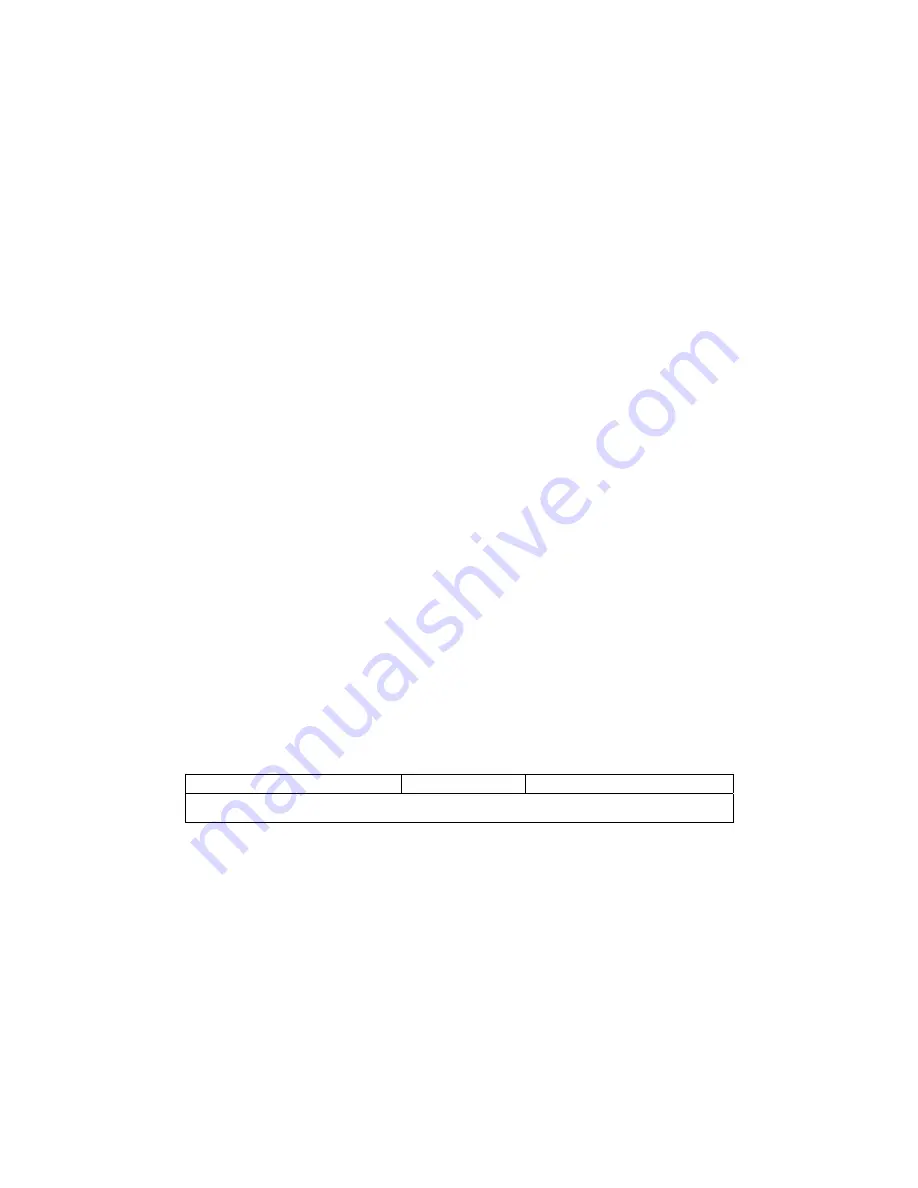
7
8. Disassemble power rotor (63) as follows: See Figure 2 for seal drawing.
a. Using a flat nosed tool, such as a screw driver, remove Truarc rings (42) located on
both sides of ball bearing (49) from grooves in power rotor (63).
b. Sealed ball bearing (49) is assembled to power rotor (63) with a light press fit. Ball
bearing (49) may be removed by using a bearing puller or a vertical arbor press.
When using press, two pieces of key stock are to be placed through openings of
mechanical seal seat adapter (48) underneath ball bearing (49) on both sides of
power rotor shaft. Key stock should be long enough to support power rotor (63) as it
is placed in press. Press ram is to be positioned against power rotor (63) coupling
end face. Gently press power rotor (63) through ball bearing (49). Ensure power
rotor (63) does not fall to floor once ball bearing (49) is off of its diameter.
c. Remove seal seat adapter (48) from power rotor (63), then remove mechanical seal
stationary seat from seal seat adapter (48). Loosen set screws on mechanical seal
rotating assembly body and remove from power rotor (63). Remove spacer (38) from
the power rotor (63).
9. Remove O-ring (83) from inboard end cover (46).
10. Remove bolts (4) and inboard cover (46) from case (1). (On size 400, C-face unit
removal of inboard cover (46) also removes balance piston spacer (93) and BP spacer
installation bolts (94). These two parts need not be removed from balance piston since
they are not wearing parts and will not be supplied with major kit.)
11. Remove O-ring (28 or 9) from inboard cover (46).
12. Remove idler stop (22) from inboard cover (46) by removing bolts (81).
13. Remove floating balance piston (79) from inboard cover (46).
14. Remove stop pin (6) and Dyna seal (7) from case (1).
15. Remove housing snap rings (8) from case (1).
16. Remove housing (24) from case (1) and O-ring (28) from housing (24).
CAUTION
Do not permit housing (24) to drop as it is removed from pump.
H.4 PUMP ASSEMBLY PROCEDURE
Note:
Prior to reassembly of pump, all parts should be cleaned and inspected for nicks
and burrs. Replace all worn or damaged parts. Imo Pump recommends
replacement of all O-rings (9, 27, 28, 83), Dyna Seal (7), mechanical seal (25) and
ball bearing (49) when these parts are disturbed from their previously installed
positions. Coat all parts with light lubricating oil to assist in assembly.
Note:
Bolts (81) have Nylok threads. Torque stated on appropriate assembly drawing for
bolt (81) does not include additional torque to install fasteners containing nylok
inserts. Torque required for first application is much higher than for subsequent
applications. To ensure required preload on Nylok fastener is achieved for each
application, following procedure is mandatory assembly practice.