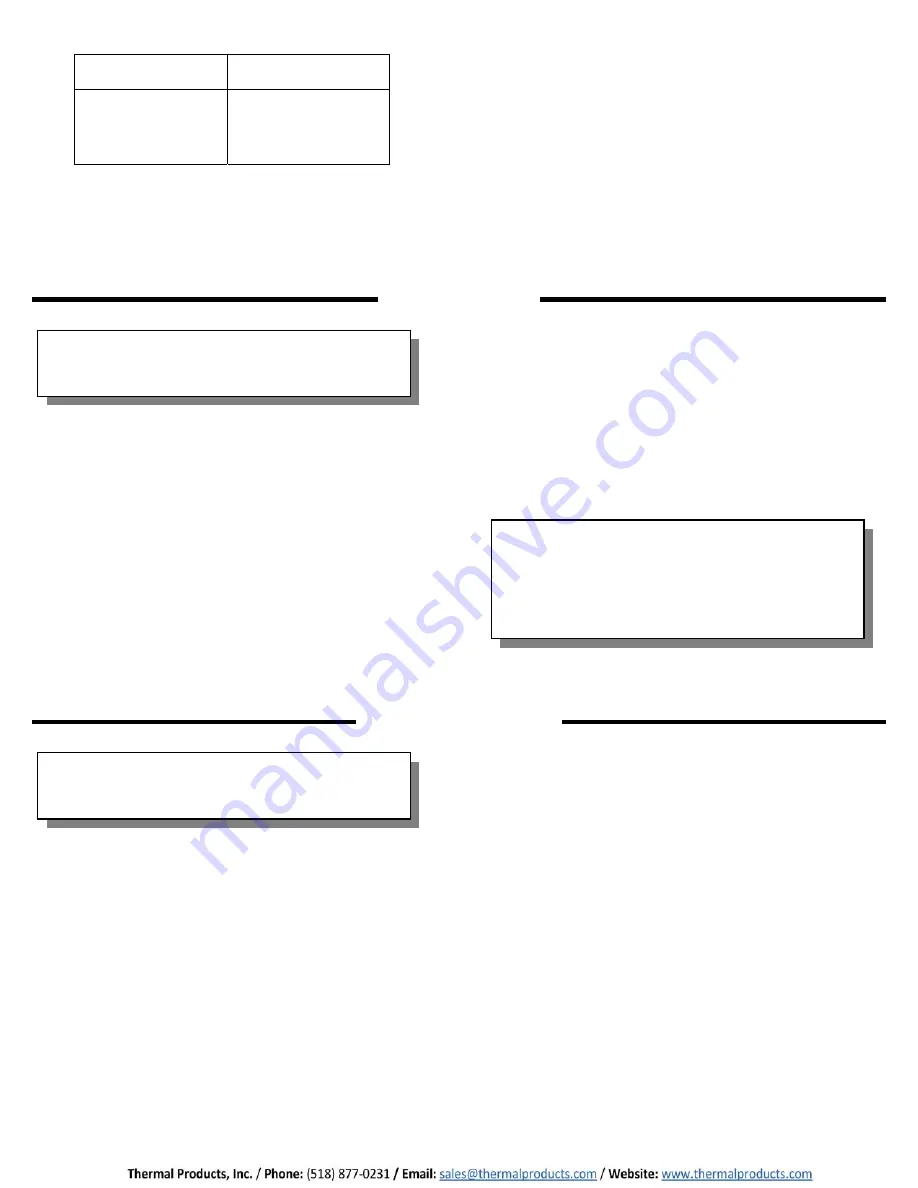
4
Sheath
Material
Maximum
Sheath Temperature
Copper
350
q
F
Steel
750
q
F
Stainless Steel 304
1400
q
F
Incoloy 800
1600
q
F
DO NOT
operate heaters at flow rates below the design
flow range. Reduced flow can shorten heater life, cause
nuisance tripping of thermal safeties, or potentially exceed
vessel shell design temperatures. Note that heaters with
SCR control can typically operate at reduced flows down to
1/10
th
of the design flow if the controller is properly tuned,
and over-temperature safety devices are set at an
appropriate point to protect the heater and fluid.
INDEECO recommends that all safety interlocks are tested
during initial startup to ensure they properly disable the
heater. After 10 days of operation, retighten all electrical
connections.
On Flanged Immersion heaters, re-tighten heater flange
bolts after the heater has completed one or two heating
cycles.
MAINTENANCE
Periodically check all electrical connections, including field
and factory-made connections for tightness, and all wiring
for deterioration at least once a year.
Periodically inspect for leakage and retighten Immersion
Heater flange bolts when required.
Inspect the terminal enclosure and conduit connections for
evidence of water leaks or moisture collection. Tighten
connections as required. Clean up any corrosion. Do not
continue using a heater with signs of damage.
Where the heater is installed in cold climates, consider
safety precautions to prevent damage due to freezing fluid
when the heater is not in service.
Where buildup of solids on the heating elements or
significant corrosion is expected, periodically remove the
Immersion Heater to inspect the vessel and heating
elements. Do not continue using a heater with signs of
damage. Before removing, note the orientation of the
flange or pipe plug relative to the vessel. Place a reference
mark on the vessel and Immersion Heater or use other
methods, such as drawing a sketch showing the conduit
hub orientation, to ensure proper orientation when re-
installing.
TROUBLESHOOTING
The nature of the magnesium oxide used to electrically
isolate the nickel chromium resistance wire in the heating
elements is such that over a long period of storage, they will
absorb considerable moisture from the atmosphere unless
hermetically sealed. It is recommended to perform an
insulation resistance test prior to energizing the equipment.
If the value is less than 1 Meg Ohm using a 500Vdc or
similar tester, care must be taken to dry out the heater to
prevent failure. It is recommended that the elements be
turned on at a reduced voltage at first to boil off the
moisture. Meg Ohm readings may drop initially after a few
minutes of operation, indicating moisture being forced out of
the elements. The terminal enclosure lid should be left
open during this period to allow the moisture to escape.
If the heater has a manual-reset high limit thermostat, be
sure that the reset button is pressed in.
The heating elements are not field-repairable. The only
recommended field repairs are to remove and replace the
faulty Immersion Heater, or to return the heater to the
factory for repair. Refer to instruction manual 72-2010-83 or
70-2010-83 for details on the Immersion Heater.
If reduced heat output is suspected, verify the condition of
the heating elements by using an ammeter to check the
current draw of each input line. All input lines should draw
approximately equal current, which should agree with
nameplate rating. If they do not, one or more of the heating
elements could be damaged.
CAUTION
Troubleshooting and repair should only be
attempted by qualified maintenance personnel.
CAUTION
Troubleshooting and repairs should only be
attempted by qualified maintenance personnel.
CAUTION
Immersion Heaters with cross-baffles or over-
temperature thermocouples are specifically oriented
to match the vessel. Do not rotate the Immersion
Heater without consulting with the factory.