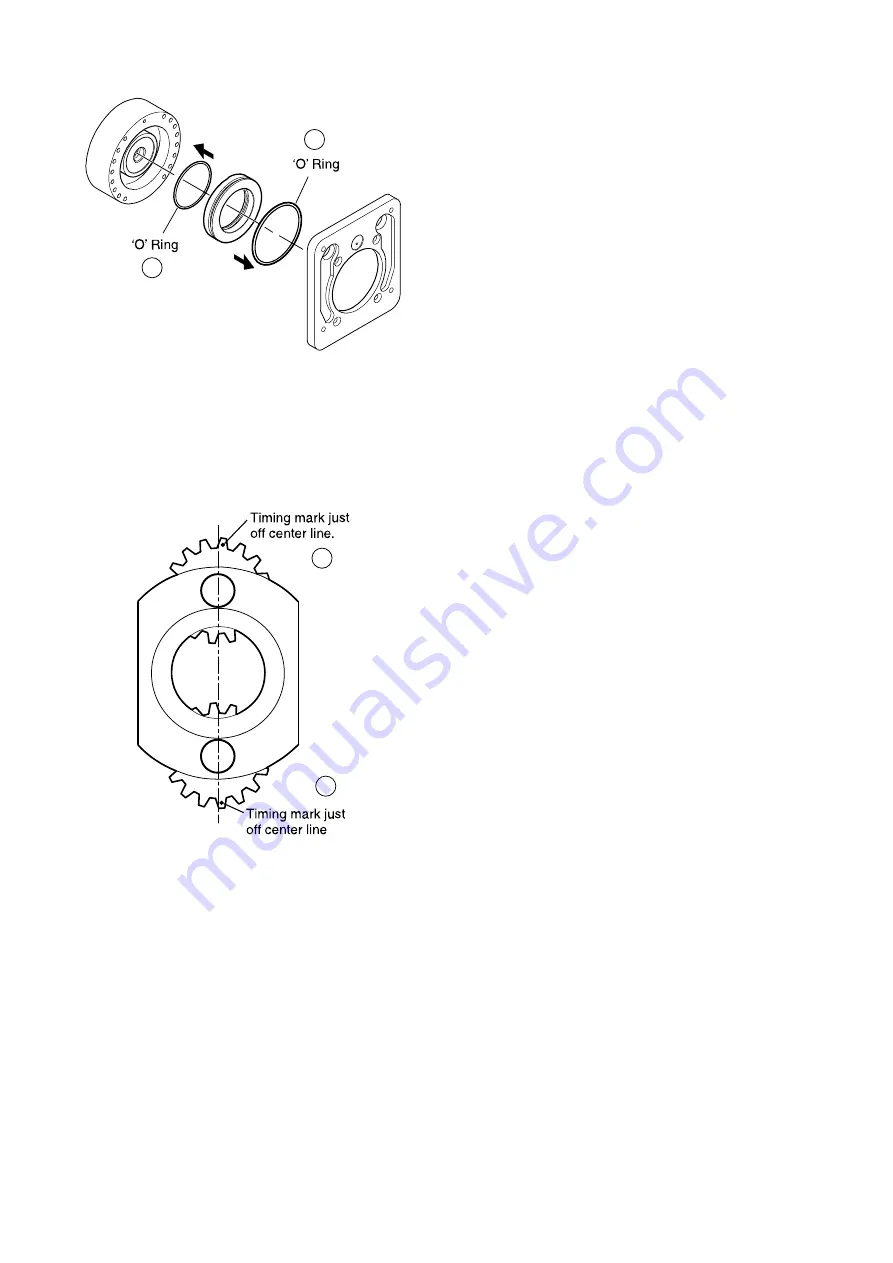
16. Install piston (692) in brake housing (689). Ensure ‘O’ ring in bore of piston is
located toward brake housing. Refer to Dwg. MHP1627 on page 14, A. ‘O’ ring.
A
A
(Dwg. MHP1627)
17. Lubricate ‘O’ rings (659) and (686) and install on brake housing (689).
18. Install gasket (667) and brake housing assembly on gear housing (668). Check
holes are correctly aligned.
19. Use Loctite® 243 on the capscrews (650) and (653) threads. Refer to “TORQUE
CHART” on page 19 for torque requirements.
20. Install retainer ring (687) on sun gear (678).
21. Install coupling (690) on sun gear (678).
22. Install spacer (694), friction discs (695) and drive discs (696) on coupling (690).
23. Install plates (657) on flange (651) and secure with capscrews (658).
24. Install two mufflers (680) in plates (657).
25. Install plugs (656) with seal washers (660) in gear housing (668) and brake
housing (689).
A
A
(Dwg. MHP1560)
n
18 ton and 25 ton Rack Drive 2nd Stage Trolley Reduction Gear
Assembly
Refer to Dwg. MHP3181.
1. Install oil seal (652) and bearing (130) in flange (651). Lip of seal must be toward
planetary gear side.
2. Assemble planetary assembly if previously disassembled.
a. Install bearing (660) in planet gear (661).
b. Install a thrust bearing (659) and washer (658) on either side of planet gear
(661).
c. Install assembled planet gear in planet support (655).
d. Install planet pin (657) in planet support (655). Align pin hole with hole in
planet support.
e. Tap pin (662) into planet support to secure planet pin.
3. Install bearing (130) on planet support (655).
4. Install planet support (655) in flange (651).
5. Install reduction gear assembly on trolley side plate with capscrews (270) and
washers (271).
6. Install drive gear (136) with key (656) on planet support (655).
7. Install washer (135), washer (119) and capscrew (133) to secure drive gear (136).
n
Hoist Motor and Disc Brake Installation
Refer to Dwgs. MHP2999 and MHP3038.
1. Lubricate and install ‘O’ ring (6) on brake housing (61).
2. Press piston assembly in brake housing (61). Internal ‘O’ ring (64) must enter
brake housing first. Avoid damaging ‘O’ rings.
3. Install plates in brake housing (61) in the following order: Friction plate without
clips (66) then drive plate (67) then friction plate with clips (72) then drive plate
(67). Repeat this plate sequence finishing with a friction plate with clips (72).
Align drive plate slots with slots in splined hub (65).
4. Install splined hub (65).
5. Lubricate and install ‘O’ rings (64) and (6) on piston (63) and reaction plate (68)
into brake housing (61).
6. Align holes and install gasket (7) on brake housing (61).
7. Ensure retainer ring (10) is installed on spline of drive gear (80).
8. Install springs (69) in motor housing (76).
9. Carefully install assembled brake in motor housing (61) and secure with
capscrews (62). Install capscrews (62) with Loctite® 243 or equivalent. Splined
hub must locate on motor drive gear (80) and remain engaged in drive plates.
Refer to “TORQUE CHART” on page 19 for torque requirements. For a correct
assembly the brake housing must be completely inside the motor housing.
10. Install plug (1) and washer (151) in brake housing.
11. Mount motor and brake assembly on end cover (73).
n
Motor Emergency Stop and Overload Assembly
Refer to Dwgs. MHP3037 and MHP3038.
1. Lubricate and install seal (189) and ‘O’ ring (201) on base plate (199).
2. Lubricate and install ‘O’ ring (197) on plunger (198).
3. Install diaphragm (196) on plunger and secure with nut (194) and washer (195).
4. Install plunger assembly on base plate and ensure plunger slides easily in the
bore of the base plate.
5. Install spring (213) on motor cover (83).
6. Install seal (210) on cap (202).
7. Install seal (203) on cap (211).
8. Install cap (202), washer (206), spacer tube (209), washer (208), cap (211),
diaphragm (212), and washer (206) into valve seat (205) and secure with
capscrew (62). Apply Loctite® 243 or equivalent to capscrew (62) threads. Do not
over tighten, apply torque for snug fit.
9. Lubricate and install ‘O’ rings (204) on valve seat (205).
10. Lubricate and install ‘O’ ring (191) on regulating screw (192).
11. Screw regulating screw (192) into emergency stop end cover (183).
12. Lubricate spring (193) with grease and install into regulating screw (192).
13. Install setscrew (102) with Loctite® 243 or equivalent onto emergency stop end
cover.
14. Install seal (189) on axle (188).
15. Install axle (188) into valve seat (186).
16. Install the second seal (189) on axle (188).
17. Lubricate and install ‘O’ rings (187) on valve seat (186).
18. Install valve assembly into emergency stop end cover.
19. Lubricate ball (47) with grease and install into emergency stop end cover.
20. Install gasket (91) with grease on motor cover.
21. Install emergency stop end cover assembly on motor cover and secure with
capscrews (103). Refer to “TORQUE CHART” on page 19 for torque
requirements.
22. Lubricate and install ‘O’ rings (70) on emergency stop end cover.
23. Install setscrew (180).
24. Install plug (182).
n
Trolley Assembly
Refer to Dwg. MHP3155
1. Install seals (336), bearings (335) and spacer (333) in sprocket (334).
2. Install bushing(s) (338) in support(s) (330).
3. Position sprocket assembly in support and install axle (327).
4. Install capscrews (317), lockwashers (318) and caps (319) on one end of shafts
(329).
5. Install support(s) (330) and spacers on shafts.
6. Record quantity and position of spacers (326), (327) and (328) for later
reassembly. Install spacers on shafts (329).
7. Carefully install remaining side plate on shafts (329).
8. Install capscrews (317), lockwashers (318) and caps (319) on shafts (329) to retain
side plates (301).
9. Install hoist on support (330) with capscrews (331) and lockwashers (332).
Trolley Wheel Assembly
1. Install bearings (324) in wheel (325) and secure with retainer ring (323).
2. Tap axle (322) into bearings (324). Install retainer ring (321).
3. Install wheel assembly in side plate (301). Secure with spacer (314), locknut (315)
and locknut (316).
4. Repeat steps 1 to 3 for remaining wheels.
n
Trolley Motor and Reducer Assembly
Refer to Dwg. MHP3169.
1. Install trolley motor and reducer assembly on side plate (301).
2. Install capscrews (62) and lockwashers (44) or (63) that secure trolley motor and
reducer assembly to trolley side plate (301). Refer to
“TORQUE CHART” on page 19 for torque requirements.
3. Connect hoses to pendant and hose (614) to hoist motor.
n
Four Function Pendant Assembly
Refer to Dwg. MHP3062 with emergency stop or MHP3061 without emergency stop.
1. Assemble protectors (170) and ‘O’ rings (53) and (171) on valves (165).
2. Insert valve (165) assemblies into pendant handle (514) and attachments (right)
(524) and (left) (523).
3. Install levers (503) with pin (502) in pendant handle (514).
4. Install capscrews (525) and (527) in pendant handle and attachments (right) and
(left).
5. Install balls (47), springs (46) and plugs (518) into pendant handle and
attachments (right) and (left).
6. Install plug (615) or emergency stop valve (164) into pendant handle.
7. Install fittings (603) into top of pendant handle and attachments (right) and (left).
Install lifting eye (501) into top of pendant handle.
8. Facing pendant handle operation side, place levers (522) such that lever
direction indicates ‘UP’ on left hand side and ‘DOWN’ on right hand side. Install
pin (529) ensuring pin inserts through levers and locates on opposite side of
pendant handle.
14
Form MHD56473 Edition 2
Содержание LC2A060S
Страница 16: ...SERVICE NOTES 16 Form MHD56473 Edition 2...
Страница 17: ...SERVICE NOTES Form MHD56473 Edition 2 17...
Страница 18: ...SERVICE NOTES 18 Form MHD56473 Edition 2...
Страница 20: ...R www ingersollrandproducts com...