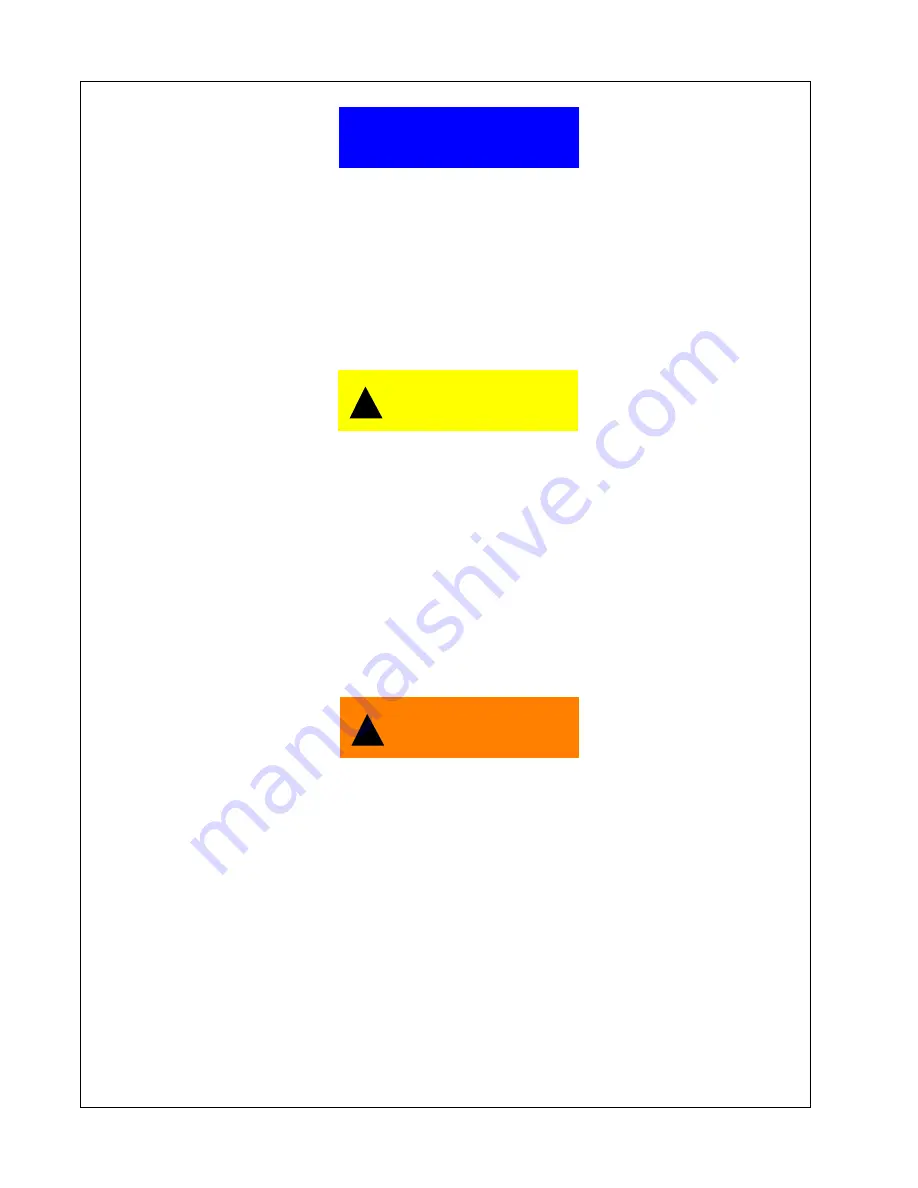
Operation & Maintenance Manual
Maintenance
62
Book 22826226
NOTICE
Installing a new oil filter element when the old gasket remains on the filter
head, will cause an oil leak and can cause property damage.
Reassembly
Clean the filter gasket contact area and install the new element.Tighten until the gasket makes
contact with the filter housing. Tighten an additional 1/2 to 3/4 of a revolution.
CAUTION
!
Start the machine (refer to PRIOR TO STARTING and STARTING THE
MACHINE in the OPERATING INSTRUCTIONS section of this manual) and
check for leakage before the machine is put back into service.
COMPRESSOR OIL SEPARATOR ELEMENT
Refer to the MAINTENANCE CHART in this section for the recommended servicing intervals.
If, however, the element has to be replaced, then proceed as follows:
Removal
WARNING
!
Do not remove the filter(s) without first making sure that the machine is
stopped and the system has been completely relieved of all air pressure.
(Refer to STOPPING THE MACHINE in the OPERATING INSTRUCTIONS
section of this manual).
Disconnect all hoses and tubes from the separator tank cover plate. Remove the drop-tube
from the separator tank cover plate and then remove the cover plate. Remove the separator
element.
lnspection
Examine the filter element. Examine all hoses and tubes, and replace if necessary.
Содержание Doosan HP675WCU-T3
Страница 2: ...2...
Страница 6: ...6 Always use Ingersoll Rand Replacement parts...
Страница 7: ...Book 22826226 7 Foreword...
Страница 10: ...Operation Maintenance Manual Foreword 10 Book22826226 Always use Ingersoll Rand Replacement Parts...
Страница 11: ...Book 22826226 11 Safety...
Страница 17: ...Safety Operation Maintenance Manual Book 22826226 17 Decals Graphic Form and Meaning of ISO Symbols...
Страница 18: ...Operation Maintenance Manual Safety 18 Book22826226...
Страница 19: ...Safety Operation Maintenance Manual Book 22826226 19...
Страница 20: ...Operation Maintenance Manual Safety 20 Book22826226...
Страница 22: ...Operation Maintenance Manual Safety 22 Book22826226...
Страница 23: ...Safety Operation Maintenance Manual Book 22826226 23...
Страница 24: ...24 Book22826226...
Страница 26: ...Operation Maintenance Manual Safety 26 Book22826226...
Страница 27: ...Book 22826226 25 Noise Emission...
Страница 33: ...Book 22826226 31 General Data...
Страница 36: ...34 Book22826226 Always use Ingersoll Rand Replacement parts...
Страница 37: ...Book 22826226 35 Operating Instructions...
Страница 56: ...Operation Maintenance Manual Operating Instructions 54 Book22826226 Always use Ingersoll Rand Replacement Parts...
Страница 57: ...Book 22826226 55 Maintenance...
Страница 72: ...Operation Maintenance Manual Maintenance 70 Book22826226 Torque Values...
Страница 73: ...Maintenance Operation Maintenance Manual Book 22826226 71...
Страница 74: ...Operation Maintenance Manual Maintenance 72 Book22826226 Always use Ingersoll Rand Replacement parts...
Страница 75: ...Book 22826226 73 Lubrication...
Страница 78: ...76 Book22826226 Always use Ingersoll Rand Replacement parts...
Страница 79: ...Book 22826226 81 Fault Finding...
Страница 84: ...Always use Ingersoll Rand Replacement parts 86 Book22826226 Always use Ingersoll Rand Replacement parts...
Страница 85: ...Book 22826226 87 Machine Systems...
Страница 89: ...Book 22826226 93 Electrical...
Страница 93: ...Book 22826226 97 Options...
Страница 98: ...102 22826226 Always use Ingersoll Rand Replacement parts...