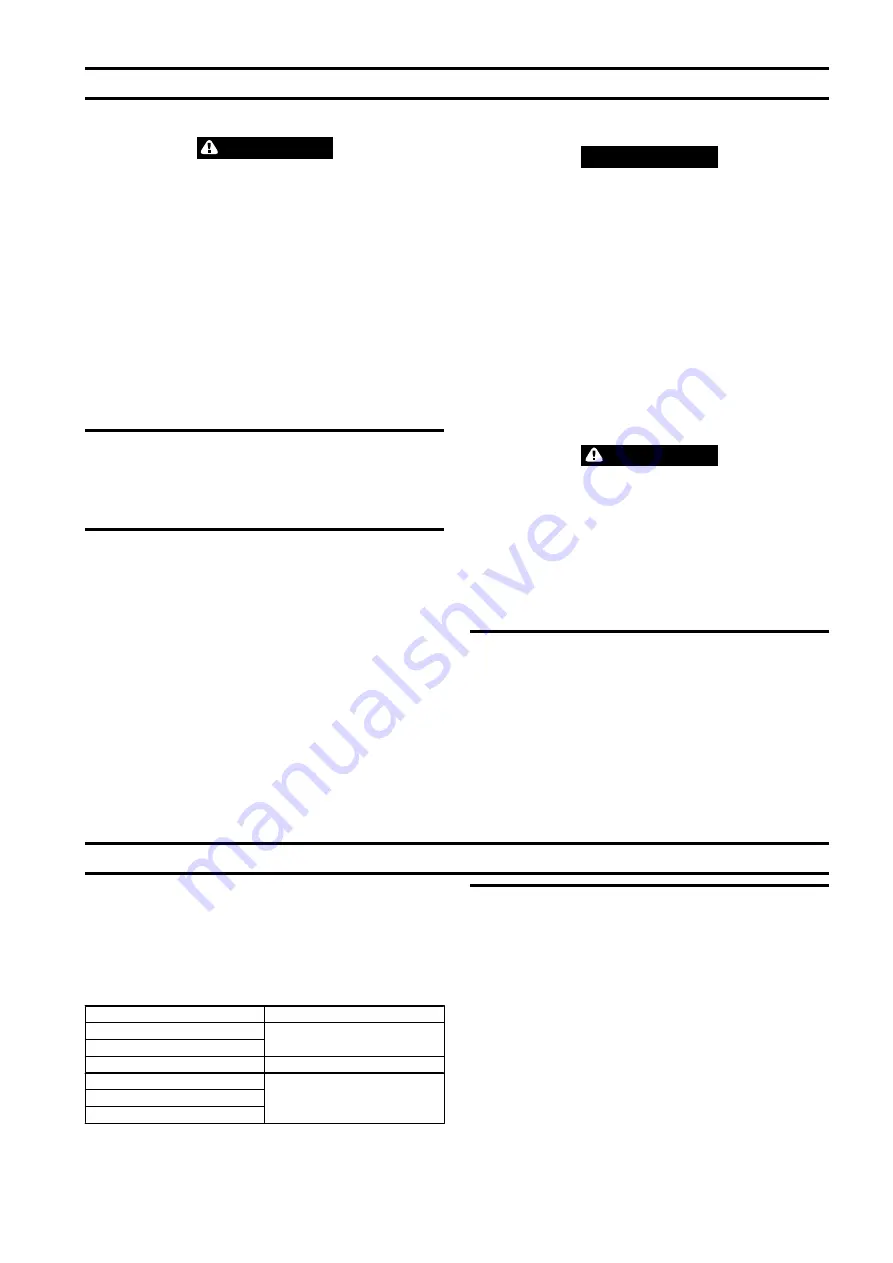
INSPECTION
Inspection information is based in part on American Society of Mechanical Engineers
Safety Codes (ASME B30.7).
WARNING
•
All new or repaired equipment should be inspected and tested by
Ingersoll Rand trained Service Technicians to ensure safe operation at rated
specifications before placing equipment in service.
•
Never use a winch that inspection indicates is damaged.
Frequent and periodic inspections should be performed on equipment in regular
service. Frequent inspections are visual examinations performed by operators or
Ingersoll Rand trained Inspectors and include observations made during routine
equipment operation. Periodic inspections are thorough inspections conducted by
Ingersoll Rand trained Service Technicians. ASME B30.7 states inspection intervals
depend upon the nature of the critical components of the equipment and the
severity of usage. Refer to “Inspection Classifications” chart and “Maintenance
Intervals” chart in Product Maintenance Information Manual for recommended
maintenance intervals.
Careful inspection on a regular basis will reveal potentially dangerous conditions
while still in the early stages, allowing corrective action to be taken before the
condition becomes dangerous.
Deficiencies revealed through inspection, or noted during operation, must be
reported to designated personnel to ensure corrective action is taken.
A determination as to whether a condition constitutes a safety hazard(s) must be
decided, and the correction of noted safety hazard(s) accomplished and
documented by written report before placing the equipment in service.
n
Wire Rope Reports
Records should be maintained as part of a long-term wire rope inspection program.
Records should include the condition of wire rope removed from service. Accurate
records will establish a relationship between visual observations noted during
frequent inspections and the actual condition of wire rope as determined by periodic
inspections.
n
Frequent Inspection
On equipment in regular service, frequent inspections should be made by operators
at the beginning of each shift. In addition, visual and audible inspections should be
conducted during regular operation for indications of damage or evidence of
malfunction (such as abnormal noises).
Disassembly may be required as a result of frequent inspection findings or in order
to properly inspect the individual components. Disassembly steps are described in
the Product Maintenance Information Manual.
1.
Surrounding Area. Visually check for winch oil leaks. Do not operate winch if
leaking oil is found. Ensure surrounding area has no slippery surfaces and is
obstruction free.
2.
Hoses and Fittings. Visually inspect for damage, air leaks and loose connections.
Repair all leaks or damage and tighten loose connections prior to starting daily
tasks.
3.
Muffler. Visually check for restrictions or external damage. Clear restrictions or
replace if damaged.
4.
Manual Shut-Off Valve. Test shut-off valve to ensure proper operation and free
movement.
5.
Guards. Verify wire rope does not contact guard during winch operation and
that guards are secure and undamaged.
6.
Winch. Visually inspect winch housings, control(s), external brake, side rails and
drum for damage. Check that all external bolts are in place and secure. Report
damage to supervisor and request additional inspection by an Ingersoll Rand
trained Service Technician.
7.
Winch Operation. Power winch in both directions. Winch must operate
smoothly without sticking, binding or abnormal noises and have minimal
vibration.
NOTICE
•
The full extent of wire rope wear cannot be determined by visual inspection.
At any indication of wear inspect wire rope in accordance with instructions
in “Periodic Inspection.” Refer to Product Maintenance Information
Manual.
8.
Pendant (optional feature). Ensure operation of pendant levers is smooth and
winch is responsive to pendant control. Pendant levers must spring return to
the neutral position when released.
9.
Manual Throttle Lever. Ensure operation of manual throttle lever is smooth
and winch is responsive to lever movement. Lever must return to neutral and
lock in place when released. If winch responds slowly or controls stick, do not
operate winch until all problems have been corrected.
10.
Wire Rope. Visually inspect all wire rope expected to be in use during the day’s
operations. Inspect for wear and damage indicated by distortion of wire rope
such as kinking, “birdcaging,” core protrusion, main strand displacement,
corrosion, broken or cut strands. If damage is evident, do not operate winch until
the discrepancies have been reviewed and inspected further by personnel
knowledgeable on wire rope safety and maintenance procedures.
11.
Wire Rope Spooling. Visually check reeving and ensure wire rope feeds on and
off the drum smoothly. Verify spooling direction (overwind or underwind) is
correct for winch and application.
12.
Brake(s). Lift and lower the load a short distance to test brake(s). Brake(s) must
hold load without slipping. Automatic brake must release when winch control
throttle is operated. If brake(s) do not hold load or do not release properly, they
must be adjusted or repaired.
WARNING
•
Worn or improperly functioning brakes may cause excessive heat buildup
and sparks.
13.
Lubrication. Refer to “LUBRICATION” on page 9 for recommended
procedures and lubricants.
14.
Limit Switches (standard on all CE winch models). Ensure limit switches engage
and prevent operation at the required set point and with drum rotating in correct
direction. Ensure limit switch properly resets.
15.
Emergency Stop (standard on all CE winch models). Run winch and activate
emergency stop. Winch operation must stop quickly. Ensure valve resets
properly.
16.
Labels and Tags: check for presence and legibility of labels. Refer to Product
Parts Information Manual for correct labels and placement. Replace if damaged
or missing.
n
Storing the Winch
1. Always store the winch in a no load condition.
2. Wipe off all dirt and water.
3. To prevent rust buildup from internal condensation, open lubricator to allow
more oil into winch and operate with no load. If winch is being stored from air
source place small amount of 20 weight oil at air inlet port.
4. Oil the wire rope.
5. Place in a dry location.
6. Before returning winch to service, follow instructions for ‘Winches Not In Regular
Use’ in the “INSPECTION” section on page 9.
7.
Mufflers and Breathers. All mufflers and breathers must be removed and
replaced with threaded plugs to prevent dust and moisture from entering motor
and valve assemblies.
8.
Drum Brake. Product equipped with a manual band brake must be stored with
the brake in its disengaged position.
LUBRICATION
To ensure continued satisfactory operation of winch, all points requiring lubrication
must be serviced with correct lubricant at proper time interval as indicated for each
assembly.
Refer to ‘Maintenance Interval’ chart in Product Maintenance Information Manual
for recommended lubrication intervals. Use only those lubricants recommended.
Other lubricants may affect product performance. Approval for use of other
lubricants must be obtained from your Ingersoll Rand distributor. Failure to observe
this precaution may result in damage to winch and/or its associated components.
Table 9: Lubrication Intervals
Component
Interval
Check Air Line Lubricator
Daily
Check Motor Oil Level
Check Reduction and Disc Brake Oil
3 Months
Change Motor Oil
1 Year or 1,000 Hours
of Product Operation
Change Gearbox Oil
Change Disc Brake Oil
n
General Lubrication
Correct lubrication is one of the most important factors in maintaining efficient
product operation.
1. The recommended grade of oil must be used at all times. Use of unsuitable oil
may result in excessive temperature rise, loss of efficiency and possible damage
to lubricated components. Refer to ‘Recommended Lubricants’ section
2. It is recommend that the first oil change be done after approximately 50 hours
of initial operation. Thereafter, drain and replace oil according to Table 9
‘Lubrication Intervals’ on page 9.
3. Always inspect removed oil for evidence of internal damage or contamination
(metal shavings, dirt, water, etc.). If indications of damage are noted, investigate
and correct before returning winch to service.
4. After product operation, allow oil to settle before topping off.
5. Always collect lubricants in suitable containers and dispose of in an
environmentally safe manner.
Form MHD56437 Edition 7
9