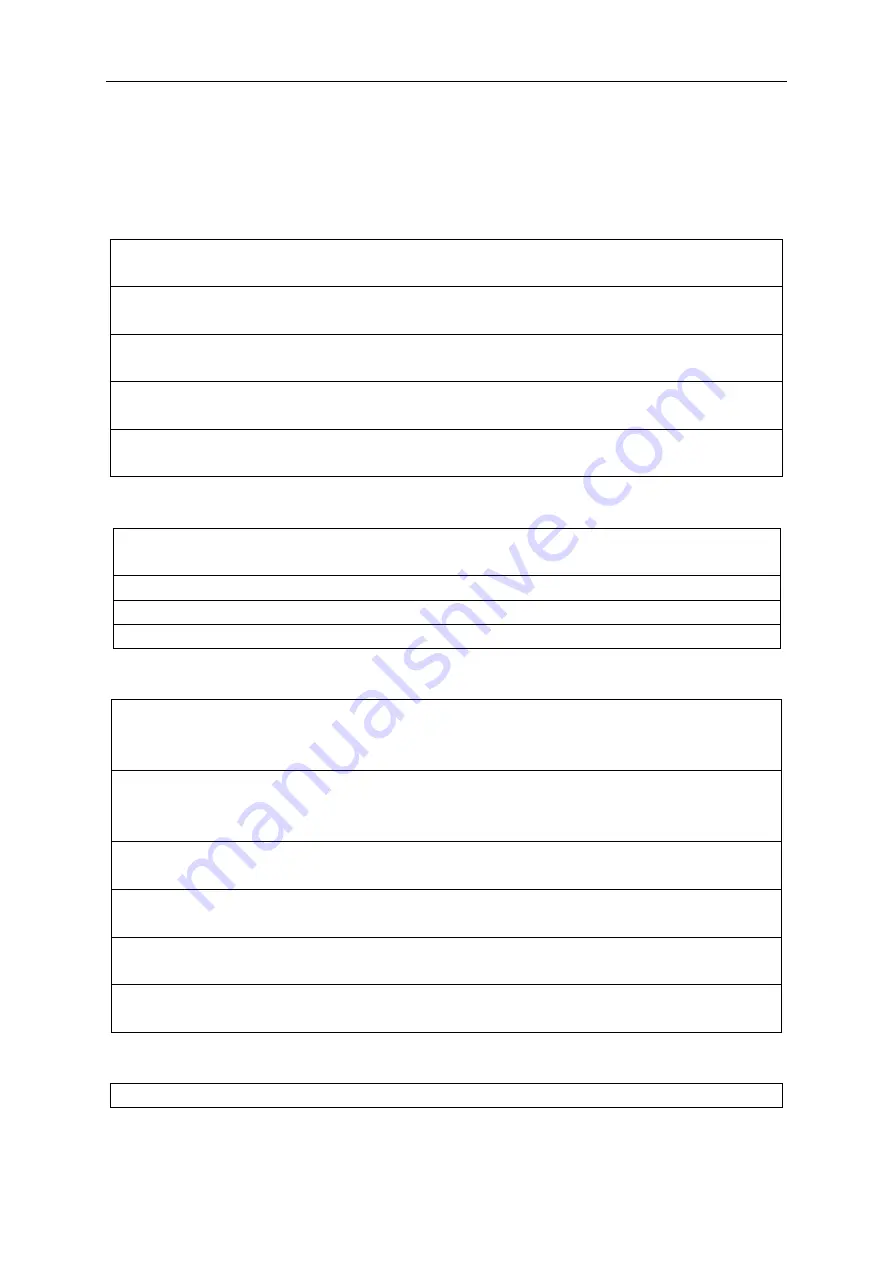
iDrive2 inverters Product overview
7
2 Product overview
2.1 Quick start-up
2.1.1 Unpacking inspection
Check as followings after receiving products:
1. Check that there is no physical or water damage to the package. Contact supplier immediately if received
damaged.
2. Check the information on the type designation label on the outside of the package to verify that the drive is
of the correct type. If not, contact supplier immediately.
3. Check that there are no signs of water in the package and no signs of damage or breach to the inverter.
Contact supplier immediately if any damage.
4. Check the information on the type designation label on the outside of the package to verify that the name
plate is of the correct type. If not, contact supplier immediately.
5. Check to ensure the accessories (including user’s manual and control keypad) inside the device is
complete. If not, contact supplier immediately.
2.1.2 Application confirmation
Check the machine before beginning to use the inverter:
1. Check the load type to verify that there is no overload of the inverter during work and check the drive is the
correct power rating.
2. Check that the actual current of the motor is equal to or less than the rated current of the inverter.
3. Check that the control accuracy of the load is the same of the inverter.
4. Check that the incoming supply voltage is correspondent to the rated voltage of the inverter.
2.1.3 Environment
Check as followings before the actual installation and usage:
1. Check that the ambient temperature of the inverter is below 40
℃
. If exceeds, derate 3% for every additional
1
℃
. Additionally, the inverter can not be used if the ambient temperature is above 50
℃
.
Note: for the cabinet inverter, the ambient temperature means the air temperature inside the cabinet.
2. Check that the ambient temperature of the inverter in actual usage is above -10
℃
. If not, add heating
facilities.
Note: for the cabinet inverter, the ambient temperature means the air temperature inside the cabinet.
3. Check that the altitude of the actual usage site is below 1000m. If exceeds, derate1% for every additional
100m.
4. Check that the humidity of the actual usage site is below 90% and condensation is not allowed. If not, add
additional ant-condensation heaters.
5. Check that the actual usage site is away from direct sunlight and foreign objects can not enter the inverter. If
not, add additional protective measures.
6. Check that there is no conductive dust or flammable gas in the vicinity of the drive. If not, add additional
protection to inverters.
2.1.4 Installation confirmation
Check as followings after the installation:
1. Check that the load range of the input and output cables meet the need of actual load.