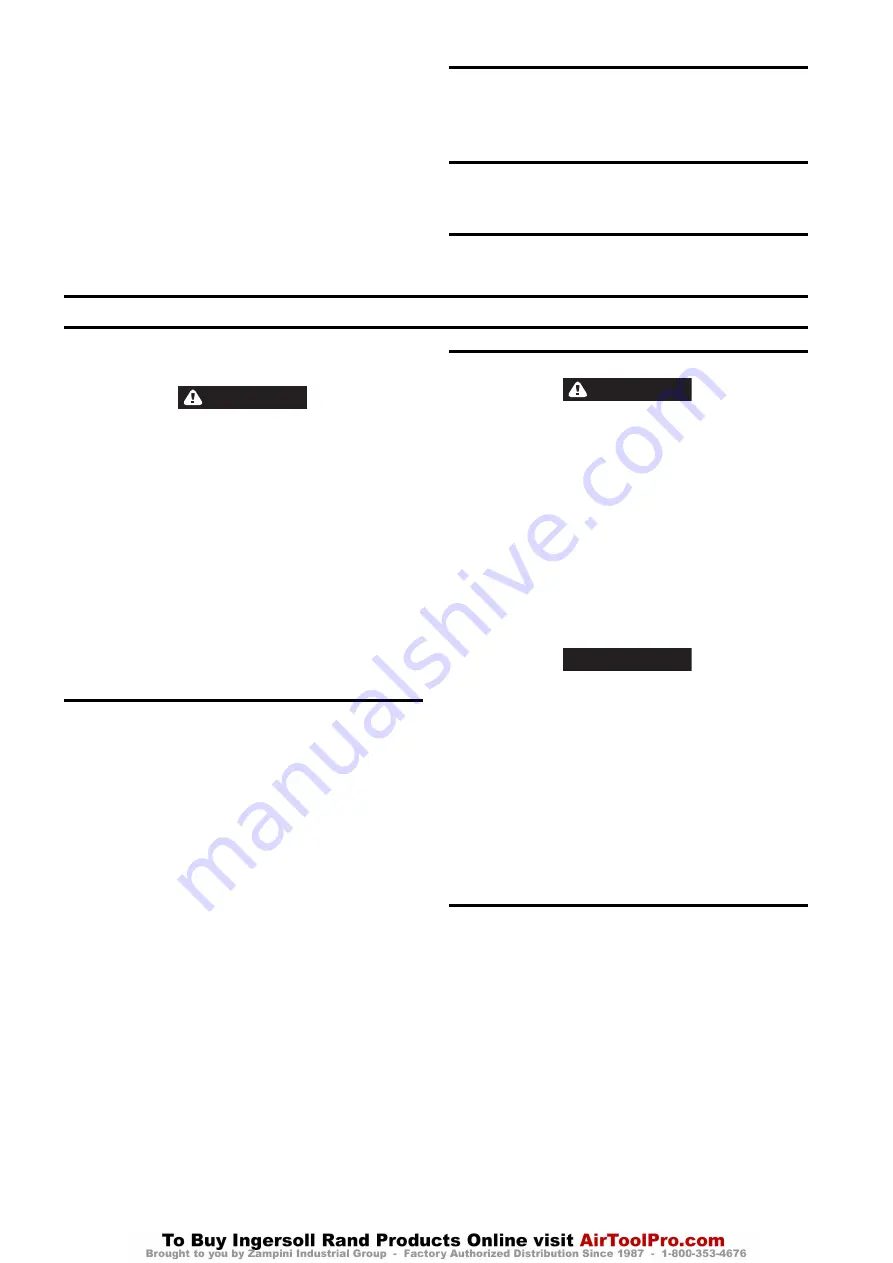
8
Form MHD56349 Edition 1
Automatic Band Brake (optional feature)
The automatic brake is a spring applied, air released brake which utilizes an air
actuated, spring loaded cylinder, that automatically disengages brake when motor is
operated. Air pressure in cylinder overcomes spring pressure to release brake. When
control valve is placed in neutral position, air in cylinder is vented and spring
automatically engages brake to prevent drum rotation.
The cylinder clevis must be kept properly adjusted to hold required load.
Automatic Disc Brake
The automatic brake is a spring applied, air released brake. Using an air actuated,
spring loaded piston, the brake automatically disengages when motor is operated
and engages when throttle is returned to neutral position.
Air pressure ported through brake housing overcomes spring pressure and moves
piston which releases brake. When control valve is placed in neutral position, air is
vented, spring pressure overcomes air pressure and spring pressure moves piston,
engages brake and prevents drum rotation.
Limit Switch
Pre-set limit switch settings prevent winch wire rope payout and haul-in by stopping
air flow to the winch motor when a set point has been reached. It is the owner’s and
operator’s responsibility to adjust winch operating limits prior to using the winch. To
adjust the limit switch set points, refer to “INSTALLATION” section on page 4.
Press Roller (optional feature)
Ensure wire rope is positioned between press roller and drum barrel and springs keep
press roller in tight contact with wire rope.
Slack Wire Rope Detector (optional feature)
Contact factory for information.
INSPECTION
Inspection information is based in part on American National Standards Institute
Safety Codes A10.22 and American Standards of Mechanical Engineers Safety Codes
B30.7.
WARNING
• All new or repaired equipment should be inspected and tested by
Ingersoll Rand trained Service Technicians to ensure safe operation at rated
specifications before placing equipment in service.
• Never use a winch that inspection indicates is damaged.
Frequent and periodic inspections should be performed on equipment in regular
service. Frequent inspections are visual examinations performed by operators or
Ingersoll Rand
trained Inspectors and include observations made during routine
equipment operation. Periodic inspections are thorough inspections conducted by
Ingersoll Rand
trained Service Technicians. ASME B30.7 states inspection intervals
depend upon the nature of the critical components of the equipment and the severity
of usage. Refer to ‘Inspection Classifications’ chart and ‘Maintenance Intervals’ chart
in Product Maintenance Information Manual for recommended maintenance intervals.
Careful inspection on a regular basis will reveal potentially dangerous conditions
while still in the early stages, allowing corrective action to be taken before the
condition becomes dangerous.
Deficiencies revealed through inspection, or noted during operation, must be
reported to designated personnel to ensure corrective action is taken.
A determination as to whether a condition constitutes a safety hazard(s) must be
decided, and the correction of noted safety hazard(s) accomplished and documented
by written report before placing the equipment in service.
Records and Reports
Personnel Lifting System
Owners are responsible for establishing and implementing operation and safety
procedure training for all personnel involved in the use and operation of a Personnel
Lifting System.
1. PERSONNEL TRAINING. Records of training provided to supervisors, operators,
service personnel and personnel being transported should be maintained and
made available to designated personnel for review.
2. SYSTEM MAINTENANCE. Records of all service, maintenance and testing
performed on the Personnel Lifting System should be maintained and made
available to designated personnel for review.
Winch Records and Reports
Inspection records, listing all points requiring inspection, should be maintained for
all load bearing equipment. Written reports, based on
Initial
,
Weekly
and
Quarterly
inspections, should be made on the condition of critical parts as a method of
documenting inspections. These reports should be dated, signed by the person who
supervised the performance of the inspection, and kept on file where they are readily
available for review. A sample winch ‘Inspection and Maintenance Report’ has been
provided in the Product Maintenance Information Manual.
Wire Rope Reports
Records should be maintained as part of a long-range wire rope inspection program.
Records should include the condition of wire rope removed from service. Accurate
records will establish a relationship between visual observations noted during
frequent inspections and the actual condition of wire rope as determined by periodic
inspections.
Personnel Lifting System wire rope records should be maintained and made available
to designated personnel for review.
System Inspections and Tests
WARNING
• Information provided by Ingersoll Rand is applicable only to the winch to
assist in determining the condition of the winch components described.
References to other Personnel Lifting System components are made with respect
to their relationship to the winch. For specific information on system
components other than the winch, reference the manufacturer’s literature and
ANSI A10.22.
Personnel Lifting System inspections and tests of installed components, functions
and safety devices should be established based on procedures derived from ANSI
A10.22 specifications, OSHA regulations, manufacturer’s literature and
recommendations, system designer recommendations and all applicable local, state
and national standards.
1. SYSTEM. Frequency of inspections:
a.
Initial system inspection.
b.
Daily checks and Weekly inspections.
c.
Quarterly inspections.
System Initial and Quarterly Inspections
In addition to established Daily and Weekly inspections conduct the following:
NOTICE
• The static drop test is only required for guided cage systems.
1. INITIAL INSPECTION. With the cage
at rated load, on a guided cage system,
using dead weights, conduct a static drop test. This test is designed to ensure
the cage safety clamps engage and stop the cage from falling. Perform
requirements of the weekly inspection.
2. QUARTERLY INSPECTION. With the cage
empty, on a guided cage system,
conduct a static drop test. This test is designed to ensure the cage safety clamps
engage and stop the cage from falling. Perform requirements of the weekly
inspection.
System Testing
Personnel Lifting System testing should be conducted in accordance with the system
specific instructional manual and component manufacturer’s recommendations. A
system specific instruction manual must be compiled to conform to the requirements
of ANSI A10.22, and detail the operation, maintenance and safety requirements of
the various components comprising the personnel lifting system.
Winch Inspections
The following listed inspections apply only to the winch. These inspections should be
conducted when scheduled, when indicated by winch performance and when the
winch is disassembled for repair.
Careful inspection on a regular basis will reveal potentially dangerous conditions
while still in the early stages, allowing corrective action to be taken before the
condition becomes dangerous.
Damage revealed through inspection, or noted during operation, must be reported to
designated personnel instructed in safety, operation and maintenance of this
equipment. A determination as to whether a condition constitutes a safety hazard
must be made, and the correction of noted safety hazards accomplished and
documented by written report before placing the equipment in service.
Содержание FORCE5i FA5i-MRA
Страница 13: ...Form MHD56349 Edition 1 13 SERVICE NOTES...
Страница 14: ...14 Form MHD56349 Edition 1 SERVICE NOTES...
Страница 15: ...Form MHD56349 Edition 1 15 SERVICE NOTES...
Страница 16: ...www winchandhoistsolutions com...