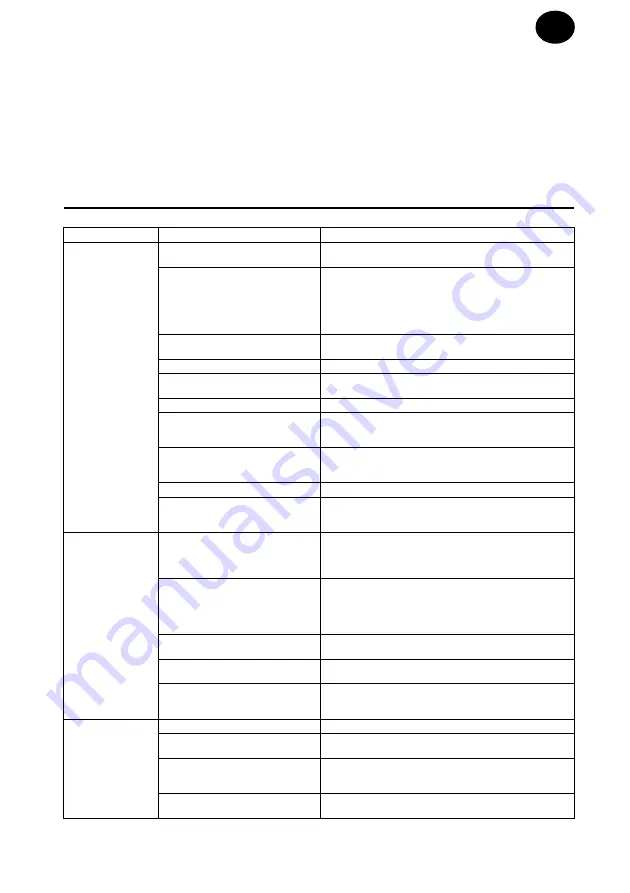
16575003_ed1
EN-4
EN
counterclockwise
to tighten them. Tighten the joint
between 20 and 25 ft.-lb. (27.1 and 33.9 Nm) torque.
15. Using finger pressure, press the Seal Cup Assembly (55),
felt end trailing, onto the rotor end of the Collet Body (58).
Press the Cup Assembly to the shoulder of the Collet
Body. Saturate the felt with
Ingersoll Rand
No. 50 Oil.
16. Insert a 5/32" pin through the opening in the Extension
Housing and the cross hole in the Spindle to keep the
Spindle from rotating. Thread the Collet Body and Seal
Cup Assembly onto the Spindle and tighten it between 14
and 19 ft.-lb. (19 and 26 Nm) torque. Install the Extension
Housing Plug (52).
17. Slide the Spindle Bearing Shield (56), large opening first,
over the Collet Body and into the Extension Housing.
Using snap ring pliers, install the Shield Retainer (57) in
the internal groove in the Extension Housing.
18. Slide the Handle Clamp (61) with the assembled handle
onto the Extension Housing and position the handle in
the most comfortable position. Tighten the Mounting
Screw Nut (64) between 10 and 12 ft.-lb. (13.5 and 16.3
Nm) torque.
19. Insert the Collet (59) into the Collet Body and thread the
Collet Nut (60) onto the Collet Body.
20. Use the Collet Body Wrench (82) on the flats of the Collet
Body and the Collet Nut Wrench (81) on the Collet Nut to
tighten the Collet Nut.
Troubleshooting Guide
Trouble
Probable Cause
Solution
Low power or low free
speed
Insufficient air pressure
Check air line pressure at the Inlet of the Tool. It must be 90
psig (6.2 bar/620 kPa).
Clogged muffler elements
Disassemble the Tool and agitate bare Motor Housing and
Flange in clean kerosene. Back flush muffler elements by
blowing into the exhaust ports with an air gun until all
contaminants and obstructions are removed. If elements
cannot be cleaned, replace the Motor Housing and/or the
Flange.
Plugged Inlet Screen (2)
Clean the Inlet Screen with a stream of air or replace the
Screen.
Worn or broken Vanes (17)
Install a
complete
set of new Vanes.
Loose Extension Housing (51) or Gear
Case Adapter (32)
Tighten the Housing or Adapter to 20 to 25 ft.-lb. (27 to 34 Nm)
torque.
Worn or broken Motor Housing (9)
Replace the Motor Housing.
Internal air leakage in the Motor
Housing indicated by high air
consumption/low speed.
Replace the Motor Housing.
Grit buildup under the Throttle Lever
(10) restricting full Throttle Valve
Plunger (12) movement.
Remove the Throttle Lever and clean the groove in the Motor
Housing.
Bent stem on Throttle Valve (6)
Replace the Throttle Valve.
Front Seal Cup Assembly (20) dragging
against the shield of the Front Rotor
Bearing (21)
Reposition the Front Seal Cup Assembly.
Rough operation /
vibration
Improper lubrication or dirt buildup
Inject 3 cc of clean kerosene into the Inlet, operate the Tool for
30 seconds and
immediately
inject 3 cc of the recommended
oil into the Inlet and run the Sander long enough to coat the
internal parts with the oil.
Worn or broken Rear Rotor Bearing
(13) or Front Rotor Bearing
Replace the worn or broken Bearings. Examine the Front End
Plate (18), Front End Plate Spacer (19), Front Seal Cup
Assembly (20) and Rear Rotor Bearing Spacers (14) and
replace any damaged parts. If the attached rotor plate is
damaged, replace the Rotor (16).
Worn or broken Rear Spindle Bearing
(49) or Front Spindle Bearing (53)
Replace the Bearings.
Dirt contaminated Front Spindle
Bearing
Replace the Bearing.
Worn, bent or broken Spindle (44)
Replace the Spindle if, when mounted between centers, the
runout on the spindle body exceeds 0.002" T.I.R. or 0.0005"
T.I.R. on the bearing mounting diameters.
Excessive runout
Loose Collet Nut (60)
Tighten the Collet Nut until snug.
Worn or damaged Collet (59), Collet
Nut or Collet Body (58)
Replace the damaged component and retest.
Bent, worn or broken Spindle
Replace the Spindle if, when mounted between centers, the
runout on the spindle body exceeds 0.002" T.I.R. or 0.0005"
T.I.R. on the bearing mounting diameters.
Worn or damaged Front Spindle
Bearing
Replace the Front Spindle Bearing.
Содержание HDS Series
Страница 7: ...16575003_ed1 EN 6 EN Notes ...
Страница 8: ...www irtools com 2006 Ingersoll Rand Company ...