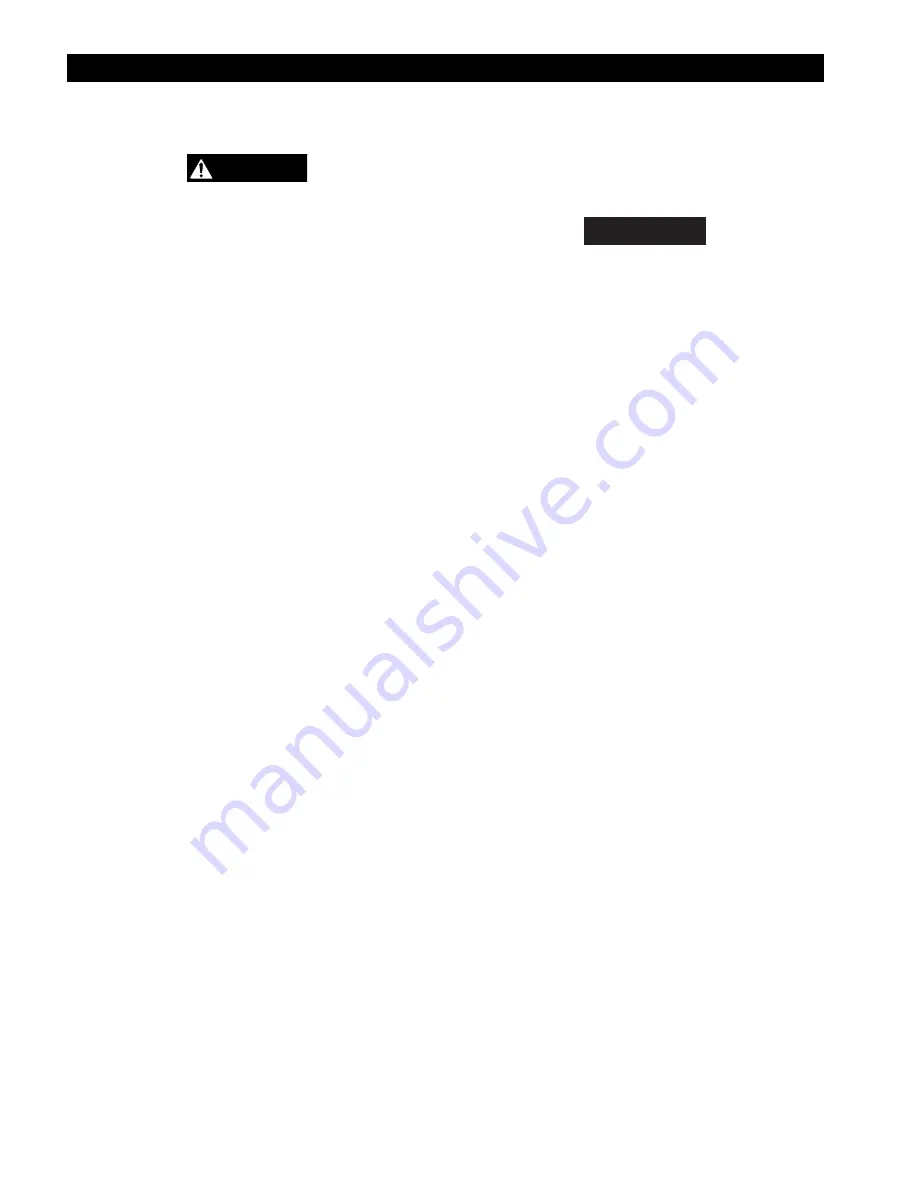
18
INSPECTION
such as kinking, “birdcaging”, core protrusion, main strand
displacement, corrosion, broken or cut strands. If damage is
evident, do not operate winch until the discrepancies have
been reviewed and inspected further by personnel familiar
with wire rope maintenance. Lubricate if necessary. Refer
to “LUBRICATION” section.
NOTICE
• The full extent of wire rope wear cannot be determined by
visual inspection. At any indication of wear, inspect the wire
rope in accordance with instructions in “Periodic
Inspection.”
3.
BRAKE. During winch operation test brake. Brake must
hold load without slipping. Brake must release when winch
motor is operated. If brake does not hold load, or does not
release properly, the brake must be adjusted or repaired.
4.
WIRE ROPE REEVING. Check reeving and ensure wire
rope is properly secured to the drum. Do not operate the
winch unless the wire rope feeds onto the drum smoothly.
5.
LUBRICATION. Refer to the “LUBRICATION” section
for recommended procedures and lubricants.
6.
PENDANT (optional feature). Ensure operation of pendant
buttons is smooth and that winch is responsive to pendant
control. Pendant buttons must spring return to a position
flush with the pendant housing when released.
7.
LIMIT DEVICES (optional feature). Check that they are
correctly adjusted and operate properly.
Periodic Inspection
Periodic inspection intervals for winch use under various
conditions are listed below:
NORMAL
HEAVY
SEVERE
yearly
semiannually
quarterly
Disassembly may be required as a result of frequent inspection
findings or in order to properly inspect the individual
components. Disassembly steps are described in the
“MAINTENANCE” section. Maintain written records of
periodic inspections to provide an accumulative basis for
continuing evaluation. Inspect all items listed in “Frequent
Inspection”. Also inspect the following:
1.
FRAME. Check for deformed, cracked or corroded main
components. Replace damaged parts if necessary.
2.
FASTENERS. Check rivets, cotter pins, capscrews and nuts
on winch, including mounting bolts. Replace if missing and
tighten if loose.
3.
DRUM. Check for cracks, wear or damage. Replace if
necessary.
4.
ALL COMPONENTS. Inspect for wear, damage, distortion
and cleanliness. If external evidence indicates the need, for
example poor performance or excessive noise, disassemble
and inspect. Check pins, gears, shafts, bearings, sheaves,
covers, etc. Replace worn or damaged parts.
5.
MOTOR. Make sure motor operates properly and conforms
to applicable specifications. Check wiring connections are
clean, dry and secure.
6.
BRAKE. Check brake functions correctly. Only minimum
maintenance is required. Refer to “MAINTENANCE”
section for brake adjustment and repair.
Inspection information is based in part on American National
Standards Institute Safety Codes (ASME B30.7).
WARNING
• All new, altered or modified equipment should be inspected
and tested by personnel instructed in safety, operation and
maintenance of this equipment to ensure safe operation at
rated specifications before placing equipment in service.
• Never use a winch that inspection indicates has a potential
problem.
Frequent and periodic inspections should be performed on
equipment in regular service. Frequent inspections are visual
examinations performed by operators or personnel trained in
safety and operation of this equipment and include observations
made during routine equipment operation. Periodic inspections
are thorough inspections conducted by personnel trained in the
safety, operation and maintenance of this equipment. ASME
B30.7 states inspection intervals depend upon the nature of the
critical components of the equipment and the severity of usage.
Careful inspection on a regular basis will reveal potentially
dangerous conditions while still in the early stages, allowing
corrective action to be taken before the condition becomes
dangerous.
Deficiencies revealed through inspection, or noted during
operation, must be reported to designated personnel instructed in
safety, operation and maintenance of this equipment. A
determination as to whether a condition constitutes a safety
hazard must be decided, and the correction of noted safety
hazards accomplished and documented by written report before
placing the equipment in service.
Records and Reports
Inspection records, listing all points requiring periodic
inspection should be maintained for all load bearing equipment.
Written reports, based on severity of service, should be made on
the condition of critical parts as a method of documenting
periodic inspections. These reports should be dated, signed by
the person who performed the inspection, and kept on file where
they are readily available for authorized review.
Wire Rope Reports
Records should be maintained as part of a long-range wire rope
inspection program. Records should include the condition of
wire rope removed from service. Accurate records will establish
a relationship between visual observations noted during frequent
inspections and the actual condition of wire rope as determined
by periodic inspections.
Frequent Inspection
On winches in continuous service, frequent inspection should be
made at the beginning of each shift. In addition, visual
inspections by operators should be conducted during regular
operation for indications of damage or evidence of malfunction.
1.
WINCH. Prior to operation, visually inspect winch frame,
bearings, guards and drum for indications of damage. Any
discrepancies noted must be reviewed and inspected further
by authorized personnel instructed in the operation, safety
and maintenance of this winch.
2.
WIRE ROPE. Visually inspect all wire rope which can be
expected to be in use during the day’s operations. Inspect
for wear and damage indicated by distortion of wire rope
Содержание 10000B20
Страница 13: ...12 DRUM SWITCH CONNECTION DIAGRAMS Dwg MHP0201...
Страница 14: ...13 230 Volt Single Phase 60 Hz Dwg MHP0271 WIRING DIAGRAM...
Страница 15: ...14 WIRING DIAGRAMS Dwg MHP1086...
Страница 16: ...15 Dwg MHP1087 WIRING DIAGRAM 208 575 Volt Three Phase 50 or 60 Hz 22 Amp and smaller...
Страница 17: ...16 WIRING DIAGRAM Dwg MHP1088 208 575 Volt Three Phase 50 or 60 Hz 22 Amp and larger...
Страница 41: ...40 6 000 lb to 25 000 lb winches TORQUE LIMITER ASSEMBLY PARTS DRAWING OPTIONAL FEATURE Dwg MHP0583...