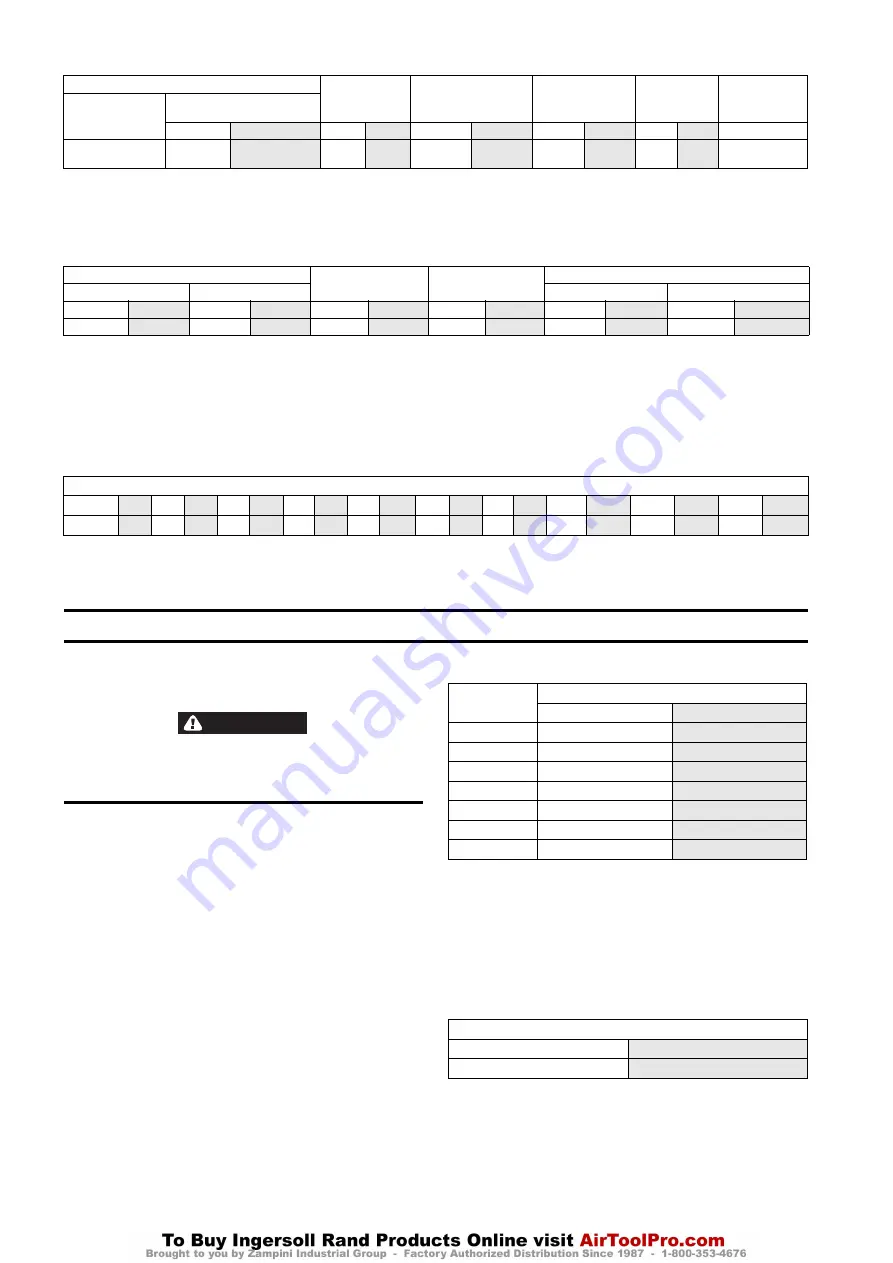
4
Form MHD56349 Edition 1
Table 2: Specifications
INSTALLATION
Prior to installing the winch, carefully inspect it for possible shipping damage.
Winches are supplied fully lubricated from the factory.
Check oil levels and adjust as necessary before operating winch. Refer to
“LUBRICATION” section for recommended oils and lubrication intervals.
CAUTION
• Owners and users are advised to examine specific, local or other regulations,
including American National Standards Institute and/or OSHA Regulations
which may apply to a particular type of use of this product before installing or
putting winch to use.
Mounting
Refer to Dwg. MHP0133 on page 11,
A.
Drum; Table 5 on page 4 and Table 6 on
page 4.
Care must be taken when moving, positioning or mounting the winch. In most cases,
lifting lugs have been provided to assist in handling the winch. If lug locations are
improper for your specific installation, great care should be taken to ensure that
winch, when lifted, will be properly balanced. Determine weight of winch by referring
to “SPECIFICATIONS” section. Add weight of wire rope and other installed options as
necessary. Lift winch 3 to 4 inches (75 to 100 mm) off ground. Verify winch is
balanced and secure before continuing lift. Mount winch so axis of drum is horizontal
and that motor vent cap is not more than 15° off top vertical center. If winch is to
be mounted in an inverted position, motor case must be rotated to position vent cap
to the top.
1. The winch mounting surface must be flat and of sufficient strength to handle
rated load plus weight of winch and attached equipment. An inadequate
foundation may cause distortion or twisting of winch uprights and side rails
resulting in winch damage.
2. Make sure mounting surface is flat to within 0.005 inch (0.127 mm) per inch of
drum length. Shim if necessary. Refer to Table 5 on page 4.
3. Mounting bolts must be Grade 8 or better. Use self-locking nuts or nuts with
lockwashers. Refer to Table 6, “Mounting Bolts,” on page 4.
4. Tighten 3/4 inch (18 mm) mounting bolts evenly and torque to 380 ft lbs (515
Nm) for dry thread fasteners. If fasteners are plated, lubricated or a thread
locking compound is used, torque to 280 ft lbs (380 Nm).
5. Maintain a fleet angle between sheave and winch of no more than 1-1/2°. The
lead sheave must be on a center line with drum and, for every inch (25 mm) of
drum length, be at least 1.6 feet (0.5 metre) from the drum. Refer to Product
Safety Information Manual.
6. Do not weld to any part of winch.
Air System
Air Motor Pipe
Inlet Size
Minimum Air System
Hose Size (inside
diameter)
Drum
Barrel Diameter
Drum Flange
Diameter
Sound Pressure
Level
Rated Operating
Pressure
Air Consumption
(at rated pressure and load)
scfm
cu.m/min
inch
mm
inch
mm
inch
mm
inch
mm
dBA
90 psig (630 kPs/6.3
bar)
700
20
1.25
32
1.5
38
15
381
27
686
89
Sound measurements have been made in accordance with ISO 11201, ISO 3744-3746 and ISO 4871 test specifications for sound from pneumatic equipment. Readings shown
are based on the average noise level of each winch configuration, proportionate to the utilized time in a regular cycle.
Lpc (Peak Sound Pressure) does not exceed 130 dB.
Performance based on 90 psig (6.3 bar/630 kPs) operating pressure.
Table 3: Rated Performance (at Rated Pressure/Volume)
Full Drum Lifting Capacity *
Stall Pull
Required Rope Size **
Drum Rope Storage Capacity ***
Personnel
Utility
Personnel
Utility
lbs
kgs
lbs
kgs
lbs
kg
in
mm
ft
m
ft
m
4,400
2,000
7,040
3,200
24,000
10,909
5/8
16
1,024
312
1,456
444
* Man Rider rating of 4,400 lbs (2,000 kg) is based on requirements of ANSI A10.22 [8:1 design factor with 5/8 inch (16 mm) wire rope]. Utility rating of 7,040 lbs (3,200 kg)
is based on requirements of ASME B30.7 [5:1 design factor with 5/8 inch (16 mm) wire rope].
** Rope construction: Only 6 x 19, 6 x 37 classification, or rotation-resistance ropes, all with IWRC, shall be used.
*** Man Rider wire rope storage is based on a winch with a 24 inch (610 mm) diameter drum flange and on ANSI A10.22 standards which require the top layer to be at least
2 inches (51 mm) below the drum flange diameter. Utility wire rope storage is based on a winch with a 19 inch (483 mm) diameter drum flange and on ASME/ANSI B30.7
standards which require the top layer to be at least 1/2 inch (13 mm) below the drum flange diameter.
Refer to sales literature for winch drum wire rope storage capacities on other drum lengths.
Table 4: Available Drum Lengths
Drum Lengths
in
mm
in
mm
in
mm
in
mm
in
mm
in
mm
in
mm
in
mm
in
mm
in
mm
---
---
12
305
16
406
20
508
24*
610*
30
762
36
915
40**
1016**
42**
1067**
50**
1270**
* Standard Length
** Special, contact factory
Table 5: Mounting Surface Tolerance
Drum
Length
Mounting Surface Minimum Flatness
inch
mm
8
0.04
1.02
12
0.06
1.52
16
0.08
2.03
20
0.10
2.54
24
0.12
3.05
30
0.15
3.81
36
0.18
4.57
Table 6: Mounting Bolts
Mounting Bolts
inch
mm
3/4
18
Содержание FORCE5i FA5i-MRA
Страница 13: ...Form MHD56349 Edition 1 13 SERVICE NOTES...
Страница 14: ...14 Form MHD56349 Edition 1 SERVICE NOTES...
Страница 15: ...Form MHD56349 Edition 1 15 SERVICE NOTES...
Страница 16: ...www winchandhoistsolutions com...