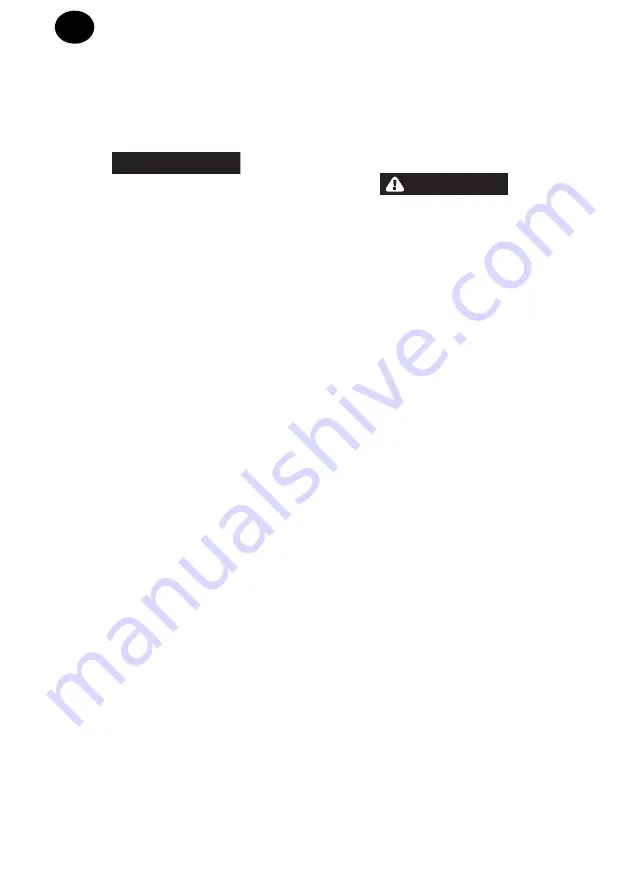
EN-3
16575003_ed1
EN
(19) that is opposite the large internal bevel. Continue
pressing until the felt end is flush with the end of the
spacer. Saturate the felt with
Ingersoll Rand
No. 50 Oil.
Place the assembled Spacer, Seal Assembly trailing,
onto the threaded hub of the Rotor. Make sure the Seal
Assembly enters the recess in the Front End Plate.
4. Stand the small hub of Rotor on the table of an arbor
press with the threaded end upward and press the Front
Rotor Bearing (21) onto the hub of the Rotor.
NOTICE
The Front Rotor Bearing is a flush ground bearing and
must be installed in a specific manner. The end of the
Bearing with a black stain or hash marks must be away
from the Spacer.
5. Grasp the assembled Rotor in copper-covered vise jaws
with the threaded rotor hub upward.
6. Thread the Rotor Pinion (28) onto the Rotor and using a
torque wrench, tighten the Pinion between 14 and 19 ft.-
lb. (19.0 and 25.8 Nm) torque.
7. Inject approximately 1/2 cc of
Ingersoll Rand
No. 68
Grease into the small recess at the bottom of the motor
housing bore. Drop the two Rear Rotor Bearing Spacers
(14) into the bottom of the motor housing bore.
8. Wipe each Vane (17) with a light film of oil and insert a
Vane into each vane slot in the Rotor.
9. Grasp the Rotor Pinion and insert the assembled Rotor
into the Motor Housing (9).
10. Assemble the Flow Ring (22) with the Flange (23) before
installing the Flange on the Housing. Mate the Flow Ring
to the end of the Flange without perforations. The
positioning of the Flow Ring is dictated by the desired
exhaust. To set the tool exhaust, proceed as follows:
a.
For front exhaust tools,
align the notched
projection on the edge of the Flow ring with the letter
"F" on the Housing.
b.
For rear exhaust tools,
align the notched
projection on the edge of the Flow ring with the letter
"R" on the Housing.
11. Carefully install the assembled Flange, Flow Ring
leading, onto the front of the Motor Housing. Make certain
the Ring properly engages the Housing.
Assembly of the Extension Housing
1. Form the Wick (29) into a circle and insert it into one end
of the Clamp Sleeve (30) and push it against the Wick
Retaining Ring (31). Saturate the Wick with
approximately 1.5 cc of
Ingersoll Rand
No. 63 Oil.
Do
not substitute any other oil.
2. Install the Clamp Sleeve over the Rotor Pinion (28), Wick
end first, against the Front Rotor Bearing (21).
3.
For HDS60, HDS90, TDS90 or TDS120,
apply a thin
coat of O-Ring lubricant to the Rear Spindle Bearing Seal
(49A) and install it in the annular groove on the Spindle
(44).
4.
For HDS10, HDS30, HDS45, TDS15, TDS30 or TDS45,
using a block with clearance for the gear pins, stand the
Spindle (44) on the table of an arbor press with the Collet
end upward. With the seal end of the Rear Spindle
Bearing (49) trailing, press the Bearing onto the large hub
of the Spindle.
For HDS60, HDS90, TDS90 or TDS120,
slide the Rear
Spindle Bearing (49) onto the shaft of the Spindle until it
covers the Seal. Use care not to damage the Seal when
sliding the Bearing over it.
5. Using snap ring pliers, install the Rear Spindle Bearing
Retainer (50).
6. Using a block with clearance for the gear pins or shaft
spline, stand the Spindle on the table of an arbor press
with the collet end upward. With the seal end trailing,
press the Front Spindle Bearing (53) onto the shaft of the
Spindle until it stops against the shoulder.
7. Install the Ring Gear Clamp (43) at the bottom of the
large opening in the gearing end of the Extension
Housing.
8. Moisten the Front Bearing Spindle Seal (54) with O-Ring
lubricant and install it in the second internal groove
inward from the collet end of the Extension Housing.
9. Insert the assembled Spindle, small end leading, into the
large end of the Extension Housing until the Rear Spindle
Bearing seats in the housing recess.
CAUTION
Maker certain the Front Spindle Bearing Seal is not
forced out of the groove or damaged during installation
of the Spindle.
10.
For HDS60, HDS90, TDS90 or TDS120,
if the Gear
Frame (35) was disassembled, proceed as follows:
a. Stand the Gear Frame on the table of an arbor press
with the notched face upward.
b. Using a needle bearing inserting tool, press a Spur
Gear Bearing (37), marked end trailing, into each of
the three holes in the Gear Frame until the trailing end
of the Bearing is flush with the counterbored face. Turn
the Gear Frame end for end.
c. Position a Spur Gear (36) in the Gear Frame with
the small end of the Gear
toward
the notched face
with the Bearings pressed into position.
d. Insert a Spur Gear Pin (38) through the hole in the
Gear Frame and in the Spur Gear and Spur Gear
Bearing.
e. Press a Spur Gear Bearing into the gear frame hole
around the Pin until the marked end of the Bearing is
flush with the counterbored face on the Gear Frame.
f. Repeat steps (c), (d) and (e) with the remaining Spur
Gears.
11.
For HDS10, HDS30, HDS45, TDS15, TDS30 or TDS45,
slide the Ring Gear (34) into the large end of the
Extension Housing. Coat the teeth of the Ring Gear and
the three Spindle Planet Gears (45 or 47) with
approximately 2 cc of
Ingersoll Rand
No. 68 Grease and
install the Gears with their Bearings (46 or 48) on the
spindle gear shafts. The planet gear teeth must mesh
with the ring gear teeth.
For HDS60, HDS90, TDS90 or TDS120,
coat the gear
train with approximately 2 cc of
Ingersoll Rand
No. 68
Grease and slide the assembled Gear Frame, notched
face leading, into the Housing against the Rear Spindle
Bearing. The Gear Frame must engage the spline of the
Spindle and force the Bearing to the bottom of the
bearing recess.
12.
For HDS10 or TDS15,
insert the Gear Head Spacer (42)
into the Extension Housing against the Spindle Planet
Gears. Insert the Gear Head (39), spline shaft leading,
into the Housing. Make certain the spline passes through
the Spacer and engages the teeth of the Gears. Grease
the Gear Head Planet Gears (40) and Bearings (41) and
install them on the shafts of the Gear Head. Make certain
the Teeth of the Gears and the Ring Gear mesh.
13. Install the Flange Clamp (24) on the small hub of the
Gear Case Adapter (32) and thread the Adapter, clamp
end leading, into the Motor Housing (9). This is a
left-hand thread;
rotate the Adapter
counterclockwise
to tighten it. Tighten the Adapter between 20 and 25 ft.-lb.
(27.1 and 33.9 Nm) torque.
14. Holding the assembled Extension Housing horizontally in
one hand and the assembled Motor Housing in the other
hand, insert the teeth of the Rotor Pinion with the teeth of
the three Planet Gears and thread the housings together.
This is a
left-hand thread;
thread the housings
Содержание HDS Series
Страница 7: ...16575003_ed1 EN 6 EN Notes ...
Страница 8: ...www irtools com 2006 Ingersoll Rand Company ...