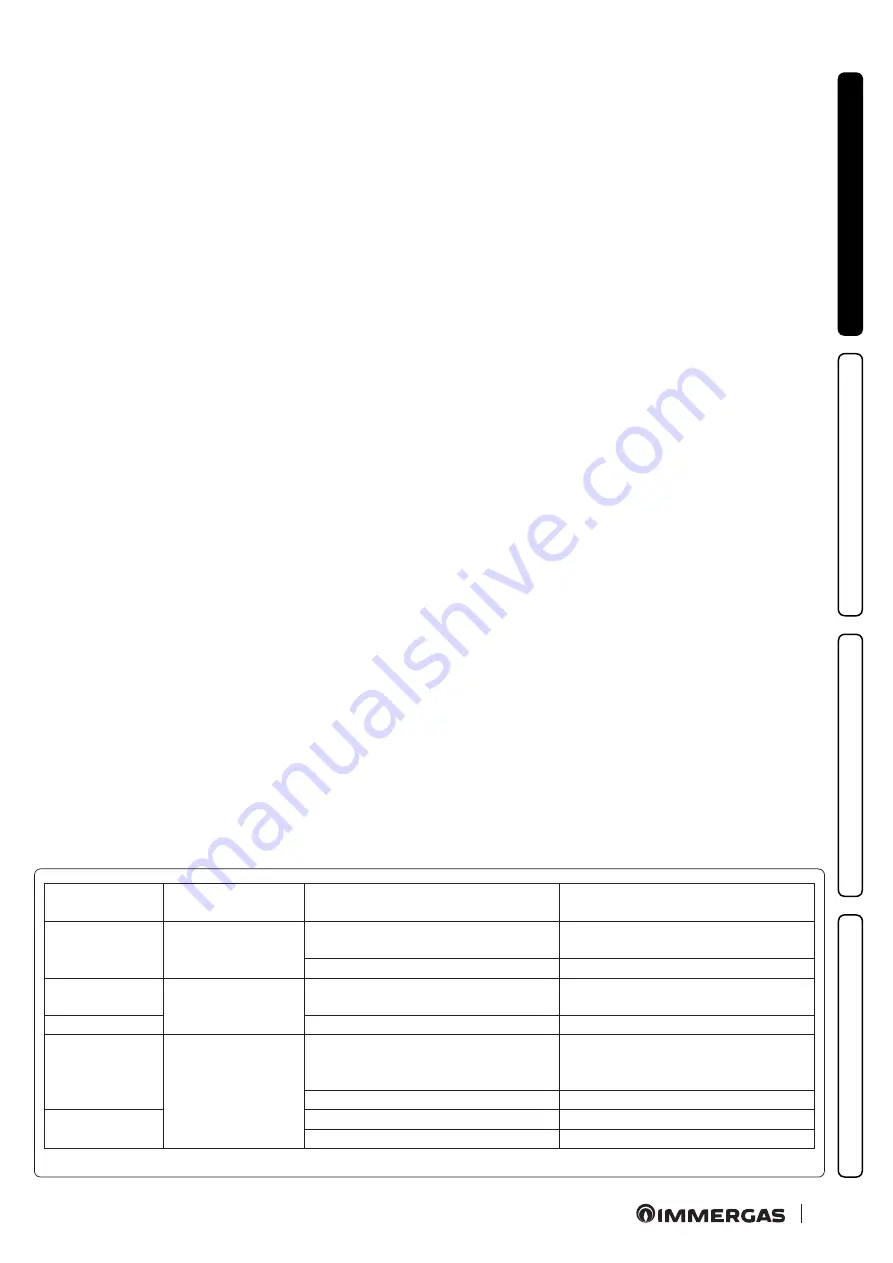
11
7
INS
TALLER
US
ER
MAINTEN
AN
CE
TECHNI
CI
AN
TECHNI
CAL
D
AT
A
- MIN. - MAX. program (blue LED).
The pump is distinguished
by adjustable operating curves by positioning the selector in any
point between the Min. and Max. positions, thereby satisfying
any installation requirement (from a simple single-pipe to more
modern and sophisticated systems) and always guaranteeing op-
timum performance. The precise working point can be selected
in the entire field of use by gradually adjusting the speed.
Real-time diagnostics:
a lit LED (in various colours) provides
information regarding the pump operating status, see fig. 7.
Possible pump release.
The pump block is indicated by a fixed
red LED switching on. Turn the selector up to the MAX. position,
disconnect and reconnect the power to restart the automatic re-
lease process. The pump will then activate the procedure, which
will last for a maximum of 15 minutes and the LED will flash upon
each restart. It then turns blue for a few seconds and goes back to
red if the attempt to restart is not successful. Once the process is
complete, position the selector back on the desired curve and if
the problem has not been resolved, perform the manual release
procedure as described below.
- Disconnect the power to the boiler (the LED switches off).
- Close the system flow and return and allow the pump to cool
down.
- Empty the system circuit via the relative cock.
- Remove the motor and clean the impeller.
- Once unblocked, remount the motor.
- Fill the primary circuit; restore boiler power and set the desired
curve.
Attention:
a scalding hazard is present due to high fluid tem-
peratures and pressures.
Scalding hazard as a result of contact.
Circulating
pump LED
Description
Diagnostics
Remedy
LED steady on
Pump
noisy
Insufficient system pressure, circulating
pump in cavitation
Restore correct thermal circuit pressure
Presence of foreign matter in the impeller Remove the motor and clean the impeller
Flashing white
LED
Noises during cir-
culation of the heat
transfer fluid
Presence of air in the system
Vent the system
LED steady on
Flow rate too high
Reduce rotation speed
LED off
The circulator does
not work
Power outage
Ensure the boiler is correctly powered,
ensure the circulator is correctly pow-
ered
Faulty circulating pump
Replace the circulating pump
Red LED
Rotor seized
Remove the motor and clean the impeller
Insufficient power supply voltage
Check boiler power supply voltage
1.9 SIZING THE SYSTEMS.
The flow temperatures to the various system zones may be re-
duced with respect to the boiler outlet temperatures, according
to the mixture of the flow and return fluids inside the DIM ERP.
In the event that the DIM ERP is used to feed Low-Temperature
zones, check that the design parameters allow you to achieve a
maximum surface temperature of the radiant floor in compliance
with standard in force.
1.10 KITS AVAILABLE ON REQUEST.
• System cut-off cock kit (on request). The manifold is designed
for the installation of system interception cocks, to be placed on
the flow and return pipes of the connection assembly. This kit is
particularly useful for maintenance as it allows the DIM ERP to
be drained separately without having to empty the entire system.
• External probe kit.
• Safety thermostat kit.
The above-mentioned kits are supplied complete with instructions
for assembly and use.