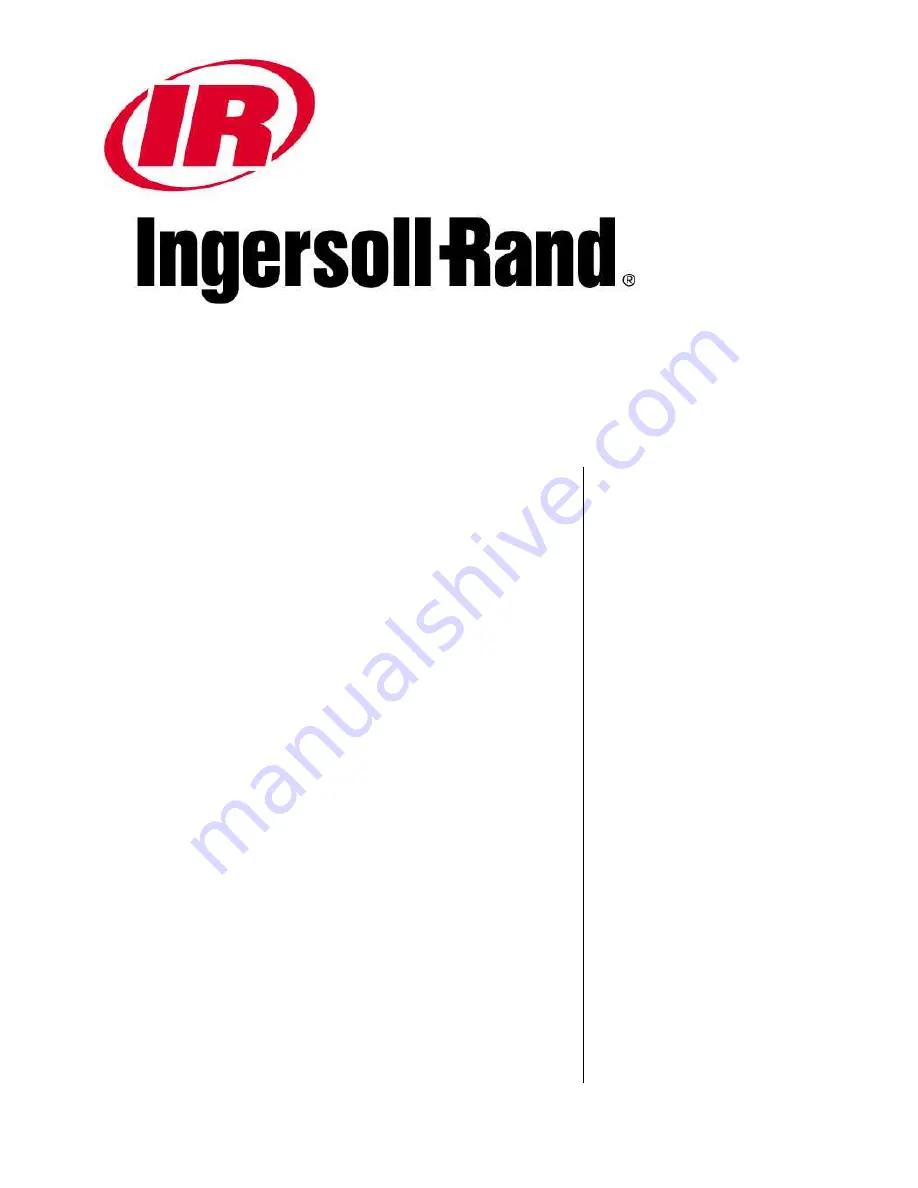
U
U
s
s
e
e
r
r
M
M
a
a
n
n
u
u
a
a
l
l
SERIES HC
Heat-of-Compression
Compressed Air Dryer
Models HC-3 – HC-239
IMPORTANT! BEFORE INSTALLING AND
OPERATING THE DRYER, IT IS
RECOMMENDED THAT THIS
MANUAL BE STUDIED AND
CLEARLY UNDERSTOOD.
THIS DRYER IS DESIGNED TO BE
USED ONLY WITH A NON-
LUBRICATED COMPRESSOR.
USE WITH A LUBRICATED
COMPRESSOR WILL VOID ALL
WARRANTIES AND MAY CAUSE
SEVERE DAMAGE.
Information
When making inquiries,
please provide the following
information:
1) Equipment Model Number
2) Equipment Serial Number
3) Equipment Operating
Pressure
4) Equipment Operating
Temperature
5) Approximate time in
service
6) Nature of Problem
For information, parts,
or service, contact your
local
I
I
n
n
g
g
e
e
r
r
s
s
o
o
l
l
l
l
-
-
R
R
a
a
n
n
d
d
Service provider or
reach us at
www.air.irco.com
Содержание HC-103
Страница 2: ...USER MANUAL Series HC Reference IR 222 Rev 3 Page 2 10 17 2013 ...
Страница 31: ...USER MANUAL Series HC Reference IR 222 Rev 3 Page 31 10 17 2013 SECTION 4 MAINTENANCE ...
Страница 40: ...USER MANUAL Series HC Reference IR 222 Rev 3 Page 40 10 17 2013 SECTION 5 TROUBLESHOOTING FAULTS ...
Страница 50: ......
Страница 52: ......
Страница 54: ......
Страница 56: ......
Страница 57: ...USER MANUAL Series HC Reference IR 222 Rev 3 Page 45 10 17 2013 SECTION 7 AUXILIARY MANUALS IF APPLICABLE ...
Страница 69: ...SAHARA MOISTURE TRANSMITTER Instruction Manual ...
Страница 85: ...USER MANUAL Series HC Reference IR 222 Rev 3 Page 46 10 17 2013 SECTION 8 CUT SHEETS ...
Страница 94: ...Page 4 MODEL 1700TM DIMENSIONAL PRINT 050205 Model 1700 IG ...
Страница 119: ...USER MANUAL Series HC Reference IR 222 Rev 3 Page 47 10 17 2013 SECTION 9 DRAWINGS ...
Страница 120: ......
Страница 121: ......
Страница 122: ......
Страница 123: ......
Страница 124: ......
Страница 125: ......
Страница 126: ......
Страница 127: ......
Страница 128: ......