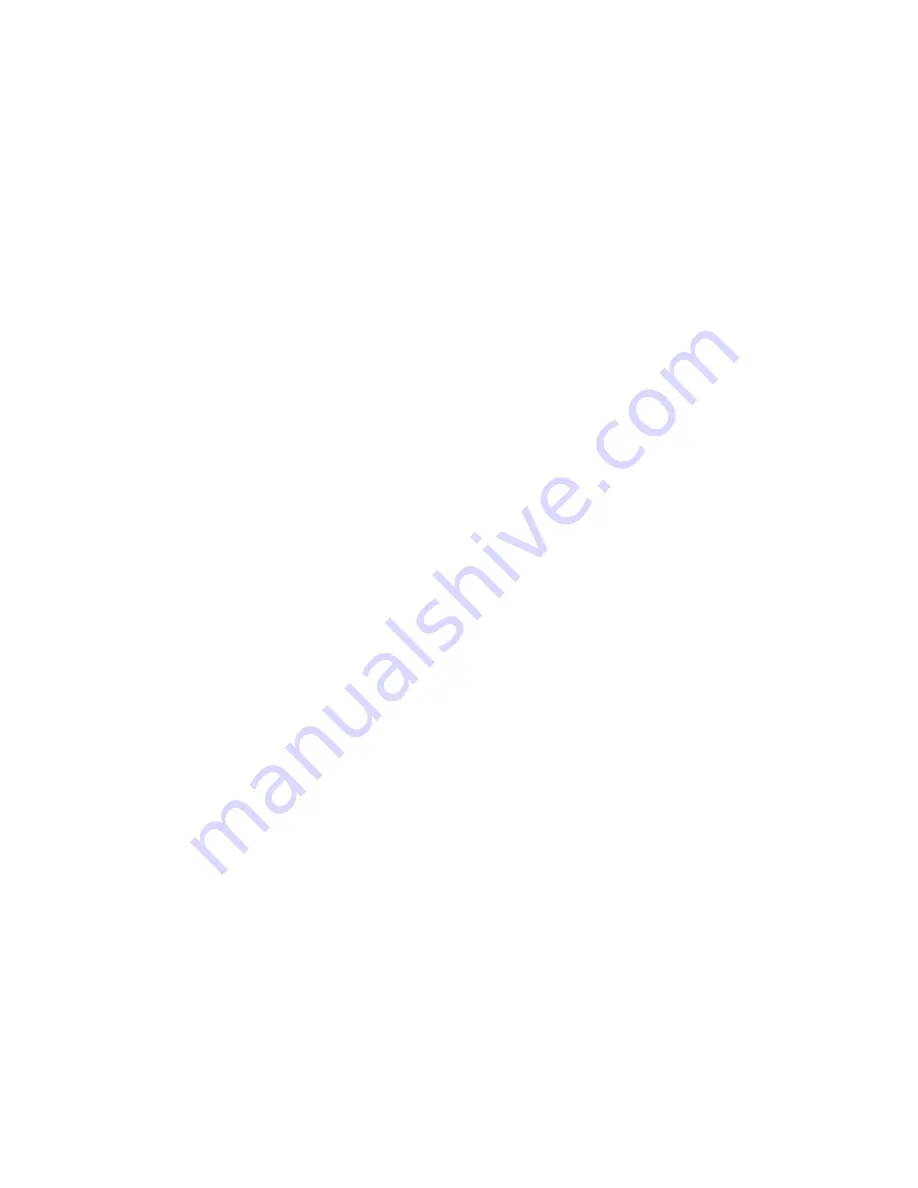
1.0 RECEIPT OF EQUIPMENT
1.1 INSPECTION
When you receive the compressor please inspect it
closely. Any indication of careless handling by the car-
rier should be noted on the delivery receipt especially
if the compressor will not be immediately un-crated.
Obtaining the delivery man’s signed agreement to any
noted damages will facilitate any future insurance
claims.
1.2 UNPACKING AND HANDLING
The compressor package has been mounted on a
wooden shipping base which will allow fork lifting
under the compressor base to facilitate handling dur-
ing shipment. Care in positioning the forklift is impor-
tant because the location of the center of gravity is
strongly affected by the location of the airend and
drive motor.
The wooden base must be removed prior to installa-
tion.
2.0 INSTALLATION
2.1 VENTILATION
Air cooled air compressors produce large amounts of
heat. Because of this large heat production, the com-
pressor must be placed in a room with adequate venti-
lation.
If heated air from the compressor exhaust is allowed
to re-circulate back to the compressor, the compressor
will overheat and shut down. This heat must be
exhausted from the room. You should take this into
consideration when deciding where to place the com-
pressor within the building. Sufficient clearance must
be allowed around the compressor to perform the
required maintenance.
Ambient temperatures higher than 115°F (46°C)
should be avoided as well as areas of high humidi-
ty.
External ducting, to and from the compressor, that
is installed in the field must be sized so that no
excessive back pressure is exerted on the fan.
Maximum allowable is 0.25 inches (6.4mm) of
water column air resistance total for inlet and
exhaust ducting.
Also consider the environment near the compres-
sor.
DUST, CHEMICALS, METAL FILINGS, PAINT
FUMES, and OVERSPRAY should be avoided as well
as any other conditions which might be detrimental to
the proper operation of the compressor.
2.2 FOUNDATION REQUIREMENTS
The compressor can be installed on any level floor that
is capable of supporting the weight.
When sound transmission is of particular importance, it
is often helpful to install a sheet of rubber-fabric-mat-
ting, under the compressor baseplate or receiver tank
feet to reduce the possibility of resonant sounds being
transmitted or amplified through the floor.
2.3 OUTDOOR INSTALLATIONS
When a compressor must be installed outside, there
are certain items that should be incorporated into the
installation to help assure trouble free operation.
These items have been listed below plus Figure 2.31
has been included to show a typical outdoor protected
installation. The unit must be purchased with
NEMA 4 option to provide watertight electric’s.
• The compressor should be on a concrete pad
designed to drain water away. If the concrete pad is
sloped, then the compressor must be leveled.
• The roof of the shelter should overhang the compres-
sor a minimum of 4 feet (1.2m) on all sides to prevent
direct rain and snow from falling on the unit.
• The unit must be arranged under the shelter in a way
that prevents air recirculation (i.e. hot exhaust back to
the package inlet).
• If the installation includes more than one compressor,
the hot air exhaust should not be directed towards the
fresh air intake of the second unit or an Air Dryer.
• If a standard machine is to be installed outside, the
ambient temperature must never drop below 35°F
(2°C) or freezing of condensate will result.
• Power disconnect switch must be within the com-
pressor operator’s line of sight and should be in close
proximity to the unit.
• Condensate drains must never be allowed to dump
on the ground. Pipe to a suitable sump for future col-
lection, disposal or separation of lubricant and water
mixture.
• Incoming power connections must use suitable con-
nectors for outdoor weather tight service.
• Sufficient clearance must be allowed on all four sides
of the unit for service access. If possible, access by a
fork lift and/or an overhead beam hoist should be kept
in mind (for eventual service to airend or motor).
8
Содержание EP 20-ESP
Страница 35: ...33 6 0 REFERENCE DRAWINGS 6 1 ELECTRICAL SCHEMATIC FULL VOLTAGE 39884143 REV 01...
Страница 36: ...34 6 2 ELECTRICAL SCHEMATIC STAR DELTA 39884150 REV 01...
Страница 38: ...36 6 4 FOUNDATION PLAN TANK MOUNTED CONTINUED 39871975 REV 03...
Страница 39: ...37 6 4 FOUNDATION PLAN TANK MOUNTED 39871975 REV 03...
Страница 40: ...38 6 5 FOUNDATION PLAN BASE MOUNTED CONTINUED 39872835 REV 03...
Страница 41: ...39 6 5 FOUNDATION PLAN BASE MOUNTED 39872835 REV 03...
Страница 44: ...42 39876461 REV 02...
Страница 46: ...44 39880844 REV 01...
Страница 48: ...46 39872031 REV 01 SEE PIPING ASSEMBLY OPTIONS...
Страница 52: ...50 39872023 REV 02 TO AFTERCOOLER TO AFTERCOOLER...
Страница 57: ...55 DATE RUN TIME WORK DONE QTY UNIT WORK HOURS MEASURE BY 8 0 MAINTENANCE RECORD...
Страница 58: ...56 DATE RUN TIME WORK DONE QTY UNIT WORK HOURS MEASURE BY MAINTENANCE RECORD...