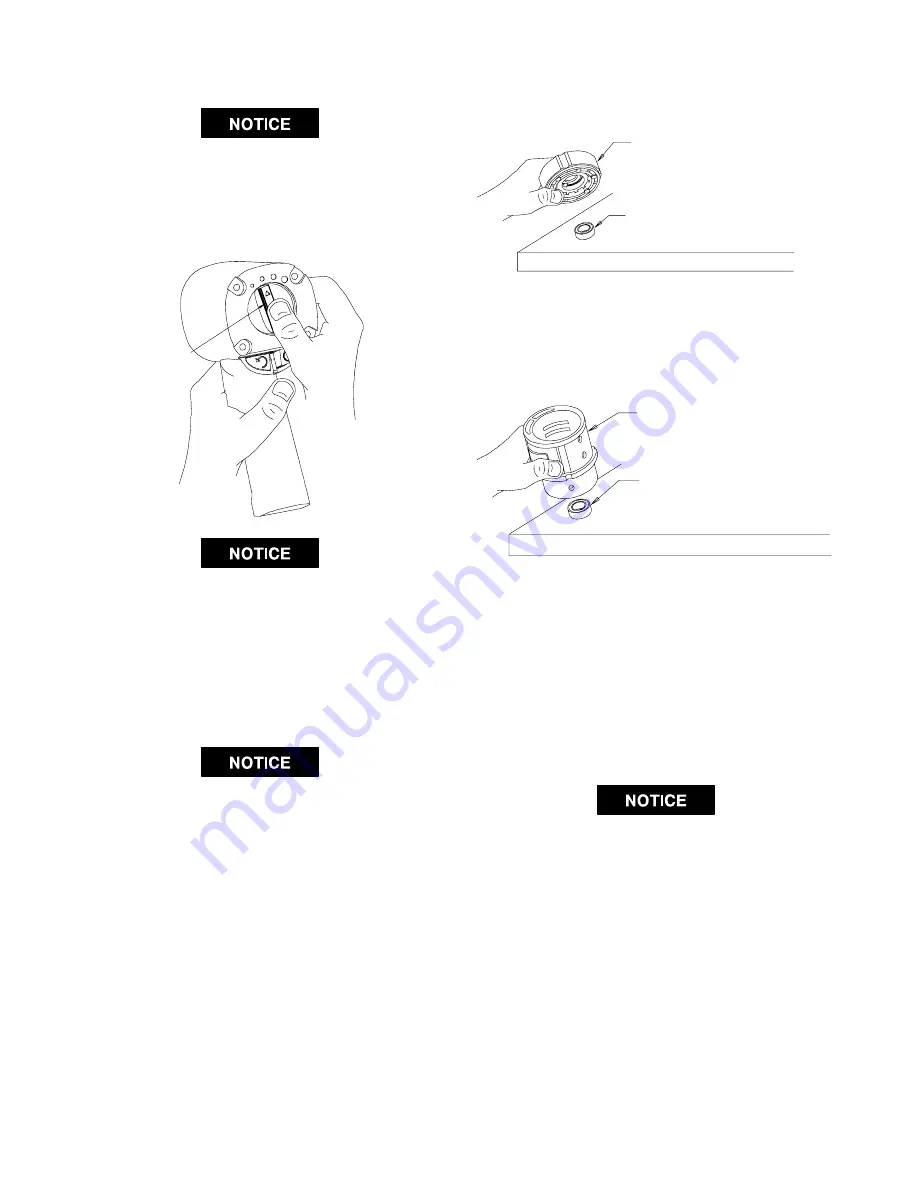
10
MAINTENANCE SECTION
Disassembly of the Motor
When pulling, disassembling or assembling the
motor, we recommend replacement of the Motor
Gasket (7).
1.
Remove the Motor Assembly from the Housing (17)
by pushing on the Power Management Dial (32) from
the back of the Housing. Refer to Dwg. TPDD1322.
POWER
MANAGEMENT
DIAL
(Dwg. TPD1322)
If the Motor Assembly cannot be removed from the
Housing by pushing, tap the Power Management
Dial lightly until the Motor Assembly is free.
2.
Remove the Power Management Dial from the rear of
the Cylinder (1). Remove the Power Management
Dial Seal (33) if it needs to be replaced.
3.
Remove the Front End Plate (2) from the Cylinder by
tapping the splined end of the Rotor (5) with a plastic
hammer.
To prevent damage to the Cylinder, do not tap or
strike Cylinder on a hard or metallic surface when
removing the Rotor Bearings (3) and (3A).
To remove the Front Rotor Bearing, hold the Front
End Plate with Front Rotor Bearing down and tap the
Front End Plate on a flat, nonmetallic surface such as
a work bench. This will loosen the Front Rotor
Bearing so that it will drop out of the Front End Plate.
Refer to Dwg. TPD1323.
(Dwg. TPD1323)
FRONT END PLATE
FRONT ROTOR BEARING
BENCH WITH NONMETALLIC SURFACE
4.
Remove the Rear Rotor Bearing Retainer (6) from the
rear of the Rotor (5). The Rotor can now be removed
from the Cylinder. Remove the Vanes (4) from the
Rotor if they need to be replaced.
CYLINDER
REAR ROTOR BEARING
(Dwg. TPD1324)
BENCH WITH NONMETALLIC SURFACE
5.
To remove the Rear Rotor Bearing, hold the Cylinder
with the Rear Rotor Bearing down and tap the
Cylinder on a flat, nonmetallic surface such as a work
bench. This will loosen the Rear Rotor Bearing so that
it will drop out of the Cylinder. Refer to Dwg.
TPD1324.
6.
Working from the rear of the Housing, push out the
Motor Gasket (7).
When removing the Motor Gasket, do not use a
screwdriver or any other sharp object which could
damage the Gasket and/or Housing.