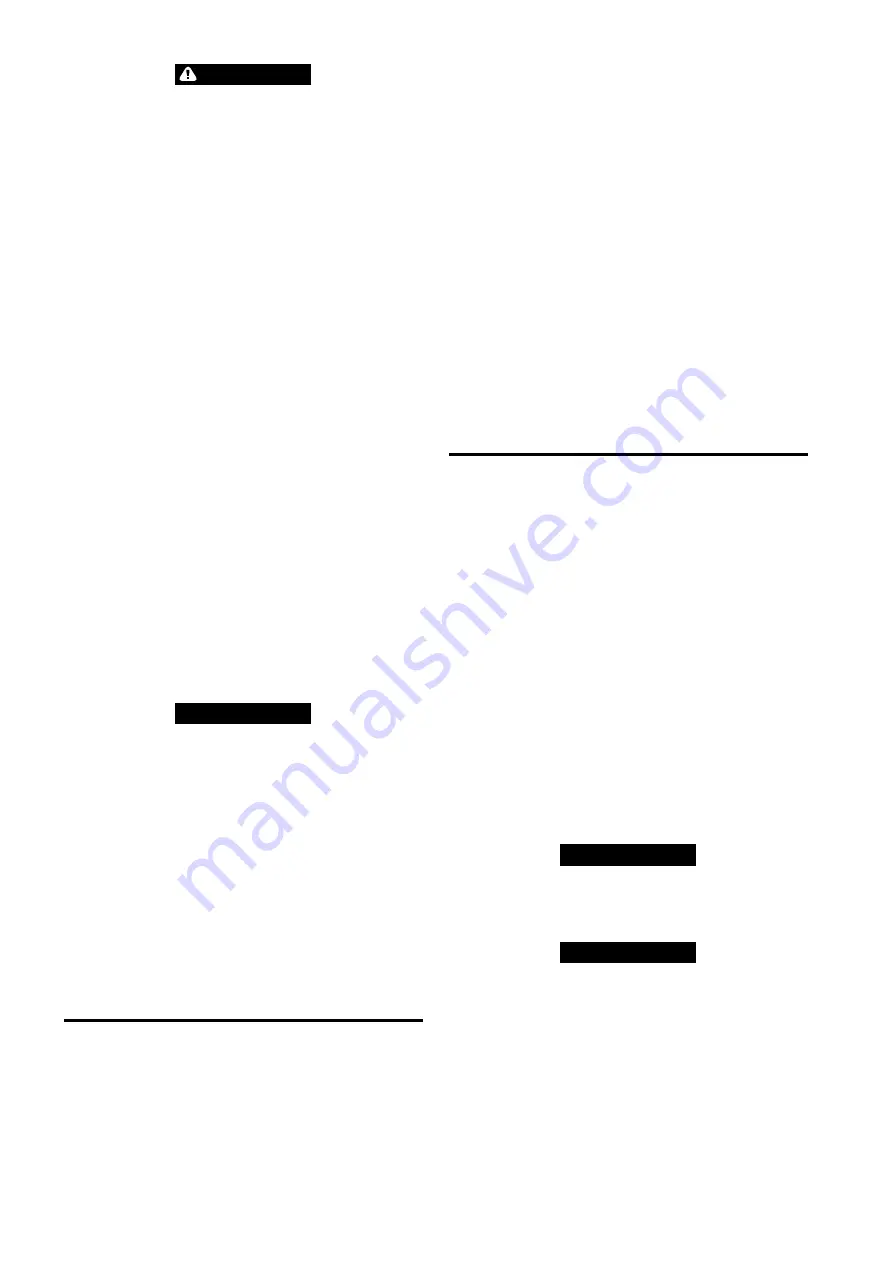
CAUTION
•
Press reverse valve bushing out from inside motor housing only. Bushing
has a groove to clear bushing key (30).
•
Support motor housing to prevent damage during pressing.
n
Gear Case Disassembly
Refer to Dwg. MHP1207.
1. Remove lower grease plug (75) from gear case cover (76). Tip winch on its side
and drain grease.
2. Unscrew eccentric shaft bushing setscrew (77) with No. 201 setscrew wrench,
and by pulling on clutch lever (54) remove assembled eccentric shaft bushing
(49) from gear case cover.
3. Unscrew seven gear case cover capscrews (5) and remove cover (76) from gear
case (66).
4. Grasp intermediate gear (70) and drive gear (99) and withdraw them
simultaneously from gear case. The complete drive shaft assembly will come out
with the gear.
5. Support clutch jaw (101) and press drive shaft (93) out of outer bearing (72),
freeing clutch jaw, clutch jaw lock balls (95) and clutch jaw lock spring (94). Care
should be taken so that these latter parts, which are small, will not be lost.
6. With two small screw drivers, spread gap in retainer ring (98) and remove it from
groove in drive shaft.
7. Slide washer (97) and drive gear (99) from drive shaft.
8. Drive shaft bearing, inner (96) should be removed only if replacement is
necessary. If necessary, support bearing and press shaft from its inner ring.
n
Shuttle Valve Chest Disassembly (optional feature)
Refer to Dwg. MHP1209.
1. Remove capscrews (221) and (222) and lockwashers (223) from shuttle valve
chest (200). Separate the shuttle valve chest from motor housing (28).
2. Remove gasket (217) from shuttle valve chest.
3. Remove thrust washer (13) from shuttle valve chest.
4. Remove pipe plugs (205) and (207) and fittings (225) and (236) from shuttle valve
chest (200).
5. Unscrew brake valve caps (210) and remove brake valve cap gaskets (211) from
both sides of the shuttle valve chest.
6. Unscrew brake valve seats (209) from shuttle valve chest and remove the brake
valve (208) from the brake valve bushing (202).
7. Unscrew shuttle valve caps (213) and remove brake valve cap gaskets (214) from
both sides of the shuttle valve chest.
8. Remove shuttle valve springs (216) and shuttle valve washers (215).
9. Remove shuttle valve (212).
10. Do not remove shuttle valve bushing (203) or brake valve bushing (202) unless
replacement is necessary.
n
Wire Rope Drum Removal
Refer to Dwg. MHP1207.
1. Unscrew and remove from bottom of base (87), four base capscrews (69) and
lockwashers (71) that retain motor mounting bracket (79). Use No. 331 base
capscrew wrench.
2. Pull complete motor and wire rope drum assembly as one unit away from gear
end of winch, sliding it along the base until the crank assembly is clear.
3. Lift off brake band (61) and assembled parts.
4. Slide wire rope drum (86) from drum shaft (62).
NOTICE
•
The two drum bearings (84), one located at each end of the drum, and the
motor pinion bearing (63) located in the drum shaft are needle type
bearings that are usually destroyed by removal. Therefore, they should be
removed only if replacement is to be made. Likewise, grease seals are
usually destroyed if removed, so the drum grease seal (82), located in the
motor end of the drum, should not be removed except for replacement.
5. If replacement of either drum bearing is necessary, stand drum on end, with
bearing to be removed at the bottom. Using a long punch or rod that is small
enough to pass through the upper bearing at a sufficient angle to contact shell
of the lower bearing, drive bearing out.
6. If replacement of motor pinion bearing (63) is necessary, unscrew the two drum
shaft setscrews (77) and remove drum shaft (62) from motor mount bracket (79).
Using a small, sharp chisel, collapse bearing and withdraw it from shaft.
n
Two Function Pendant Disassembly (optional feature)
Refer to Dwg. MHP2346.
1. Remove fittings (348) and lifting eye (440).
2. Unscrew plugs (444). Remove springs (445) and balls (446).
3. Tap out pin (447) and remove levers (453).
4. Remove setscrew (455) from pendant handle (454).
5. Remove valve assemblies (452). Remove ‘O’ rings (443) and (449) and protectors
(451). Discard ‘O’ rings.
6. Remove plug (470) or emergency stop valve (441) from pendant handle.
7. Remove retainer ring (458) and exhaust washer (457).
n
Cleaning, Inspection and Repair
n
Cleaning
Clean all winch component parts in solvent (except the drum brake band). The use
of a stiff bristle brush will facilitate the removal of accumulated dirt and sediments
on the housing, frame and drum. If bushings have been removed, it may be necessary
to carefully clean out old Loctite™ from the bushing bores. Dry each part using low
pressure, filtered compressed air. Clean the drum brake band using a wire brush or
emery cloth. Do not wash the drum brake band in liquid. If the drum brake band
lining is oil-soaked, it must be replaced.
n
Inspection
All disassembled parts should be inspected to determine their fitness for continued
use. Pay particular attention to the following:
1. Inspect all gears for worn, cracked, or broken teeth.
2. Inspect all bushings for wear, scoring, or galling.
3. Inspect shafts for ridges caused by wear. If ridges caused by wear are apparent
on shafts, replace shaft. Inspect all surfaces on which oil seal lips seat.
4. Inspect all threaded items and replace any with damaged threads.
5. Inspect band brake lining for oil, grease and glazing. If band brake lining is oil-
soaked, replace the brake band. Remove glazed areas of band brake lining by
sanding lightly with a fine grit emery cloth.
6. Measure thickness of drum brake band and lining. If drum brake band and lining
together measure less than 0.203 inches (5.2 mm) thick anywhere along the
edges, replace brake band (61).
7. Inspect all bearings for play, distorted races, pitting and roller or ball wear or
damage. Inspect bearings for freedom of rotation.
n
Repair
Actual repairs are limited to removal of small burrs and other minor surface
imperfections from gears and shafts. Use a fine stone or emery cloth for this work.
Do not use steel wool.
1. Worn or damaged parts must be replaced. Refer to the applicable parts list in
the Product Parts Information Manual for specific replacement parts
information.
2. Inspect all remaining parts for evidence of damage. Replace or repair any part
which is in questionable condition. Cost of the part is often minor in comparison
with cost of redoing job.
3. Smooth out all nicks, burrs, or galled spots on shafts, bores, pins, or bushings.
4. Examine all gear teeth carefully, and remove nicks or burrs.
5. Polish edges of all shaft shoulders to remove small nicks which may have been
caused during handling.
6. Remove all nicks and burrs caused by lockwashers.
7. Replace all gaskets, oil seals, and ‘O’ rings removed during product disassembly.
n
Assembly
n
General Instructions
•
Use all new gaskets and seals.
•
Replace worn parts.
•
Assemble parts using matchmarks attached during disassembly. Compare
replacement parts with originals to identify installation alignments.
•
Lubricate all internal parts with rust and oxidation inhibiting lubricant, ISO
VG 100 (SAE 30W).
•
Apply a light coat of Loctite® 243 to all threaded components prior to
assembly, unless otherwise specified.
n
Motor Assembly
Refer to Dwg. MHP1207.
1. Place motor case (28) on a flat table with open side facing up.
2. Clean bushing bore in motor housing with Loctite® 790 cleaner. Ensure that
entire bore is clean then dry using low pressure, filtered compressed air.
3. Apply a thin even coat of Loctite® 609 to entire outside surface of new rotary
valve bushing (14).
4. Using a swab, apply a thin even coat of Loctite® 609 to entire inner bore of motor
housing.
5. Align keyway in rotary valve bushing with bushing key in bore of motor case.
Start bushing squarely in bore and gently press it (by hand) flush with the top
face of the case. Once bushing has been installed allow Loctite® to cure for 10
minutes. Full cure requires 24 hours.
6. Clean reverse valve bushing bore in motor housing with Loctite® 790 cleaner.
Ensure that entire bore is clean then dry using low pressure, filtered compressed
air.
7. Apply a thin even coat of Loctite® 609 to entire outside surface of new reverse
valve bushing (12).
8. Using a swab, apply a thin even coat of Loctite® 609 to entire inner bore of motor
housing.
NOTICE
•
Applying Loctite® 609 to both surfaces is necessary to ensure an airtight
seal between rotary valve bushing and motor housing.
9. Align groove in reverse valve bushing (12) with bushing key (30) in motor
housing. Press rotary valve bushing into motor housing until reverse valve
bushing is flush with motor housing.
NOTICE
•
Earlier BU7A winches contain a reverse valve bushing with the keyway
running the entire length of bushing making it difficult to determine which
end of the bushing should be installed first. On these winches, always start
bushing into case, external beveled end first. The bevel in bore of bushing
will then be toward valve chest cover.
10. Check fit of rotary valve (15) in bushing. It must be a good running fit. Lap if
necessary using a mild, fine grain, lapping compound. If bushing has closed in
sufficiently to make lapping impossible, ream to 1.000 in. (25.4 mm) diameter.
11. Check fit of the reverse valve (10) in its bushing. If it is tight, ream bushing to
1.000 in. (25.4 mm) diameter.
12. Place oil wall (33) in motor case and retain with four oil wall screws (35).
13. Support inner ring of shielded side of crank bearing (78) and press crank (44)
into bearing until shoulder on crank contacts inner ring. Ensure crank bearing
(78) is installed with unshielded side nearest the flanged end of crank (44).
14. Place motor case assembly on bench with open side up and inlet bushing (20)
to the left.
15. Lubricate rotary valve bushing (14) and rotary valve (15).
8
Form MHD56461 Edition 2
Содержание BU7A
Страница 12: ...R www ingersollrandproducts com...