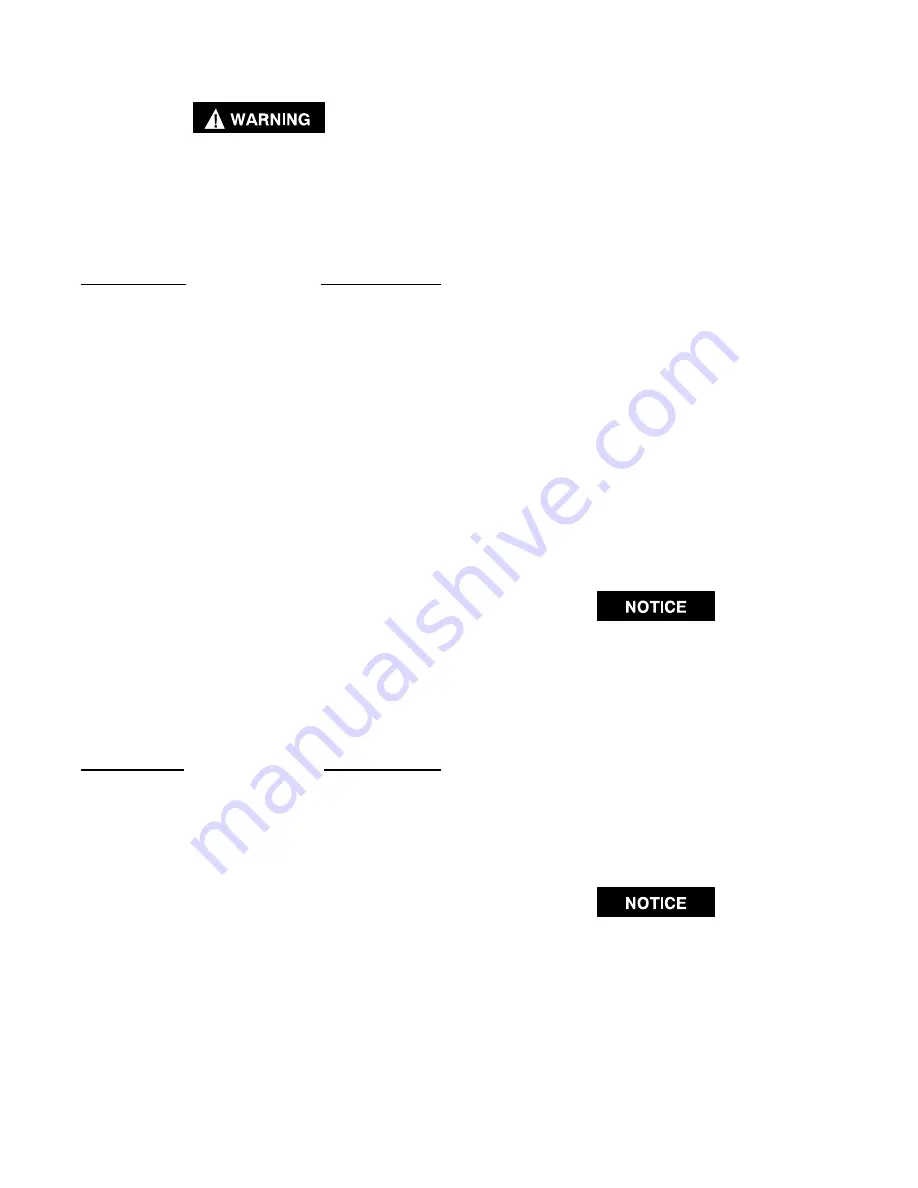
14
MAINTENANCE SECTION
Always turn off the air supply and disconnect the air
supply hose before installing, removing or adjusting
any accessory on this tool or before performing any
maintenance on this tool. Failure to do so could result
in injury.
General Instructions
LUBRICATION
Each time a Model 2934B2SP, 2934B9SP or 2940B2SP
Impactool is disassembled for maintenance and repair or
replacement of parts, lubricate the tool as follows:
1.
Work approximately 12 to 15 cc of Ingersoll–Rand
No. 100 Grease into the impact mechanism. Coat the
Anvil (49) lightly with grease. Also, coat the inside of
the Hammer Case Bushing (40) with grease. Inject
approximately 2 to 4 cc of grease into the Grease
Fitting (2).
2.
Use Ingersoll–Rand No. 50 Oil for lubricating the
motor. Inject approximately 1 to 2 cc of oil into the
Straight Inlet (11) before attaching the air hose.
Remove the Oil Chamber Plug (14) and fill the oil
chamber. To avoid repeated filling of the built–in
lubricator, we recommend installing a larger capacity
air line lubricator as close to the tool as practical.
Where the lubricator cannot be permanently mounted,
we recommend using an Ingersoll–Rand No. 3LUB8
Lubricator. For permanent installation, we
recommend using an lngersoll–Rand C22–04–G00
Filter–Lubricator–Regulator Unit. These units have
1/2” inlet and outlet. The 3LUB8 has 1/6 pt (79 mL)
capacity; the C22–04–G00 has 1/2 pt (237 mL)
capacity. Larger capacity units may be used, but do
not use a unit having less than 1/2” inlet and outlet.
DISASSEMBLY
1.
Always disconnect the air supply line before
performing any maintenance on this tool.
2.
Always use protective eyewear when performing
maintenance on a tool or when operating a tool.
3.
Do not disassemble a tool any further than necessary
to replace or repair damaged parts.
4.
Do not disassemble the Impactool unless you have a
complete set of new gaskets and O–rings for
replacement.
5.
Do not remove any part which is a press fit in or on
an assembly unless the removal of that part is
necessary for repair or replacement.
6.
Whenever grasping a tool or part in a vise, always use
copper–covered or leather–covered vise jaws to
protect the surface of the part and help prevent
distortion. this is particularly true of threaded
members and housings.
Disassembly of the Impact Mechanism
1.
Grasp tool in copper–covered or leather–covered vise
jaws with square drive upward.
2
.
Using a hex wrench, unscrew and remove two
Deflector Screws (33). Remove Exhaust Deflector
(29) and Exhaust Gasket (32) and, if necessary, pull
Exhaust Baffle (31) and Exhaust Silencer (30) from
Deflector.
3.
Using a hex wrench, unscrew and remove four
Hammer Case Cap Screws (42) and Lock Washers
(43). Remove Dead Handle Bracket (51) and two
Bracket Spacers (52).
4.
While lightly tapping on the end of Anvil (49) with
plastic hammer, lift off hammer Case (39).
5.
Remove Hammer Case Gasket (41).
6.
Remove Anvil by rotating it as it is lifted out of the
assembly.
7.
Lift remaining hammer assembly off rotor shaft.
8.
Push two Hammer Pins (47) out of Hammer Frame
Assembly (46) and slide two Hammers (48) out of the
Frame.
Disassembly of the Reverse Valve
1.
Lightly clamp Motor Housing Assembly (25) in
copper–covered or leather–covered vise jaws with
Trigger Handle Assebly (1) upward.
Excessive clamping pressure will distort the Motor
housing and make motor removal extremely
difficult. Do not insert the hammer case end of the
motor housing more than 1” (25 mm) into the vise
jaws.
2.
Using a hex wrench, unscrew and remove four handle
Cap Screws (44) and Lock Washers (45). Lift
assembled handle and handle Gasket (15) off Motor
Housing and set them aside.
3.
Lift motor Clamp Washer (16) off Housing.
4.
Move Reverse Lever (34) to center position and using
a drift pin to push from below, grasp Lever and lift
Reverse Valve Assembly (37) out of Housing.
Make certain the Lever is in the center position to
avoid jamming the Reverse Lock Plunger (35)
when the Reverse Valve Assembly is removed.
5.
Pull Lever off Reverse Valve and remove Reverse
Valve Bushing Seal (38) from groove on the Valve.
Содержание 2934B2SP
Страница 10: ...MAINTENANCE SECTION 10 Dwg TPA1249 2...
Страница 19: ...19...