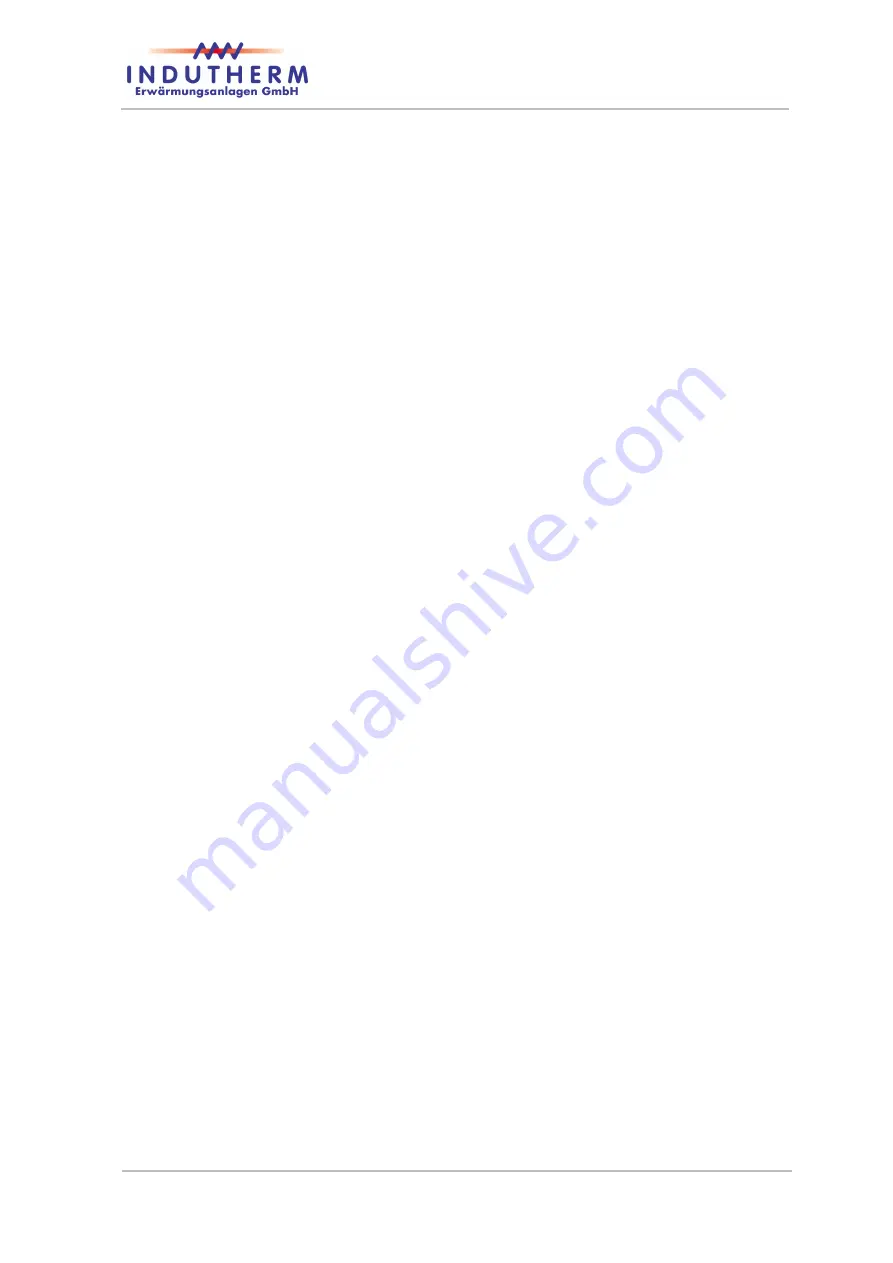
System
description
[email protected] | www.romanoff.com
2019-10-16
4
–10
4.7
Functional description
With the casting machine, castings of different dimensions can be
produced from the metals to be used as intended. For this purpose,
the casting material is first melted inductively under a protective gas
atmosphere and then poured into a flask or into a mould.
The advantage of the inductive heating is the rapid attainment of the
melting temperature, since the heat is generated directly in the melt
material and in the crucible. Likewise, the metal is thoroughly mixed
through the magnetic field during the melting process, so that homo-
geneous metal mixing is achieved even in new alloys.
The built-in thermocouple is used to precisely measure the tempera-
ture and to control the power of the unit so that the set temperature is
kept constant.
The material is melted as standard with protective gas purge. For
metals, which are more susceptible to oxidation, it is recommended to
draw vacuum after the material has been filled, and subsequently to
return with protective gas. In addition, in the case of metals with a
high oxygen content (eg commercially available copper or silver), de-
gassing of the molten metal under vacuum is possible.
The INDUTHERM mini casting machine MC16 is suitable to cast all
kind of metals into moulds or into investment flasks. Exceptions are
dental alloys and very reactive alloys like magnesium. The melting
charge is heated up by induction. The special advantage of strong in-
ductive heating is that the melting temperature is reached rapidly, be-
cause the heat is directly generated in the metal or will transported to
the metal by a crucible with graphite insert. During the melting pro-
cess, the metal is thoroughly mixed by means of a magnetic field, en-
suring a homogenous mixing even when using mixtures of pure met-
als.
Crucibles with graphite inlet are used for metals up to 1300 °C and
ceramic crucibles for steel or platinum up to 2000 °C.
Vacuum-Pressure mode in only one chamber
The casting mode is based on this new method: during the melting
process the metal and the flask are under full vacuum. The metal is
poured into the flask by tilting the whole chamber. Inside flask is also
a vacuum which guarantees pouring without air counter pressure.
Now the vacuum will be replaced by gas overpressure rapidly: The
pressure impulse (inside of the flask is still under vacuum!) ensures
excellent form filling. The effect of vacuum in the flask and outside
overpressure lasts for some time, long enough until metal is already
solid.
The most important fact of this system is quickly creating of vacuum
and very fast pressure built-up in the system. To the evacuate cham-
ber it needs a strong vac pump with 8 m³/h minimum, releasing vacu-
um + creating over pressure it needs a gas bottle with PRESSURE
regulator (NEVER a flow regulator !!!). Short connection pipes make
rapid pressure supply even better.