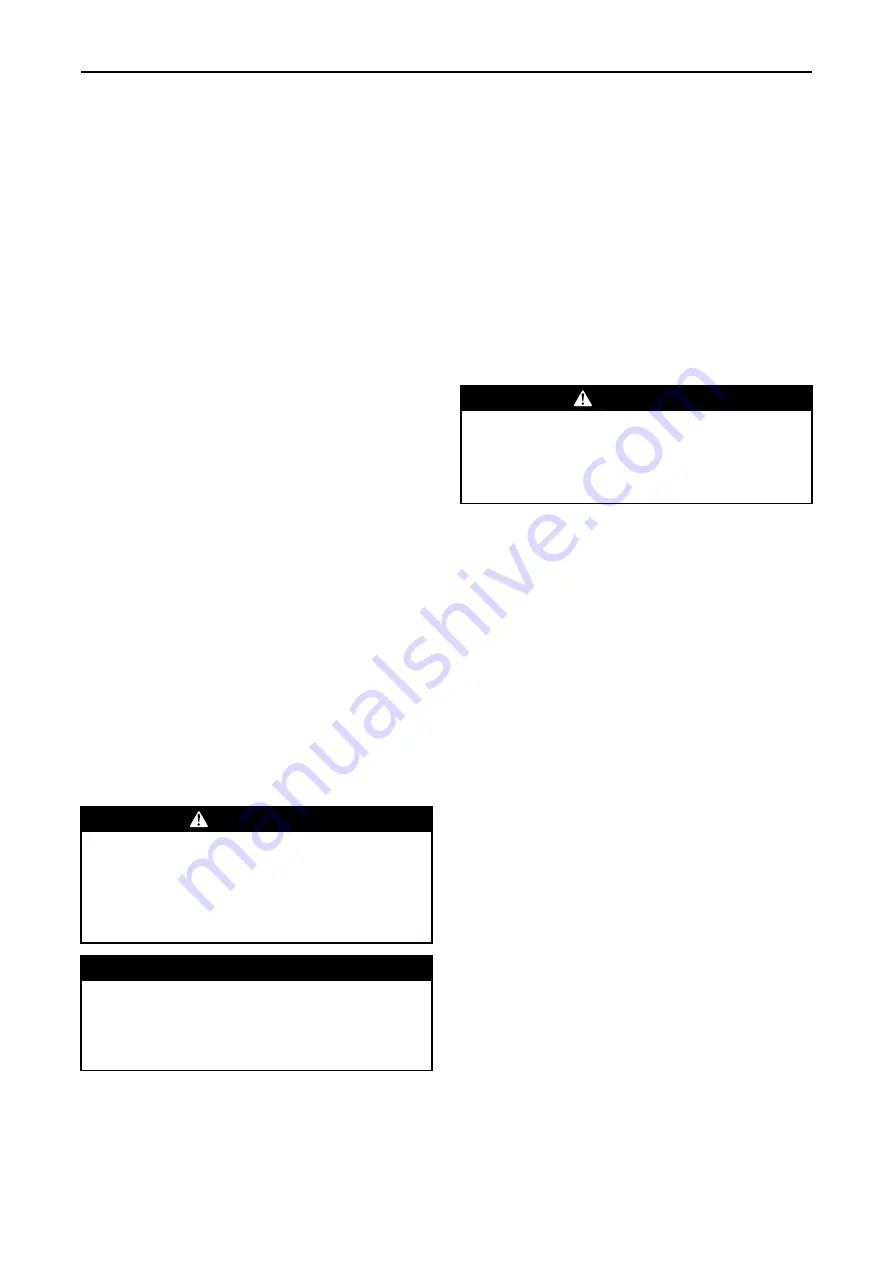
9
Adjust Clearance
Refer to
There is an adjustment screw located below reducer
adapter.
1. Loosen capscrews attaching trolley drive to
sideplate.
2. Loosen jam nut and rotate adjustment screw to
achieve clearance.
3. Tighten jam nut and mounting screws.
If a larger adjustment is required.
1. Add shims between rack segment and beam to
decrease distance.
Installing Rack Segments Onto Beam
Refer to
and
Rack segments should be installed on the outside edge
of the lower flange of the trolley beam. Allow 1/4 inch
(6.5 mm) clearance between the edge of the lower
flange and rack segment for fillet weld. The rack
segments should be clamped tight against the lower
flange so that there is no sagging. Sagging of the rack
could cause the drive pinion to bind as it traverses
along the runway beam.
Racks are provided in segments. These segments
should be jack welded (refer to
) in place
and the trolley traversed the entire length. During this
movement observe for any high or low spots and
correct. Also check each segment connection for drive
tooth contact and correct as necessary. When all
clearances are achieved, weld both sides of the rack to
the beam flange to prevent corrosion between the rack
segment and beam.
Chain Container
When a chain bucket is used, always connect the free
end of the chain to the hoist. Attach the chain container
to the hoist. Run bottom block to the lowest point and
run hoist in the ‘UP‘ direction to feed the chain back
into the container.
W
WA
AR
RN
NIIN
NG
G
• Allow chain to pile naturally in the chain
container. Load chain that does not pile
naturally can chafe excessively, leading
to sparks.
N
NO
OT
TIIC
CE
E
• Make certain to adjust the balance chain
so that the chain container does not
contact the load chain.
Attaching Limit Stop
1. Install limit stop as described under ‘Load Chain
Replacement‘.
2. Run hoist slowly in the both directions to verify
limit stops activate and hoist ceases to operate.
Accu-Trol® Pendant
Refer to
Check that all hose connections are tight and that hoses
are not twisted or crimped. Refer to Product Manual
MHD56014 for hose connections and all other
operation information.
Pendant lengths up to 66 ft (20 m) are available.
Contact factory for pendant lengths greater than 66 ft
(20 m).
C
CA
AU
UT
TIIO
ON
N
• To avoid damaging pendant hose, make
sure strain relief cable, not pendant
hose, is supporting weight of pendant.
Initial Operating Checks
Hoists are tested for proper operation prior to leaving
factory. Before hoist is placed into service the following
initial operating checks should be performed.
1. After installation of trolley mounted hoists, check to
ensure hoist is centered below trolley.
2. Remove side plate connecting plates.
3. Check for air leaks in supply hose and fittings to
pendant, and from pendant to manifold.
4. When first running hoist or trolley motors a small
amount of light oil should be injected into inlet
connection to allow good lubrication.
5. When first operating hoist and trolley it is
recommended that motors be driven slowly in both
directions for a few minutes.
6. Operate trolley along entire length of beam.
7. Inspect hoist and trolley performance when raising,
moving and lowering test load(s). Hoist and trolley
must operate smoothly and at rated specifications
prior to being placed in service.
8. Check that trolley (if equipped) and hook movement
is in same direction as arrows or information on
pendant control.
9. Raise and lower a light load to check operation of
hoist brake.
10. Check hoist operation by raising and lowering a
load equal to rated capacity of hoist 4 to 6 inches
(100 to 150 mm) off floor.
11. Check operation of limit devices.
12. On trolley units, check ‘O’ ring (360) on breather
plug (362) in trolley drive piston motor has been
removed.