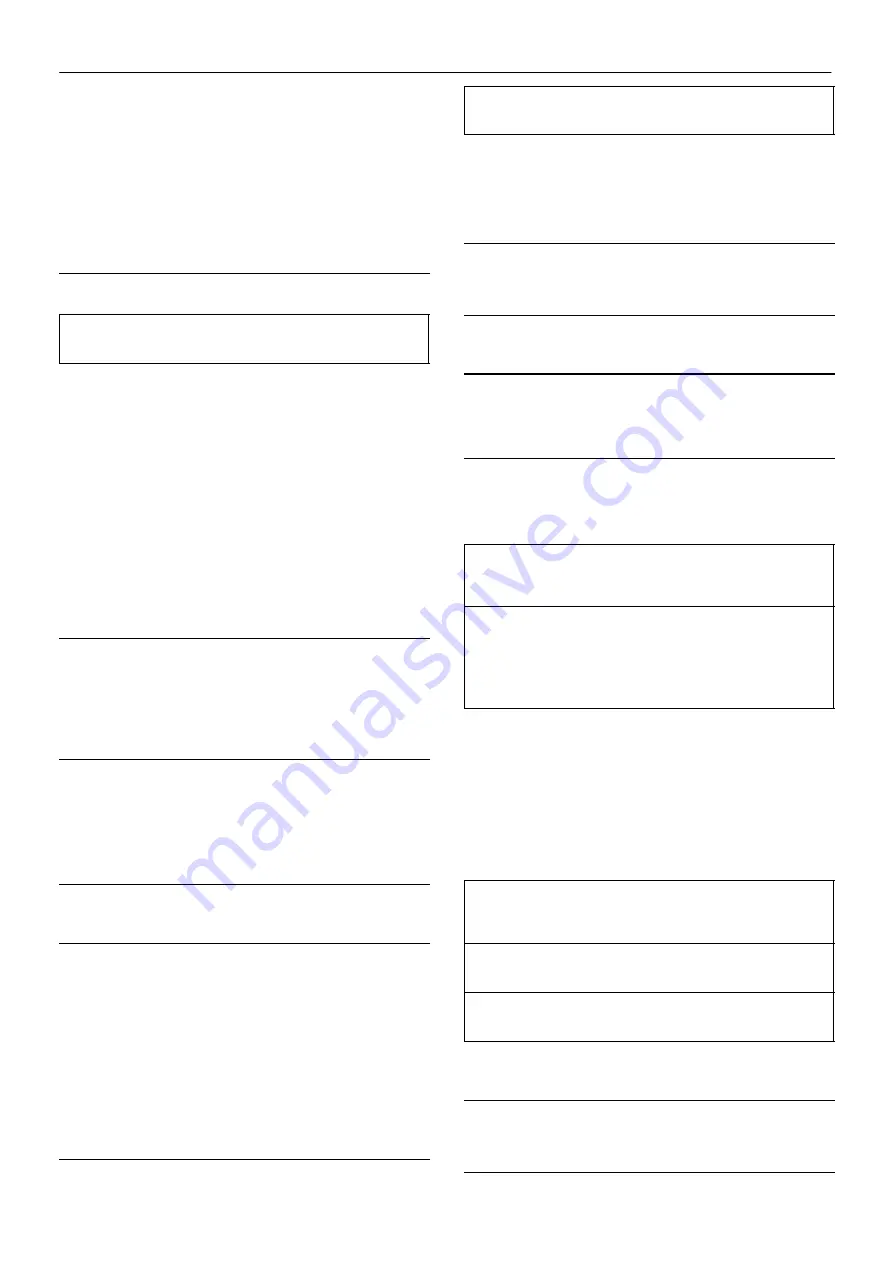
MAINTENANCE
26
9/215 9/230 9/255 9/300 10/170 12/170 12/235 17/235 21/215
HP600 VHP600 XP750 XP800 VHP825 XP900 XP1060 XHP760 XHP825
At the recommended intervals, (see the
SERVICE/MAINTENANCE CHART), inspect all of the intake lines to
the air filter, and all flexible hoses used for air lines, oil lines and fuel
lines.
Periodically inspect all pipework for cracks, leaks, etc. and replace
immediately if damaged.
ELECTRICAL SYSTEM
WARNING: Always disconnect the battery cables before
performing any maintenance or service.
Inspect the safety shutdown system switches and the instrument
panel relay contacts for evidence of arcing and pitting. Clean where
necessary.
Check the mechanical action of the components.
Check the security of electrical terminals on the switches and relays
i.e. nuts or screws loose, which may cause local hot spot oxidation.
Inspect the components and wiring for signs of overheating i.e.
discolouration, charring of cables, deformation of parts, acrid smells
and blistered paint.
BATTERY
Keep the battery terminals and cable clamps clean and lightly
coated with petroleum jelly to prevent corrosion.
The retaining clamp should be kept tight enough to prevent the
battery from moving.
PRESSURE SYSTEM
At 500 hour intervals it is necessary to inspect the external surfaces
of the system (from the airend through to the discharge valve(s))
including hoses, tubes, tube fittings and the separator tank, for visible
signs of impact damage, excessive corrosion, abrasion, tightness and
chafing. Any suspect parts should be replaced before the machine is
put back into service.
TYRES/TYRE PRESSURE
See the GENERAL INFORMATION section of this manual.
RUNNING GEAR/WHEELS
Check the wheel nut torque 20 miles (30 kilometres) after refitting
the wheels. Refer to the TORQUE SETTING TABLE later in this
section.
The bolts securing the running gear to the chassis should be
checked periodically for tightness (refer to the
SERVICE/MAINTENANCE CHART for frequency) and re–tightened
where necessary. Refer to the TORQUE SETTING TABLE later in this
section.
LUBRICATION
The engine is initially supplied with engine oil sufficient for a nominal
period of operation (for more information, consult The Engine
Manufacturer’s Manual).
CAUTION: Always check the oil levels before a new machine is put into
service.
If, for any reason, the unit has been drained, it must be re–filled with
new oil before it is put into operation.
ENGINE LUBRICATING OIL
The engine oil should be changed at the engine manufacturer’s
recommended intervals. Refer to the Engine Manufacturer’s Manual.
ENGINE LUBRICATING OIL SPECIFICATION
Refer to the Engine Manufacturer’s Manual.
ENGINE OIL FILTER ELEMENT
The engine oil filter element should be changed at the engine
manufacturer’s recommended intervals. Refer to the Engine
Manufacturer’s Manual.
COMPRESSOR LUBRICATING OIL
Refer to the SERVICE/MAINTENANCE CHART in this section for
service intervals.
NOTE: If the machine has been operating under adverse conditions,
or has suffered long shutdown periods, then more frequent service
intervals will be required.
WARNING: DO NOT, under any circumstances, remove any drain
plugs or the oil filler plug from the compressor lubricating and
cooling system without first making sure that the machine is
stopped and the system has been completely relieved of all air
pressure (refer to STOPPING THE UNIT in the OPERATING
INSTRUCTIONS section of this manual).
Completely drain the receiver/separator system including the piping
and oil cooler by removing the drain plug(s) and collecting the used oil
in a suitable container.
Replace the drain plug(s) ensuring that each one is secure.
NOTE: If the oil is drained immediately after the machine has been
running, then most of the sediment will be in suspension and will
therefore drain more readily.
CAUTION: Some oil mixtures are incompatible and result in the
formation of varnishes, shellacs or lacquers which may be insoluble.
NOTE: Always specify INGERSOLL–RAND Pro–Tec
TM
oil for use
at all ambient temperatures above –23
C.
COMPRESSOR OIL FILTER ELEMENT
Refer to the SERVICE / MAINTENANCE CHART in this section for
service intervals.
RUNNING GEAR WHEEL BEARINGS
Wheel bearings should be packed with grease every 6 months. The
type of grease used should conform to specification MIL–G–10924.