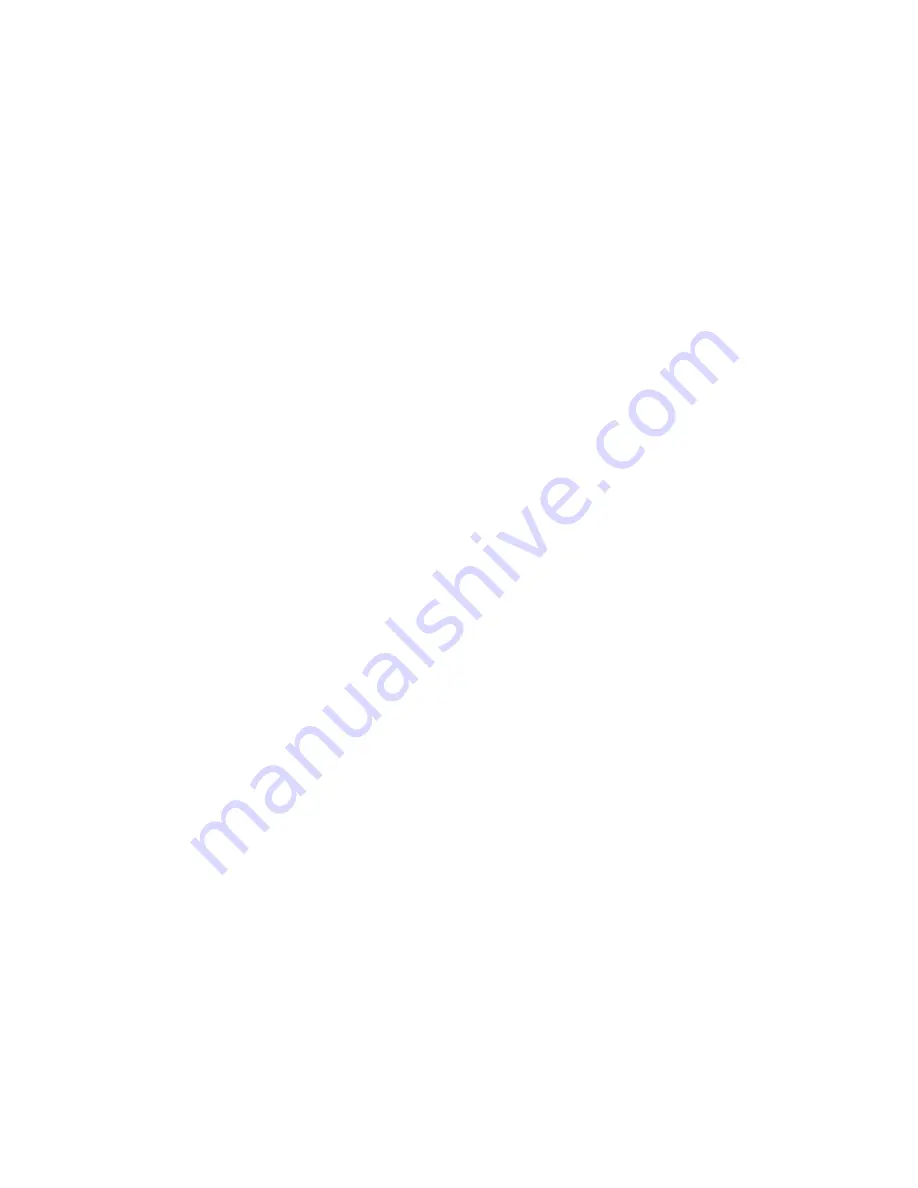
25
General Disassembly
The following instructions provide the necessary information to
disassemble, inspect, repair, and assemble the winch. An
exploded drawing of the winch is provided in the Parts Section
to assist part identification. If a winch is being completely
disassembled for any reason, follow the order of the topics as
they are presented. It is recommended that all maintenance work
on the winch be performed in a clean dust free work area.
In the process of disassembling the winch, observe the
following:
1.
Never disassemble the winch any further than is necessary
to accomplish the needed repair. A good part can be
damaged during the course of disassembly.
2.
Never use excessive force when removing parts. Tapping
gently around the perimeter of a part with a soft hammer
should be sufficient to loosen the part.
3.
Do not heat a part with a flame to free it for removal, unless
the part being heated is already worn or damaged beyond
repair and no additional damage will occur to other parts.
In general, the winch is designed to permit easy disassembly and
assembly. The use of heat or excessive force should not be
required.
4.
Keep the work area as clean as practical, to prevent dirt and
other foreign matter from getting into bearings or other
moving parts.
Winch Disassembly (chain driven winches)
Refer to Drawing MHP0255.
Disconnect all power to the winch before starting disassembly.
Remove wire rope and limit switches if equipped.
1.
Remove capscrews (15), screws (16), washers (18) and nuts
(24) and lift off guard (3).
2.
Remove chain (6).
3.
Loosen setscrews (32) and remove sprocket (5) and key
(31) from motor and reducer assembly output shaft.
4.
Remove capscrews (17), lockwashers (21), washers (12)
and nuts (22). Using an overhead hoist with sufficient
capacity to adequately support the weight of the motor and
reducer assembly remove the motor and reducer assembly
from frame (1).
5.
Remove capscrews (9) and lockwashers (25) and lift off
caps (8).
6.
Remove adjusting screws (11) and nuts (20) from frame (1).
7.
Support the drum (2) using an overhead hoist with
sufficient capacity to adequately handle the weight of the
drum. Remove nuts (19) and lockwashers (13). Pull
bearings (7) from drum spigots.
8.
Lift drum (2) from frame (1) and carefully set in an area
which will not cause damage to the sprocket teeth.
9.
Remove bolt locks (4) and capscrews (14) from frame (1).
Winch Disassembly
15,000 - 25,000 lb winches
Refer to Drawings MHP0255 and MHP0278.
1.
Remove capscrews (15), screws (16), washers (18) and nuts
(24) and lift off guard (3).
2.
Remove chain (6).
3.
Loosen setscrews (32) and remove sprocket (5) and key
(31) from motor and reducer assembly output shaft.
4.
Remove capscrews (45), lockwashers (46) and nuts (47)
from bearing (40).
5.
Remove capscrews (17), lockwashers (21), washers (12) and
nuts (22). Using an overhead hoist with sufficient capacity to
adequately support the weight of the motor and reducer
assembly remove the motor and reducer assembly from frame
(1). Slide bearing (40) from motor and reducer assembly.
6.
Remove adjusting screws (11) and nuts (20) from frame (1).
7.
Remove capscrews (41), washers (42), lockwashers (48)
and nuts (43) from bearings (39).
8.
Lift drum (2) from frame (1) and carefully set in an area
which will not cause damage to the sprocket teeth. Pull
bearings (39) from drum spigots.
Winch Disassembly (direct drive winches)
Refer to Drawing MHP0260.
1.
Remove nuts (60) and lockwashers (59). Pull bearing (58)
from drum hub.
2.
Remove nuts (53), lockwashers (54) and capscrews (56)
from motor and frame (50).
3.
Slide the motor and drum assembly away from bearing (58)
until drum spigot is clear of the frame (50).
4.
Remove drum (51) from reducer assembly drive shaft.
Limit Switch Disassembly (optional feature)
Refer to Drawings MHP0263 and MHP0579.
1.
Remove screws (74) and lockwashers (73). Lift limit switch
(72) from bracket (71).
2.
Remove nuts (19) and lockwashers (13) from extension
studs (70). Remove bracket (71) and extension studs (70).
3.
Tap pin (75) out of drum only if it requires replacement.
On 15000B20 and 25000B25 winches, bracket (71) can only be
removed after capscrews (41), washers (42), lockwashers (48)
and nuts (43), that retain bearing (39), have been removed.
Cleaning, Inspection and Repair
Use the following procedures to clean, inspect, and repair the
components of the winch.
Cleaning
Clean all winch component parts in solvent. The use of a stiff
bristle brush will facilitate the removal of accumulated dirt and
sediments on the sprockets, frame and drum. Dry each part using
low pressure, filtered compressed air.
Inspection
All disassembled parts should be inspected to determine their
fitness for continued use. Pay particular attention to the
following:
1.
Inspect sprockets for worn, cracked, or broken teeth.
2.
Inspect all bearings for wear, scoring, or galling. Check for
freeness of rotation. Replace bearings if rotation is rough or
bearings are excessively worn.
3.
Inspect shafts for ridges caused by wear. If ridges caused
by wear are apparent on shafts, replace the shaft.
4.
Inspect all threaded items and replace those having
damaged threads.
5.
Check guard for damage and that it provides suitable
protection from the roller chain and sprockets.
6.
Inspect chain to ensure it is clean and free from rust. Refer
to “LUBRICATION” section for information on cleaning
and lubricating chain.
Содержание 10000B20
Страница 13: ...12 DRUM SWITCH CONNECTION DIAGRAMS Dwg MHP0201...
Страница 14: ...13 230 Volt Single Phase 60 Hz Dwg MHP0271 WIRING DIAGRAM...
Страница 15: ...14 WIRING DIAGRAMS Dwg MHP1086...
Страница 16: ...15 Dwg MHP1087 WIRING DIAGRAM 208 575 Volt Three Phase 50 or 60 Hz 22 Amp and smaller...
Страница 17: ...16 WIRING DIAGRAM Dwg MHP1088 208 575 Volt Three Phase 50 or 60 Hz 22 Amp and larger...
Страница 41: ...40 6 000 lb to 25 000 lb winches TORQUE LIMITER ASSEMBLY PARTS DRAWING OPTIONAL FEATURE Dwg MHP0583...